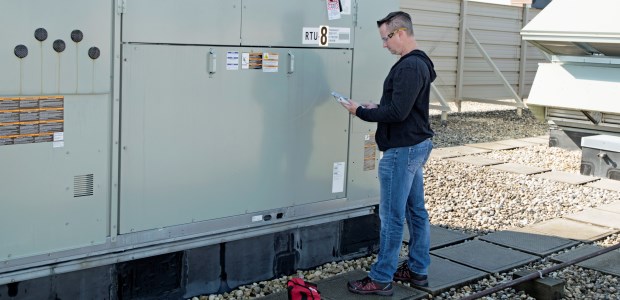
Lockout/Tagout Challenges & Best Practices for Health Care Facilities
Clear, systemized safety procedures and good practices will keep your patients and employees safe with fewer accidents.
- By Bill Belongea
- Jul 15, 2019
Year after year, lockout/tagout (LOTO) ranks among the Occupational Safety and Health Administration's top 10 most-cited violations, with nearly 3,000 LOTO citations last year, according to the National Safety Council.1 Based on the volume of LOTO citations, it's evident that companies face challenges in implementing effective lockout strategies.
OSHA refers to lockout/tagout as the practice of controlling hazardous energy to prevent the unexpected start-up, energization, or release of stored energy during service or maintenance activities. Hazardous energy encompasses all energy sources, including electrical, mechanical, hydraulic, pneumatic, chemical, thermal, or other sources, such as gravity, in machines and equipment that can be hazardous to workers. LOTO is not just best practices to prevent worker injury—it’s the law.
The OSHA standard for The Control of Hazardous Energy (lockout/tagout, 29 CFR 1910.147) "outlines specific action and procedures for addressing and controlling hazardous energy during servicing and maintenance of machines and equipment." The OSHA standard applies to a wide variety of industries, ranging from manufacturing to oil and gas to health care.
Common reasons for LOTO noncompliance include: 1) the thought that recognition and isolation of hazardous energy is a difficult compliance requirement, 2) the incorrect belief that LOTO procedures decrease productivity and 3) in industries such as health care, isolation of hazardous energy and visual procedures are often overlooked due to a general lack of awareness.
Lockout/Tagout in Health Care Settings
Lockout and tagout are often considered requirements for industrial environments. But with today's accident trends showing many serious injuries and fatalities occur in non-industrial settings, the number of health care institutions proactively taking measures to safeguard authorized personnel responsible for service and maintenance is on the rise.
The OSHA standard applies to a large number of work environments and certainly, the equipment-intensive environments of hospitals, clinics, and educational centers are not exceptions. Formal lockout practices are of paramount importance for health care campuses where a wide range of maintenance activities, equipment types, and potential environmental and mechanical hazards abound. Heating, cooling, and ventilation equipment, complex lighting systems, data centers, and medical lab equipment are a few common areas where LOTO procedures are needed in health care facilities.
Every health care facility is required to comply with OSHA. Failure to meet current standards could result in OSHA violations, or worse, catastrophic incidents, injuries, and OSHA penalties. This can jeopardize patient care if critical machinery and equipment is down because of incident investigation.
But lack of overall awareness of lockout obligations under OSHA regulations, as well as an ever-changing regulatory environment under The Joint Commission, pose a unique challenge for health care facilities. Traditionally, fewer people participate in lockout procedures in an institutional setting, such as hospitals, meaning there may be fewer qualified experts, less resource training, less frequent auditing, and more limited procedures for the staff to follow.
Although every facility has its own unique set of LOTO issues, it's worth examining how one leading hospital strengthened its safety program by raising awareness of LOTO internally and making it easier for employees to perform safety procedures.
How UC San Diego Health Implemented LOTO Procedures to Improve Worker Safety
UC San Diego Health, the only academic hospital in San Diego, is one of the premier health care providers in the United States and is nationally ranked in six adult medical and surgical specialties by U.S. News & World Report. With more than 1,500 doctors and scientists who are published experts in the field, UC San Diego Health provides unparalleled patient care.
As a leading health advocate, the hospital chose to proactively evaluate the state of its LOTO programs at its Hillcrest and La Jolla facilities to ensure the safety of its workers and prevent incidents that could jeopardize patient care. UC San Diego Health selected our company as its workplace safety partner. UC San Diego Health's primary goal was to prevent lockout-related incidents due to the unexpected release of hazardous energy while workers maintain and service machinery and equipment. As a secondary goal, the hospital was interested in assessing the workplace to provide a more efficient work environment that would not decrease the productivity of its workers.
In addition to the UC San Diego Health’s primary goals, lockout equipment deployment strategies were assessed and created to provide added efficiency to the tasks performed by authorized personnel simply by improving access to the lockout equipment.
Implementing Safety Procedures and Efficiencies at UC San Diego Health:
- Raising safety awareness. All workers authorized to service or repair equipment must now protect themselves and their co-workers by applying lockout before they begin to work on machinery, based on regulations outlined in the 1910.147 OSHA standard.2 This means that workers must first understand the applicable safety requirements and guidelines and then act to protect themselves and their colleagues. To educate workers, Gena Hedger, one of our company's most experienced lockout sales managers and solutions providers, conducted lockout training at both UC San Diego Health facilities with all information tailored to the hospital environment. This instructor-led training covered Cal/OSHA's lockout standard, best practices for controlling hazardous energy, common mistakes that lead to accidents, as well as the importance of personal responsibility to ensure the safety of the workers and their colleagues.
