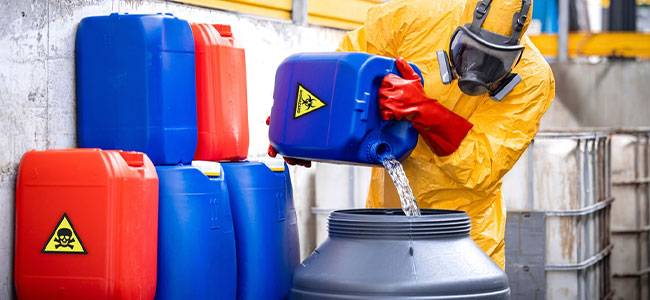
From Compliance to Safety Excellence: Elevating Chemical Handling Practices in the Workplace
Transitioning from compliance to safety excellence is not just a legal obligation but a moral imperative for businesses handling hazardous chemicals.
- By Dave Haase
- Dec 04, 2023
The workplace of today sees chemical handling compliance as a standardized necessity, often dictated by stringent regulations. Yet, a cursory glance at safety records reveals a troubling number of incidents stemming from hazardous material mismanagement. Businesses are recognizing the need for robust safety protocols that go beyond mere regulatory compliance to safeguard their workforce and operations.
Transitioning from compliance to safety excellence is not just a legal obligation but a moral imperative for businesses handling hazardous chemicals. Safety excellence entails creating an environment where the well-being of employees is not just protected by law but embedded in the company ethos. It fosters trust, enhances productivity and ultimately serves as an investment in the longevity of the company.
To ensure the welfare of their workforce and the sustainability of their operations, businesses must pursue a path that transcends basic regulatory adherence. It's about building an organizational culture that prioritizes safety not because the law demands it, but because it's the right thing to do for both their employees and the future of their business. Let’s look at how to do this.
Understanding Chemical Handling Compliance
Basic compliance requirements in chemical handling serve as the minimum standards for safe operation, delineated by governmental bodies to prevent accidents. These regulations encompass proper labeling, storage and disposal of chemicals, along with necessary training for personnel. However, treating these guidelines as the final goal rather than the baseline can lead to a complacent attitude towards chemical safety.
Safety excellence in chemical handling transcends the basic compliance checklist, aiming for a zero-incident workplace through proactive and preventative measures. It involves a company-wide commitment to identifying and mitigating risks before they result in harm. This concept views safety as a continuous improvement process rather than a static goal.
Gaps between compliance and actual safety practices often arise from a check-box mentality, where the focus is on meeting requirements rather than understanding their intent. This approach can overlook real-world scenarios, such as infrequent but high-risk events, leading to a false sense of security. Bridging these gaps requires an ingrained safety culture that values proactive hazard identification and resolution.
Mere compliance with regulations may leave workers vulnerable to unseen risks inherent in chemical handling. The consequences can be dire, ranging from chronic health issues to catastrophic accidents, undermining both employee morale and public confidence in the company. It’s clear that without striving for safety excellence, businesses are only as secure as their last near-miss incident.
Best Practices in Chemical Handling
Proper labeling and storage of chemicals are fundamental to preventing accidents in the workplace. Labels must clearly communicate hazards and handling instructions, while storage solutions need to account for the compatibility and stability of substances. Neglect in these areas can lead to dangerous interactions and exposures, making strict adherence to these practices a key element of chemical safety.
Regular risk assessments and diligent inventory management are strategies to maintain a safe working environment, from the upstream point of chemicals procurement to downstream inventory control. These practices are instrumental in reducing the risk of accidents and ensuring quick and effective responses to any incidents that do occur.
Emergency response planning and the availability of first-aid measures are critical components of a robust chemical safety protocol. Plans must be tailored to the specific risks posed by the chemicals in use, and employees should be trained to respond effectively. Having well-conceived emergency protocols can mean the difference between rapid containment and a full-scale disaster.
Advanced Techniques for Chemical Safety
The latest chemical industry trends show that technology's role in monitoring and managing chemical use is becoming increasingly indispensable. Integrated systems can track chemical inventories, monitor storage conditions and even predict potential risks using real-time data. Adopting these technologies not only enhances safety but also streamlines operations, creating a more efficient and aware workplace.
Predictive analytics stand out as a forward-thinking tool in the realm of chemical safety, capable of identifying trends and foreseeing potential incidents before they occur. Analyzing historical data and real-time inputs enables these analytical tools to alert operators of conditions that might precede an accident, thus allowing preemptive action to be taken.
