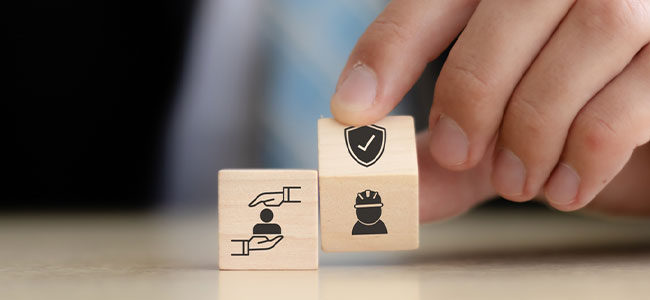
5 Common Reasons Why Safety Measures Get Ignored Over Time
Even organizations with safety measures in place can find standards slipping and procedures being ignored. Here’s why this happens and how to prevent it.
- By Rupert Jones
- Nov 16, 2023
Workplace safety is a paramount concern for any business, and yet even those organizations that have measures in place to protect employees and customers can find standards slipping and procedures being ignored. Here’s a look at why this happens and what to do to prevent the most widespread mistakes.
Employee Burnout
Employee burnout has a significant impact on the disregard of safety procedures in the workplace over time. This can stem from continuous pressure, excessive work hours or reduced enthusiasm due to monotony. Such conditions often lead to fatigue and ultimately decreased attention to safety measures.
Employers need to facilitate environments that manage stress and prevent burnout effectively. In fact, discussing tips to keep service techs motivated in the face of burnout is such a broad topic it is best saved for another day.
Periodic breaks and relaxation techniques are key aspects that should be incorporated into daily routines so that employees remain energized and alert throughout their shifts, successfully maintaining focus on crucial health protocols.
Time Constraints
Compressed timelines and tight deadlines can sometimes encourage employees to prioritize task completion over compliance with safety measures. When employees feel pressured for time, they may take shortcuts or ignore established protocols in an attempt to meet targets faster.
For example, the rush might motivate a construction worker to forgo wearing protective gear or operating machinery beyond safe parameters. This risky behavior compromises their personal safety along with that of anyone around them, thereby increasing workplace hazards immensely.
Employers should enforce strict adherence to safety guidelines irrespective of time constraints and install systems that ensure no corners are cut.
Overconfidence
A common reason safety measures often get sidelined is due to overconfidence among employees. When workers become highly comfortable with their roles or have been in their positions for an extended period, there might be a tendency to underestimate the importance of safety protocols or overestimate personal skill levels. Either way, this can lead to complacency and shortcut routines which fundamentally defy optimum health and safety standards.
Regular check-ins regarding adherence to safe operations should be part of management's routine duties and must also include regular reiterations on the hazards associated with non-compliance. This helps guard against dangerous laxity fostered by false assurance and instills a culture of constant vigilance toward workplace safety.
Lack of Regular Training
Safety measures need constant updating and reinforcement to stay relevant, which can only be achieved with consistent training sessions. Yet the importance of continuous learning is sometimes overlooked by organizations leading to a gradual neglect of safety procedures in favor of familiar practices that might be outdated or unsafe.
Without regular workshops and refresher courses on the latest industry standards for health and safety, employees could unknowingly put themselves at risk while performing their duties.
Consequently, it's crucial for businesses to invest in persistent employee education about current best practices alongside newly introduced protocols so they are well-equipped with the most recent knowledge necessary for maintaining optimal workplace well-being.
Miscommunication
Communicating safety protocols effectively is just as important as implementing them. Often, misunderstandings or lack of clarity in communication can result in employees unintentionally ignoring safety measures.
This situation usually arises when instructions are vague, delivered irregularly or get lost amidst other pieces of information being communicated simultaneously within the organization. In such cases, violations might occur out of ignorance rather than deliberate acts of negligence.
As such, it's vital for enterprises to work on refining their internal communication channels and use clear concise language while discussing safety guidelines to avoid ambiguity at all costs.
Providing written references and conducting regular feedback sessions can further reinforce understanding thus promoting adherence to protective procedures.
The Bottom Line
Knowing the reasons why safety measures are being overlooked puts you in a strong position. The next step is to roll out these preventative strategies, rather than burying your head in the sand.