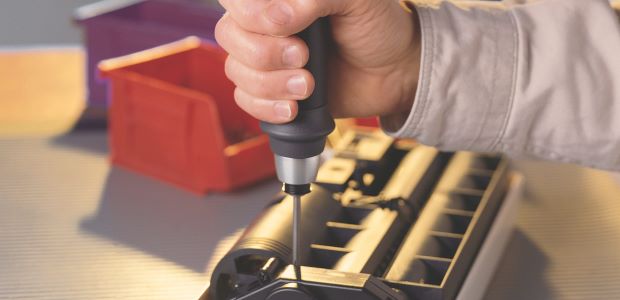
Ergonomic Assembly Tools Can Ease the Pain of Manufacturing
Tool manufacturers are improving all aspects of their tools, including the shape, size, weight, balance, torque, vibration, speed, and noise.
Manufacturing industries, with diverse fastening applications from the motor vehicle industry to appliances and aerospace to white goods, rely on assembly tools such as air-powered screwdrivers, nut runners, and drills. These tools are a driving force in bringing products to market, but they can also be the cause of undue pain for their operators if ergonomics are not applied to the tool and how the tool is used.
Assembly tools are used continuously throughout the day, day in and day out. Without proper ergonomics, the repetitive motion when using these tools can lead to fatigue, hand and arm stress, and even injury. To relieve potential pain and stress for the workforce, assembly tool manufacturers are keenly focused on improving the ergonomic qualities of their products.
Regulatory Compliance
Tool ergonomics can directly impact worker productivity by decreasing fatigue and increasing worker comfort. It also can result in decreased costs from fewer workers' compensation claims and medical costs.
The Department of Labor's Occupational Safety and Health Administration issues workplace standards requiring employers to take particular actions to reduce musculoskeletal disorders (MSDs) and other contributing workplace hazards, also known as ergonomic hazards. Ergonomics programs from a number of state and federal agencies have been found to be very effective for both companies and employees. For example, the United States Government Accountability Office compiled findings from employers that have taken the initiative to address MSDs through the implementation of their own ergonomics programs using OSHA standard guidelines.
Certifications allow manufacturers to impartially compare the performance of competing products. For example, the motor vehicle industry wanted to assess the performance of continuous drive tools across varying joint conditions. The International Organization for Standardization created the ISO 5393 standard to specify a laboratory performance test method for installing threaded fasteners, which provides instructions on what to test for and how to evaluate and present the test data. With this certification, companies can have assurance in the performance of a tool over time and feel confident incorporating the tool into their manufacturing processes.
Operator comfort has become so important that ergonomics is now at the forefront in assembly tool design. Tool manufacturers are improving all aspects of their tools, including the shape, size, weight, balance, torque, vibration, speed, and noise.
When purchasing tools, it's important that the procurement of assembly tools follow established standards for ergonomic functions. Design engineers at Ingersoll Rand have made extensive advances with the ergonomic properties of the Q2 Series tools. The Q2 Screwdriver handle eliminates fatigue with an innovative egg shape that allows the tool to sit comfortably in the operator's palm. These tools have many ergonomic features, such as a low trigger-pressure design, hand and finger comfort, soft-grip texture, reduced torque reaction and vibration, and low power-to-weight ratio.
As speed affects a tool's vibration levels, the Q2 Screwdriver supports OSHA vibration guidelines that are measured by acceleration. The screwdrivers average less than 2.5 meters per second squared and sound absorption equal to 75 decibels (dBA), which is lower than OSHA’s maximum allowance of 85 dBA over an eight-hour work day.1 These ergonomic features help tool operators work comfortably through many hours of productivity.
Tool accessories are also important to optimize assembly operations and provide maximum productivity. From torque reaction arms and torque tubes to spindle accessories and spring balancers, these accessories improve ergonomics and efficiency.
The Economics of Ergonomics
Ergonomic assembly tools are designed to reduce MSDs and injuries that can occur over time through repeated exposure to various risk factors such as contact stress, force, repetition, posture, vibration, and environmental exposure to noise, lighting, and temperature.
The Bureau of Labor Statistics, a division of the U.S. Department of Labor, measures and evaluates working conditions. BLS reported that for all 2015 cases involving days away from work, about 356,000, or 31 percent, were the result of repetitive motion or overexertion. The study also reported that over the course of one year, MSDs required a median of 12 days to recuperate before the individuals returned to work.2
According to OSHA, U.S. employers spend almost $1 billion per week on direct and indirect workers' compensation costs associated with injuries and illnesses experienced by their employees.3 The agency estimates as much as one-third of these costs are due to MSDs.4 Many of these illnesses and injuries are related to repetitive stress or sustained exertion on the body.
There will always be risk factors associated with manufacturing work. However, the key is keeping risks at acceptable levels and to not exceed those levels. To that end, tool ergonomics is really about controlling risk factors through innovative design techniques and materials.
It is important to match the correct tool with the application and is equally important to have proper ergonomic positioning and appropriate tool accessories to avoid injuries such as muscle strain, tendonitis, and carpal tunnel.
Excessive tool vibration can decrease blood flow, damage nerves, and cause muscle fatigue. There are many factors that influence tool ergonomic performance. Matching the tool with the variances in hand size requires different tool sizing. To compensate for this difference, many tool companies provide various sizing components or built-in adjustability.
Operators should use the right tool configuration for the right type of work. For example, an operator applies different speeds through different layers of materials. The Q2 Screwdriver has a torque range that can be manually adjusted with a pin on the tool to set different torque levels based on the speed needed for different tasks.
Tool Ergonomics Eases the Pain
Assembly tools are in constant use every day. Companies need tools that their operators can use all day without ending their shift with muscle fatigue and pain. They need tools with reduced trigger force per finger, improved grip comfort, and lower overall muscle effort. They require tools that are well-fitted to the hand, have excellent torque reaction, and are well-balanced.
With proper ergonomic features, using these tools will ease fatigue from repetitive motion that causes hand and arm stress. Tool ergonomics can improve worker productivity while minimizing medical costs and workers' compensation claims.
It's important to have a system for assessing the ergonomics of a product's design. A well-defined ergonomics program helps companies better understand a product’s features, the benefits derived from those features, as well as how the benefits bring value to their specific applications.
Assembly Tool Ergonomic Features to Look For
- Low torque reaction
- Use of neutral hand and wrist postures
- Low peak pressures across the grip with a generally even pressure distribution
- Soft-touch grip for comfort and reduced grip effort
- Low muscle effort levels during use
- Thermal comfort with operating temperatures between 68-77 degrees Fahrenheit
- Low vibration across spectrum (6hz-5000hz)
- Light weight
- Low trigger pressure (less than 22 psi)
- Good trigger control/response ratio (trigger throw vs. tool speed)
- Balance closest to second knuckle of the middle finger
- Options provided for air intake (top, bottom, etc.)
- Flexible tool suspension
- Accommodation for lightweight air hoses
- Low effort for reverse switch activation
- Ease of carrying
References
1. https://www.osha.gov/pls/oshaweb/owadisp.show_document?p_id=9735&p_table=standards
2. https://www.bls.gov/news.release/pdf/osh2.pdf
3. https://www.osha.gov/dcsp/products/topics/businesscase/costs.html
4. https://www.osha.gov/SLTC/ergonomics/
This article originally appeared in the July/August 2019 issue of Occupational Health & Safety.