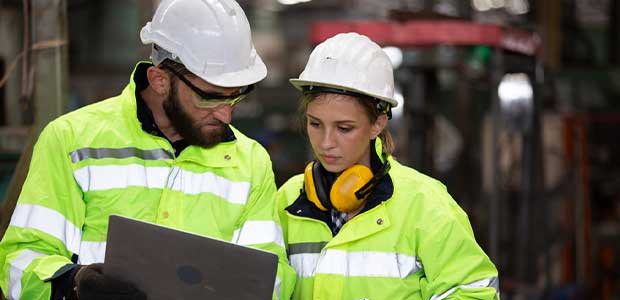
5 Safety Blind Spots in the Workplace
These blind spots can pose risk to workers.
- By Alex Saurman
- Jun 08, 2022
Many people are familiar with the concept of blind spots. When driving, it’s not always possible to see all around the vehicle using just the mirrors. Not checking these blind spots by turning and looking can lead to accidents.
Blind spots like these exist at work, too. When employers or workers don’t think about the entire picture, like rules or guidelines, it can lead to blind spots. Workers can be injured when these blind spots are ignored. Safety blind spots are something we explore in the most recent episode of our podcast.
There are many kinds of safety blind spots. Mastery Training Services published a white paper highlighting some of these.
- Safety Plans. Employers should not assume a workplace is safe, even if injury rates are low. Safety plans and frequently updating these plans can help employers and workers prepare for all situations, even common hazards.
- Slips, trips and falls. Walking and working surfaces can present a hazard if they are slick, wet or blocked. In 2019, slip, trip and fall accidents injured about 244,000 people, according to the Bureau of Labor Statistics. An article from Mastery TCN notes that simple things like cubicle walls blocking views or stacked boxes can lead to falls.
- First Aid. Having the right equipment and knowledge to treat first aid-needed incidents is important. If a workplace is far from a medical treatment center, are workers trained in treating minor injuries? Do first aid kits contain everything needed to treat these injuries? Not being able to properly treat small injuries can lead to more harm.
- Sanitation. Clean surfaces are essential to keeping workers safe and healthy. Uncleaned or improperly cleaned surfaces can lead to diseases spreading in the workplace.
- Ladders and railings. When using a ladder, there are specific safety rules workers must follow. Workers must have one hand on the ladder at a time, and must have three points of contact. Workers who need to use tools at heights should not carry them up the ladder as they climb. Instead, they should use a pulley system. Workers who are not aware of these rules and do not think they can get hurt this way are at risk for injury.
For additional examples of blind spots and to learn how to avoid them, listen to our podcast.
About the Author
Alex Saurman is a former Content Editor for Occupational Health & Safety,who has since joined OH&S’s client services team. She continues to work closely with OH&S’s editorial team and contributes to the magazine.