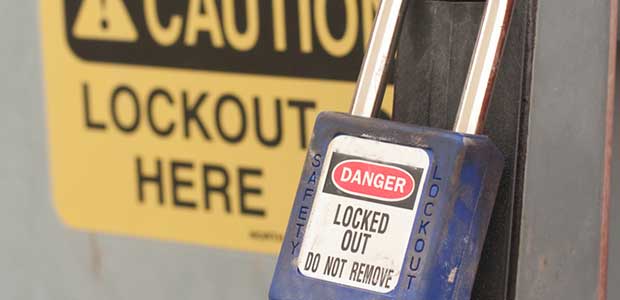
How to Stay OSHA-Compliant with Lockout/Tagout
A well-structured training program helps companies avoid the human and financial costs associated with an OSHA violation.
- By Shawn Smith
- Mar 01, 2022
The construction industry remains one of the most dangerous industries in the U.S. Just last year, fatalities in the private construction industry increased five percent to the largest number since 2007.
In order to limit incidents, workers need clear and actionable safety plans. This means a continuous commitment must be given to performing tasks like regular training sessions, audits and maintenance checks.
These types of checks are especially crucial for lockout/tagout (LOTO) procedures, since they require clear documentation and cooperation from your whole crew. Here are three strategies to stay OSHA-compliant on your construction site with your LOTO practices.
Diagnose Why Lockout/Tagout Violations Are Happening
LOTO violations often occur for three reasons. The first is poor documentation of safety practices for machines and equipment. Authorized employees should have formalized, written procedures for every machine and piece of equipment on their site. “Poor documentation” frequently extends to organizations that fail to document each piece of equipment or fail to document any procedures at all.
The second is inadequate training. Training must be given to any employee who works around dangerous equipment. It isn’t enough to merely provide training to employees directly responsible for operating or applying locks and tags to equipment. Your entire crew must be educated.
The third is prioritizing the speed of a project over its safety. When a construction site operates in this way, mistakes get made. These errors can range from using the wrong LOTO devices to failing to identify each source of hazardous energy. In short, when speed becomes the primary motivator on your site (as opposed to safety), it Is not a question of if a violation will happen, but when.
Another reason violations occur is because LOTO procedures vary. Bigger machines and equipment that impact an entire site’s operation often require a group LOTO effort, whereas smaller machines and equipment usually require just one.
These varying practices also affect the amount of time needed to conduct LOTO i.e. the larger the machine the larger the time commitment. If your site emphasizes quickness over quality, this could lead to violations. LOTO procedures require precision and understanding from a whole crew, even if the whole team isn’t directly involved with that particular LOTO.
Reinforce the Gravity of Lockout/Tagout Violations
A violation can pose serious threats to your team. The danger from these machines and pieces of equipment comes from their energy sources, such as electricity, steam or chemicals, which can be released regardless of whether the machine or equipment is in use.
Take, for instance, a hydraulic press, which can exert multiple tons of force in mere seconds. If a hydraulic press hasn’t been de-energized, it could easily crush someone.
Beyond the physical harm of an incident like this, the costs of a violation may derail a project. OSHA penalties can exceed $13,000 per violation, and this figure often compounds for every day the violation goes unfixed.
If a worker is injured, you may be on the hook for costs related to:
- Legal and compliance proceedings
- Replacing damaged equipment
- Workers’ compensation
- Lost productivity
Acknowledging the seriousness and potential harm of LOTO violations doesn’t just exhibit caution, it can also help curb their frequency.
Foster a Culture of Safety
One major way you can establish a culture of safety from the top down is by implementing LOTO training on your construction site. Many workers possess some degree of experience or training on their own. But by standardizing and benchmarking exactly what procedures must be followed on your site, you can help reduce the potential for OSHA violations and harm to your crew.
Employees should also understand and practice the most basic procedures for LOTO practices, which are as follows.
Authorized Employees are required to:
- Identify all potential energy sources.
- Review any energy control procedures or specific instructions.
- Ask affected employees to leave the work area.
- Shut down the equipment.
- Isolate the energy source with an appropriate device.
- Use proper locks and tags for isolation.
- Ensure the equipment is de-energized.
- Check for any residual energy before trying out the equipment.
- Begin work once zero energy is confirmed.
Beyond providing the protocols for LOTO, you should also establish a system where workers can ask questions and receive clear answers on safety procedures. It isn’t enough to list the requirements once. You need to consistently repeat the processes and encourage workers to voice inquiries. There is no such thing as a stupid question when lives could be at stake.
On-Site Safety Measures Help Ensure the Health and Success of Your Team
It can be easy to relegate comprehensive safety measures to the back burner. Projects have deadlines, and hitting them is a primary metric for evaluating the success of your company.
Many companies may also not know their workers’ level of safety knowledge. This impacts what training a company would invest in because if they don’t see a need, they won’t fill that need.
It’s important to remember that nobody wants to be blatantly unsafe. This is why it’s critical to align your company’s culture with tangible actions. It’s not enough to want workers to be safe. You must support workers’ safety by implementing clear, repeatable processes that emphasize their health and protection.
A well-structured training program helps companies avoid the human and financial costs associated with an OSHA violation and positions them for continued success.
This article originally appeared in the March 1, 2022 issue of Occupational Health & Safety.