- The safety process. A common, universal cause of lockout-related incidents occurs when workers skip safety steps with the thought that these procedures add complexity and extra time to their work. "Rapid Access to Lockout Equipment" practices, which are based on lean management principles, were applied to help UC San Diego Health improve worker access to lockout equipment. One significant element of this was equipping authorized workers with customized lockout safety kits. Rather than having to leave a machine's side and retrieve the necessary safety equipment from distant storage locations, workers have all of the necessary equipment on hand. This maximizes access to lockout equipment, which in turn minimizes wasted time. After raising awareness of the importance of workplace safety, implementing best-practice-based recommendations and improving access to lockout equipment, UC San Diego Health has taken measures to improve its safety culture while obtaining tangible results. Specific outcomes included increased efficiency, as UCSD Health workers now perform lockout 50 percent faster; a uniform and consistent methodology with newly implemented lockout procedures; and increased participation in the Lockout Program among not only Authorized personnel, but all employees.
Four Lockout Components and Best Practices for Health Care Facilities
UC San Diego Health's case study illustrates how one facility made the decision to improve an already effective safety program. Regardless of the stage of your LOTO program, there are four components, or best practices, you should consider:
1. Develop a Hazardous Energy Control Program. A baseline approach to safe lockout practice is the implementation of a Hazardous Energy Control Program specific to the operations of your health care facility. This program should be a user-friendly, site-specific document customized to your operation that outlines the roles and responsibilities of all employees within your Lockout Management System.
Your program should detail the following for all applicable employees:
- The scope and application of your lockout policy
- Responsibilities of all participating personnel, including administration, Authorized and Affected employees, and any other third-party employees involved in servicing or maintaining equipment
- Documented energy-control procedures
- Method of accessing all necessary energy-control equipment and hardware
- Employee training/retraining program for Authorized and Affected personnel
- Contractor participation in energy-control practices
- Annual inspections of the use of the procedures to verify, maintain, or improve their effectiveness
2. Create machine-specific, visually instructive LOTO procedures. In addition to an overview guide of your lockout/tagout program standards, it is important to provide equipment-specific visual documents outlining the procedural steps to shut down equipment safely to a zero-energy state. For this type of instruction, a visual approach is best, one where you clearly show the equipment to be worked on with step-by-step instructions as to what must be secured and done to prepare for shutdown and isolation of hazardous energy.
3. Training and retraining. In addition to being equipped with a lockout program and equipment-specific procedures, your employees must be trained so they understand the purpose and function of your facility's lockout program and the equipment to which they are exposed. The amount and type of training that each employee receives should be based on the relationship that employee's job has to the equipment being locked out and the degree of knowledge relevant to hazardous energy that employee needs to control.
4. Auditing and inspecting. To identify methods of improvement in process and changes or updates on equipment, health care facilities must conduct in-depth audits and inspections to determine areas where hazardous energy is present and LOTO procedures need to be implemented. This includes on-site examinations and analyses of the facilities and their applications for controlling hazardous energy sources during maintenance and repair operations.
The Business Case for Implementing LOTO Procedures in Health Care Facilities
Many organizations view safety compliance as a cost center that works against profitability, but that's a misguided belief. Return on Investment can be a powerful illustrator of the cause-and-effect nature of accident prevention.
Health care facilities can determine ROI by projecting what can be saved in the short term related to lost productivity due to disruption of operations from a history of significant accidents, increased insurance expenses, public relations impacts, and the positive benefit of increased efficiencies due to improved safe work processes. Facilities can calculate cost savings by using the ROI formula: Net Profit ÷ Cost of Investment = Return on Investment (ROI).
Often, businesses find significant savings when going through this exercise, but other financial and operational benefits of implementing LOTO procedures include:
- Operational efficiency. Identifying weak points and hazards throughout operations can affect the reliability of work being performed. Improvements increase productivity, leading to short-term gains that can turn into long-term, sustainable profitability. For example, making safety equipment readily available where lockout needs to be applied can increase productivity.
- Forecasting preventable losses. Proactive efforts eliminate or minimize incidents, resulting in estimated cost savings that exceed the price of the reactive actions. Example: investing in air filtration technology to replace or reduce the reliance on respiratory protection.
- Compliance requirements. By designing processes that consistently provide safer, more productive outcomes, companies find that going beyond compliance to running a well-organized health and safety management system is a justified investment.
- Job satisfaction. Workers don't respond positively to unsafe and hazardous workplaces and may not work for long under those conditions in exchange for a paycheck. Management already has a demanding list of responsibilities, and having to respond to preventable on-the-job incidents only makes their job harder.
- Public reputation. Public image influences the workforce, customers, and a business's role as a good corporate citizen. News travels fast, which can result in a lasting impact that can affect the ability to compete effectively in the marketplace.
Well-managed lockout programs will go a long way to keep you compliant with OSHA—but that is just the tip of the iceberg. Clear, systemized safety procedures and good practices will keep your patients and employees safe with fewer accidents. Moreover, they will serve to boost productivity by minimizing equipment downtime and streamlining maintenance procedures, which in turn will increase the overall efficiency of your facility's operations. Prioritize lockout/tagout in your hospital, clinic, or medical facility, and you will be taking a significant stride toward building a safer, healthier, more productive workplace.
References
1. https://www.nsc.org/in-the-newsroom/oshas-top-10-violations-for-2018-revealed-at-national-safety-council-congress-and-expo
2. https://www.osha.gov/laws-regs/regulations/standardnumber/1910/1910.147
3. https://www.osha.gov/pls/oshaweb/owadisp.show_document?p_id=9804&p_table=STANDARDS
This article originally appeared in the July/August 2019 issue of Occupational Health & Safety.