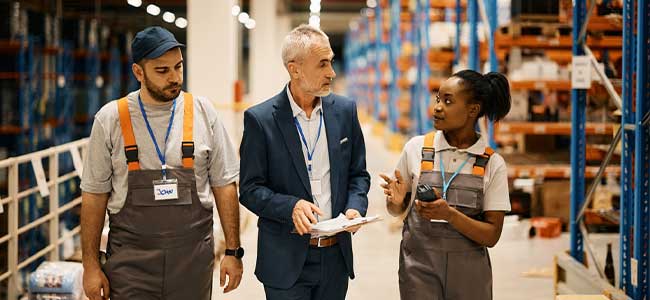
Building a Safety Culture to Enhance Workplace Safety
Every workplace needs a safety plan, but businesses need to determine what safety checks work best for them.
- By Justin Malone
- Jun 22, 2023
We’ve lived through a period of unprecedented demand on the supply chain and material handling industries, and in the chaos of adjusting to new processes things can fall through the cracks. As your facility employees work to keep up with demand amid a labor shortage, the fast pace can highlight issues with your facility’s safety plan. Safety is the single most important component of our facilities. Without a comprehensive safety plan, a facility might be unintentionally putting the people working hard for them at risk of injury.
A strong safety plan is imperative no matter what industry you’re in. It will act as a foundation of a high-performing organization so you can streamline work, maintain operations and most importantly keep your workers safe and your facility compliant. No matter what kind of business you’re in, building a safety culture will begin by finding and implementing the right safety checks that align to your business.
Here are a few great ways to begin engaging your team, driving participation and adopting a better safety culture within your organization:
Schedule Regular Safety Calls with your Management Team. These calls are a coaching opportunity to set up your leaders for success. The goal isn’t just “work safely today,” it’s about actionable advice to improve your facility’s safety collaboratively with input from your teams. We rolled this out in my own business unit to ensure we continued the conversation every Friday to debrief and decide what information needed to be shared with the rest of the team. This prevents relevant information from being siloed and disseminates it with the people who most need to know.
Highlight and Reward “Moments of Courage.” This means creating a culture where everyone feels empowered to call out safety shortfalls when they see them. Making sure your team knows to not look the other way when they see areas for improvement, but to feel confident addressing any moment where something looks unsafe or there would be a safer way to move forward. Working with safety challenges head-on, from all levels, is a great way to find areas of improvement and prevent accidents.
Build in a Stop Work Authority. If anyone on your team sees a job that’s been misquoted, a task that would be best supported by a second person, or any situation that feels unsafe, they should have the full authority to stop work, call a supervisor, and come up with a plan to do the job safely. This is another way to empower your service professionals in the field and let them know their voice and their gut’s guidance matters.
Implement Routine Field Observations. These observations are meant to validate the training and activities happening in the field are up to your facility safety standards. Your management team should schedule surprise visits to the site to check on everything from ensuring job sites are taped off correctly to ensuring procedures are being followed and any injuries are being communicated swiftly and accurately. Ideally, this should cover 80% of your service professional headcount each month.
Engagement and participation are necessary ingredients across any business when it comes to safety. Understanding and creating a structure tailored to your business needs is the first step in getting employees across the board accustomed to and willing to engage in safety checks. In the end, people feel better working when there is a sense of value and a commitment to keeping them safe.
About the Author
Justin Malone is Corporate Field Safety Manager at Miner, the only national service partner for smarter, safer loading docks. As the premier expert in docks, doors and more, Miner’s coast to coast team of best-in-class service professionals help facilities mitigate risk, improve efficiency and achieve consistency.