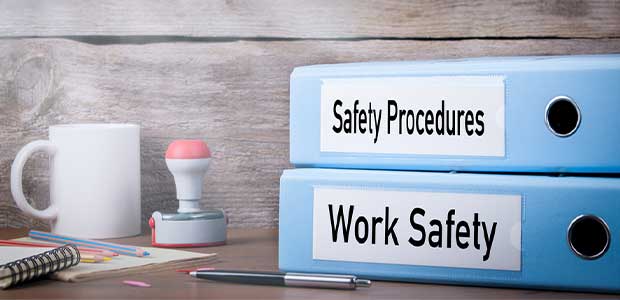
Essential Facilities Management Guidelines: 6 Ways to Improve Workplace Safety and Efficiency
From training to encouraging safe practices, there are many ways employers can increase safety.
- By Geoff Whiting
- Feb 27, 2023
According to the U.S. Bureau of Labor Statistics, there were 5,190 fatal work injuries in 2021, up 8.9 percent from 2020, and 2,607,900 recorded cases of nonfatal injuries and illnesses in the private sector. Workplace safety issues and accidents can occur in any organization, which leads to fatalities, loss of goodwill, lawsuits and hefty fines.
However, workplace safety should be a priority for every type of business. It’s the employer’s responsibility to provide a secure environment for all the team members under OSHA regulations. Implementing a safety program in your facility prevents injuries, improves productivity, reduces costs associated with workplace accidents and boosts employee morale.
In this article, we’ll look at some techniques you can use to improve efficiency and workplace safety.
Provide Ample Training for Your Employees
Comprehensive training is necessary to create a safety culture. Once you hire new employees, you must provide a training program to ensure everyone understands the organization’s safety procedures. Accidents in the workplace commonly happen when employees fail to stick to the set safety protocols.
According to statistics, preventable injury-related deaths increased by 9 percent in 2021; however, you could prevent some of these injuries with proper training. If the management and staff know the consequences of an unsafe workplace, they’ll be more cautious.
For instance, forklifts can cause damage to operators and warehouse property if operated incorrectly. Therefore, you should ensure that all forklift operators are competent and have certified training. Additionally, you should perform regular refresher training and evaluation for all your operators to avoid accidents. Regular scheduling of training programs will help you prevent injuries in your facility.
Reward Your Employees for Safe Practices
Positive reinforcement will encourage workers to keep up with facility safety practices. To improve efficiency and workplace safety, create an incentive program to keep your employees engaged. This strategy will help employees accept change easily and engage in safe behavior to get incentives.
Some of the incentives to offer could include gift cards, extra time off or longer work breaks. Set monthly goals to encourage your employees to practice safe behaviors throughout the period. For instance, if you have been having a lot of accidents or injuries in the loading docks, you can implement measures such as providing protective gear and adding signs and labels in these areas to warn your employees to be more careful.
Constantly rewarding your employees for following safety protocols will encourage them to adhere to the guidelines. In the long run, this improves your efficiency and leads to a decrease in work-related accidents.
Regular Facility Inspections
Regular warehouse inspections, for example, are a critical part of workplace safety. These inspections ensure that the warehouse is running efficiently and help you identify areas of improvement. For instance, you need to constantly check if the staff is following the safety protocols if you just introduced new equipment or handled hazardous materials in the warehouse. These protocols include wearing the right gear, taking the required breaks, and proper machine operation.
Keep in mind that OSHA will penalize employers if they don’t prioritize safety. To avoid these penalties, you should schedule facility inspections to check the conditions. During the assessment, confirm that the staff is wearing the proper PPE, materials are stored correctly and that the warning signs are in place.
Use Labels and Signs on the Floor
Labels and signs provide information about safety procedures and directions to emergency exits. They also warn of potential hazards depending on the products you are dealing with.
These sign boards should be visible to the staff; therefore, you should place them near equipment or in the hallways. In addition, they should be bold enough for all your staff to read them from afar.
You should add signs near labeling machines, floor markings to designate work zones and warnings for potential hazards. You can also caution workers to wear hard hats or high-visibility clothing in particular areas or watch out for forklifts in particular areas on the warehouse floor.
Labels are good communication tools, especially when you have important safety information. You can use a combination of text and images as visual safety reminders for everyone in the warehouse.
Encourage Work Breaks
Employees can get tired fast if they are engaged in repetitive tasks. For instance, businesses in eCommerce fulfillment have to process orders and returns and monitor inventory daily. Therefore, if your team is sitting or standing for long hours when packing products, encourage work breaks to stretch and prevent back and muscle injuries. Staying in one place for too long can lead to muscular stiffness, which makes it difficult to work comfortably and safely.
Additionally, prolonged sitting can increase hypertension and stress levels in your employees. Regular movement breaks will keep your employees relaxed, refreshed and more productive. It keeps the muscles loose, increases blood flow in the body and improves overall energy levels throughout the day.
Therefore, instead of enforcing non-stop work, ask your staff to take small breaks during their shift apart from the standard lunch break. These breaks allow them to reset mentally and refocus on the work. When the warehouse staff is well rested, it reduces the chances of making errors and getting into accidents.
Create an Open Dialogue System
To improve your efficiency and workplace safety, make it easy for employees to report any incidents. This encourages your employees to pay attention to workplace safety. For instance, if there was a recent accident in the warehouse where a team member was injured, you need to encourage employees to voice their concerns or ask questions about their tasks to help prevent another accident.
Your team is more likely to identify areas of concern and potential hazards in your facility. Therefore, if you have an open-door policy, it becomes easier for them to approach you with safety concerns. Conduct regular meetings with the team to get suggestions on how to improve workplace safety. Alternatively, you can also nominate a safety captain to represent all the employees and communicate with the management team.
Summary
In the 1960s, the U.S. had an increase in work-related injuries and illnesses, which resulted in 14,000 workers dying on the job every year. Because of this, the Occupational Safety and Health Act of 1970 was introduced to provide health and safety guidelines in the workplace.
Therefore, as an employer, you are required by the law to adhere to OSHA standards and protect workers’ health and protect them from fatal hazards. Maintaining a safe facility minimizes the risk of injury and leads to higher levels of employee satisfaction.
Geoff Whiting is the Senior Writer for Red Stag Fulfillment, an eCommerce 3PL focused on supporting heavy, bulky, and high-value products. He has more than a decade of experience covering eCommerce, technology, and business development. In his free time, Geoff enjoys exploring new cuisines and music and trying not to get too lost listening to podcasts while walking in nature.