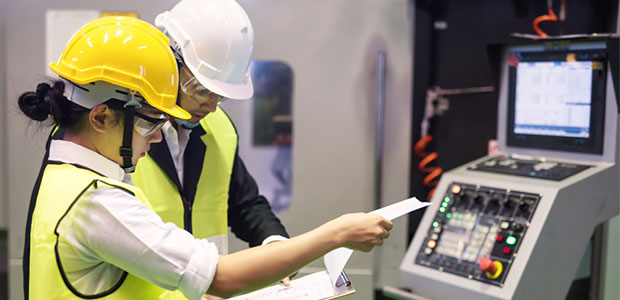
Safety Incident Reporting: Empowering Employees to Act
Successful cultures of safety are not ashamed of near misses.
- By Jonathan Jacobi
- Nov 21, 2019
In a strong corporate safety culture, every employee is involved in safety activities and motivated to identify and reinforce habits and practices that protect staff, products and the facility.
Successful cultures of safety are not ashamed of near misses.
Instead, they consider incidents and negative observations as opportunities to improve work systems and communicate observations for the greater good of the organization.
Ultimately, strong reporting is the hallmark of a robust culture, but not all organizations report successfully.
Four Incident Reporting Obstacles
What prevents workers from reporting safety incidents? These are the most common contributing factors:
1. Fear of disciplinary action or retribution or fear of some other type of negative response for those who report; there is a fear of blame.
2. Apprehension about taking on the role of a do-gooder, or worse, a rat.
3. Lack of action—workers become skeptical when reporting does not produce action or remediation of an ongoing problem.
4. Overly laborious or complicated reporting documentation (red-tape) can dissuade an employee from taking the time out from regular job responsibilities.
To overcome these obstacles, we need to emphasize the positives by making the process fair by recognizing safe work as much as or more than pointing out items needing improvement.
It can be easy to overlook positive safety functions that are working effortlessly every day.
When a worker does step up to report a workplace safety issue, they should be recognized for their diligence and safety activism.
The Employee is Not the Root Cause of the Safety Incident
We also need to create an environment where workers feel safe to step forward. This means addressing work systems rather than simply ‘fixing’ employee behaviors and actions.
From an operational or logistics perspective, workers are often at risk due to workload, staffing inefficiencies, productivity pressures, incomplete training, inadequate or outdated equipment or technology, or other issues outside their control.
The key to a safe workplace is to promptly and proactively address and correct the systemic causes of the risk, not point fingers at specific employees.
When the safety reporting risk is mitigated, workers feel more confident any future reporting will also be addressed and remediated.
Identifying Employee Safety Leaders
Develop your workforce into a team of safety management guards who maintain these qualities:
- Mindset of a protector
- Problem solvers
- Open-minded and willing to accept feedback
- Contemplate “what if” scenarios
- Looking at the future potential instead of only the present situation
Managers and supervisors also have an essential role to play. We need to understand why and how incidents happen and be open to the feedback we receive.
Issues should be addressed as they arise, not added to a safety hazard laundry list to be handled in the future.
Design Operations and Processes for Change
A reliable operations system can spot an action that’s going wrong, rather than one that’s already gone wrong. Being able to spot developing problems is not a bad thing.
Safety observations and near misses provide opportunities to eradicate weakness from the safety system.
Strengthened systems don’t fail easily and won’t require impossible standards that people in real life situations can’t possibly meet.
It is incumbent on management—at all levels—to create an operational structure that encourages workers to report their experiences and be their co-worker’s keeper, without fear of retribution.