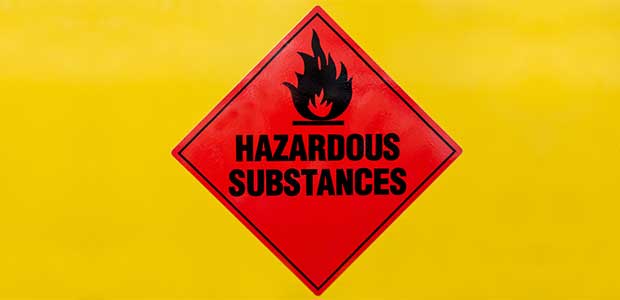
How to Properly Store and Label Hazardous Substances
Correct storage and labeling can help make your worksite safer.
- By Kevin Rowe
- Jan 18, 2023
For many businesses, daily activities necessitate the use of hazardous substances. To use and store them safely, it is critical to recognize the risks they pose and to meet the highest levels of workplace safety. Occupational safety protocols must therefore account for all hazardous substance handling, storage and comprehensive risk management.
In the UK, such occupational safety precautions are governed by the Control of Substances Hazardous to Health (COSHH) Act. Following an annual review of workplace safety, COSHH emphasizes the need of meeting and routinely refreshing safety procedures in all businesses.
In addition to meeting regulatory safety standards, we will explain below how to correctly store and label hazardous substances in the workplace, as well as outline the safety procedures and regulations you should implement to keep all those on site safe.
The Types of Hazardous Substances
COSHH defines hazardous substances as "chemicals, products, fumes, dusts, mists and vapors, and pathogens" that can pose a danger to one's health. Each hazardous substance category provides unique dangers, so it is vital that businesses recognize that hazards vary and that safety measures for one hazardous material may not be adequate for another.
Before storing hazardous substances on site, a business must prepare for the risks associated. The persons responsible for health and safety at the business must undertake comprehensive risk assessments for all aspects of the hazardous substance's usage, including storage and handling.
Carrying out due diligence of a substance’s risk before it arrives at the workplace, and ensuring this knowledge is shared amongst all on the premises, will significantly improve on-site safety and reduce the risk of injury. Doing so early will provide the business with more time to examine all hazards and communicate this information with individuals on site.
Best Practices for Storing Hazardous Substances
Good lighting throughout. One of the easiest methods to ensure the safe storage of hazardous substances is to provide excellent lighting wherever the substance is stored and used. Accidents at work can occur when there is insufficient lighting because it limits an individual's ability to detect additional hazards; it could conceal a trip hazard or moving machinery, both of which can easily cause an accident.
Even if sunlight provides adequate light during working hours, a workplace should not rely on it. As the weather changes, so do the light levels, making it more difficult to identify other hazards. As we will see further down, some substances must be protected from direct sunlight.
Well-ventilated spaces. Any area storing the substance must have adequate oxygen levels and ventilation. Many chemicals gradually leak gases into the environment that, if allowed to collect, can be dangerous to an individual in its vicinity. Maintaining good ventilation decreases the possibility of a gas buildup and distributes oxygen to maintain safe levels.
Room to maneuver. To properly store hazardous compounds, plenty of storage space is required - not only for the arrangement of the containers holding the substances, but also for transportation and use. Hazardous chemicals in crowded workplaces significantly increase the chance of an accident.
The manufacturer's safety information will include storage instructions for the hazardous substance or material. It is critical that these standards are recognized prior to the material coming on site so that adequate storage is planned ahead of time.
Surfaces that are secure. Along with enough storage space, the surface on which the hazardous chemical is to be stored is an important consideration; it must be resistant to the chemical, which is crucial in the event of a spillage. Any concerns concerning the surface's integrity must be examined before it is chosen as an effective storage option.
The storage surface must be simple to clean, which means it must be conveniently accessible to individuals who need to clean the surface and contain the material in the event of a leak.
COSHH-compliant storage. The safety criteria of the substance determine the storage option type. Following the manufacturer’s storage guidelines gives a business the peace of mind that they are meeting the expected safety standards.
COSHH standards set the compliance level needed for a storage solution. As such, by selecting a COSHH cabinet or cupboard, a business can be certain that the substance will be kept in storage that satisfies the highest safety requirements.
Environmentally conscious. When storing several types of hazardous compounds in the same place, a business must evaluate the associated hazards. Certain chemical compounds can mix with others and generate a dangerous chemical reaction, so separate safe storage is essential when outlined by the safety information provided alongside the substance. This knowledge must be applied to the possibility of chemical interactions in the ventilation system.
Cleaning supplies that are easily accessible. Even with stringent safety precautions, accidents at work can happen. A risk evaluation of the processes for spilled chemicals is a critical component of the storing process.
To prevent the damage and hazard posed by a spillage, the storage must be easily accessible to workers intending to clean it. In tandem, cleaning equipment must be readily available across the premises and be suitable for spill control as well as cleaning. This often takes the form of high-quality absorbents and disposal bags, warning tape, and leak-sealing putty.
Labeling
Chemical categorization and labelling under the Globally Harmonized System of Classification and Labeling of Chemicals (GHS) offer a worldwide recognized system. One of the leading causes of workplace accidents with hazardous substances is an inability to perceive or detect their dangers. This is often due to a lack of hazardous material reporting protocols, no health and safety culture, or insufficient health and safety training.
To keep staff safe, hazardous substances must be properly labelled.
The first step in ensuring the safe management of hazardous substances in a workplace is to keep a current inventory of all your compounds. This inventory should include the product's safety data sheets (SDSs) from the manufacturer or supplier. The SDS will provide hazardous symbols and warnings to help you understand the dangers connected with the substance. These symbols, called pictograms, are standardized by the GHS and are identifiable by a symbol on a white backdrop within a red border.
The symbol represents a particular risk connected with the substance. It is vital to remember that the product label or SDS may mention numerous hazards and, as a result, contain a large number of pictograms. The business must ensure that all those on site understand these symbols and that they are easily found on the substance’s storage.
Preparing for all dangers related to hazardous material storage will result in the business fulfilling the highest workplace safety requirements. In turn, this level of safeguarding will help the workers recognize that precautions are being made to protect them.