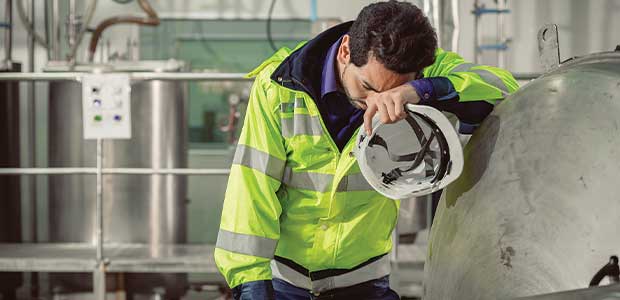
Personal Protective Equipment: The Pains of Staying Pain-Free
What PPE challenges are professionals facing, and how can they be solved?
- By Cindy Pauley
- Mar 01, 2023
When asked if personal protective equipment (PPE) is painful, most people immediately think of physical pain. But what about other pains, such as training challenges, purchasing problems and compliance issues? Pain doesn’t always have to be physical—nor does it have to be negative.
PPE pain can be caused by frustration in acquiring the right PPE, getting the right fit for employees or finding PPE that isn’t too hot or too binding. Pain felt by management can be from worker PPE non-compliance, or it can be as simple as cost. That same pain, however, can improve worker protection and build trust that the employer has workers’ best interests at heart.
The J. J. Keller Center for Market Insights sought to learn more about PPE challenges, or “pain points,” experienced by safety professionals seeking to protect workers while meeting OSHA requirements. The July 2022 online results from nearly 200 safety contacts revealed some interesting findings.
More than 90 percent of manufacturing company leaders “often or sometimes” have issues with their employees following proper PPE protocols. Reasons given included inadequate training, task hindrances, sizing, heat stress and supply-chain disruptions. To better understand some of these pitfalls, let’s digest the survey results from three frames of reference: PPE stigma, cost and the program.
The PPE Stigma
When asked why there was resistance to wearing PPE, employees didn’t think it was necessary, didn’t know it was required or felt PPE is overprotective or made the job more difficult. Alarmingly, some employees stated they just weren’t interested in wearing it.
PPE stigmas are best combatted with facts. Employees must be given applicable, relatable, real-world examples of injuries that occurred because of a lack of PPE. I’ve often explained to participants in my classes that OSHA regulations have been written in someone’s blood. Following it up with a plea to not let those sacrifices be for nothing has had an amazing impact.
The Cost of PPE
PPE can be costly, without a doubt. Recent supply chain issues have only compounded the problem with a whopping 71 percent of survey respondents experiencing delays in the past year. Supply chain issues resulted in difficulty finding stock, delivery issues and backorders and astronomical prices. However, the costs of not having PPE can be far more costly—from medical bills and lost time to insurance increases and, in some cases, litigation.
Advanced planning, selecting reputable vendors and committing to a sufficient safety budget are the best ways to rein in costs.
Program Pains
Complying with regulatory requirements is another pain point for survey participants. Hazard assessments, procurement, training and enforcement—ouch! Where’s the best place to start building a program that employees will follow?
First, don’t lose sight of the purpose of written programs—to be plans, not pains. No different than a plan to produce “x” number of widgets or earn a million dollars, a PPE program outlines objectives, anticipated challenges and strategies to overcome the challenges. Employees understand how operational procedures lead to their end goal, and they will understand the same about PPE goals. Then, incorporating their input to correct issues will gain buy-in.
Relieving the Pain
PPE pain points are best alleviated by a few steps.
Conducting hazard assessments. Conducting and documenting a hazard assessment, as required in 1910.132(d), is imperative for determining what PPE is required in the workplace and should be supported by all levels of the organization.
Effective hazard assessments involve multiple layers of management considering hazards such as motion or impact, extreme temperatures and chemical and biological exposures. They also require carefully analyzing data from injury and illness records, near-miss information and employee interview feedback to get a clear picture of workplace risk and exposure.
Writing and implementing a PPE program. You could benefit from a written PPE program if:
- Your organization currently has no written PPE program.
- Your injury and illness logs reveal at least one injury or illness due to inadequate or improper use of PPE in the past three years.
- Incorrect use of PPE is observed during an unannounced walk through your work site.
- Employee interviews reveal a lack of knowledge about PPE required in the workplace.
PPE programs should focus on two main objectives: protecting workers from hazards and preventing injury and illness. A little secret is to use your PPE hazard assessment information and watch your PPE program almost write itself.
Ensuring fit and comfort. OSHA requires employers to carefully consider PPE comfort and fit. Not only does improper fit impede necessary protection but committed PPE use is more likely when there’s comfort. Employers must also provide a variety of sizes from which workers can choose. Employers need to shift their mindset from offering unisex sizing, general, small, medium and large sizing and purchasing in bulk that not only puts employees in a bind (literally) but could promote non-compliance.
According to the Bureau of Labor Statistics, in 2021, women comprised 11 percent of construction workers, 7.9 percent of truck drivers and 2 percent of manufacturing employees, and their numbers in these fields continue to increase. Despite this increase, finding PPE that properly fits women remains difficult. Thirty-five percent of study respondents stated this is a challenge.
Women are shaped differently than men from head to toe with vastly different body measurements, so unisex or men’s PPE often doesn’t fit properly. The same holds true for men, who vary in body shape, so PPE needs to be as unique as the workforce. Failure to fit PPE to the worker places them at risk for:
- Gaps in protection, leading to increased exposure to hazards;
- Excess material getting caught in machinery;
- Physical pain, such as headaches from glasses that are too tight;
- Loss of dexterity, resulting in near misses or incidents; or
- Not wearing PPE at all.
Controlling costs. Ideally, cost and durability will go hand-in-hand when it comes to PPE selection. The more durable a product, the less frequently you’ll have to replace it. Spending a bit more upfront to get a higher-quality item will garner savings over time.
Keeping PPE costs in check requires focusing on what matters most:
- Determining if there’s an existing problem with current PPE,
- Discussing with employees the PPE issues they’re experiencing and the best ways to mitigate concerns,
- Reviewing injury and near-miss reports for trends regarding PPE usage, and
- Securing suppliers that offer what’s needed in a timely fashion.
Communicate, communicate, communicate. Discussing hazards and PPE requirements is a two-way street. Employers need to inform employees of when PPE is required, what PPE is necessary, how to properly wear and take care of PPE and most importantly, the limitations of PPE. However, employers also need to listen to workers’ PPE concerns, including the effects of heat stress while wearing PPE, lack of dexterity, discomfort and PPE storage and maintenance struggles.
Training should highlight not just hazard exposures but how PPE is personal to each worker’s safety. Explain what’s at stake if the PPE isn’t worn properly when required, such as not being able to lift their grandchild, ride a motorcycle or hear a favorite opera. Making training impactful and memorable requires identifying the real hazards that employees face.
There may be some pains with staying pain-free, but PPE complacency or misunderstanding will only lead to injury in the long term. The best prescription for PPE pain relief is having a strong written program based on a PPE hazard assessment, offering a wide range of PPE sizes and types, expecting employee accountability, purchasing from reputable vendors and ensuring PPE is both cost-effective and reliable.
This article originally appeared in the March 1, 2023 issue of Occupational Health & Safety.