Advanced personal protective equipment (PPE) and engineering controls represent the forefront of worker protection in chemical handling. Modern PPE is designed to offer greater protection and comfort, increasing the likelihood of consistent use. Similarly, engineering controls have evolved to provide more reliable safeguards against exposure, fundamentally altering the safety landscape in the chemical industry.
The Role of Cutting-Edge Technology
Recent technological advances in chemical handling prioritize safety and efficiency, with automation leading the charge. Smart sensors now actively monitor storage conditions, offering real-time data to preempt any potential hazards. Robotics also play a crucial role, handling dangerous chemicals to minimize human exposure and reduce the likelihood of accidents.
The integration of advanced technology at one specific company is a great example of enhancing safety in chemical handling. This company embarked on a transformative journey to become a Refinery of the Future, focusing on predictive maintenance to preemptively address potential safety hazards.
The predictive maintenance program was designed to monitor the refinery's equipment continuously, using data analytics and AI to predict equipment failures before they could lead to incidents. This approach aimed to minimize the risk of spillage and exposure to hazardous chemicals, enhancing the overall safety of the plant.
The predictive maintenance strategy has not only increased the mean time between failures but also contributed to a safer working environment by reducing the likelihood of unplanned outages and safety incidents. The expectation of a 50 percent reduction in planned maintenance costs further underscores the efficiency gains from this technology adoption.
Trends in chemical handling point towards an increasingly digital and interconnected approach. Companies are investing in predictive analytics to forecast potential safety breaches before they occur. The development of intelligent chemical handling systems promises to enhance safety, reduce waste and streamline operations.
Proactive Safety Measures
Continuous improvement programs for chemical handling have become critical to operational safety and success. Organizations are adopting iterative evaluation processes to identify areas for enhancement in the handling, storage and disposal of chemicals. Employee feedback serves as a vital component of these programs, ensuring that the measures implemented are both practical and effective.
The proactive reporting of near misses is a vital strategy for preventing future incidents. When employees report and investigate these potential hazards without delay, it creates an opportunity to understand and rectify underlying issues. Such vigilance not only prevents accidents but also fosters a workplace culture deeply invested in safety.
Keeping teams informed through regular updates and training is crucial for maintaining a safe chemical handling environment. Employees equipped with the latest safety protocols can identify risks more accurately and react promptly. Ongoing education ensures that the workforce not only understands the current procedures but also the rationale behind them, which reinforces their commitment to safety.
The importance of ongoing training and education in chemical safety cannot be overstated. It ensures that all personnel are not only aware of the latest safety procedures but also understand how to apply them in various scenarios. A well-informed team is the first defense against chemical mishaps, making continuous learning a key aspect of safety culture.
A Holistic Approach to Chemical Safety
Embedding chemical safety into the fabric of a company's culture requires commitment at every level. When safety becomes a shared value rather than just a compliance requirement, it shapes behaviors and decisions across the organization. Such integration leads to a more responsive and responsible workforce, where safety is everyone's priority.
Leadership plays a critical role in fostering a culture of safety excellence within an organization. Their commitment to safety is contagious, setting the standard for others to follow. Leaders who prioritize safety and demonstrate this commitment through their actions inspire their teams to uphold the highest safety standards.
Maintaining high safety standards requires cross-departmental collaboration and a unified approach. When teams across different sectors of a company communicate and work together on safety practices, a more cohesive and effective safety strategy emerges. Such collaboration ensures that safety is not siloed but is a collective responsibility shared by all.
Staying Informed and Ahead
Staying updated with the latest events, standards and legislation is essential for ensuring chemical safety in the workplace. It helps companies adapt to new regulations and maintain compliance. A proactive stance on gathering this information positions organizations to anticipate changes rather than react to them after the fact.
A culture that values continuous learning and adaptation is well-positioned to navigate the complexities of chemical safety. When employees at all levels are encouraged to learn and adapt, the organization becomes agile, responding swiftly to new information and changing safety landscapes. This culture does not just react to changes — it anticipates and plans for them.
The journey towards safety excellence is ongoing and critical to the future of work in the chemical industry. Organizations that dedicate themselves to this journey are not only protecting their employees but are also positioning themselves as leaders in their field. The pursuit of safety excellence today is a clear indicator of a company’s commitment to its workforce and its long-term sustainability.