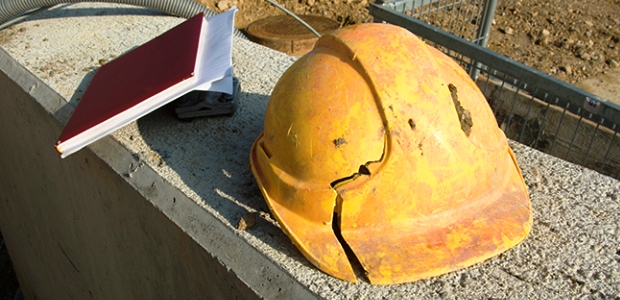
The Number 1 Reason to Demand Your Tool Tether Be Dynamic Drop Proven
A device may pass a static test with flying colors, but when put into a real-life situation it may still fail and break, and that's bad for anyone standing underneath.
- By Nicholas Voss
- Dec 01, 2018
Why is dynamic drop testing important when it comes to tool safety? When the ISEA 121 committee on Dropped Object Prevention (DOP) began working on the new standard, they made a keystone decision to require dynamic drop testing to prove all DOP solutions instead of the traditional static testing. But why is this important? How does this make us safer, and what is dynamic drop testing anyway? Let's see if we can shine a light on some of these questions.
Up until then, Dropped Object Prevention companies have tested their products the same way rock climbing companies test their rope and carabiners: They used a math equation and a static tensile test. To follow this method, you take the mass you're going to drop, use physics to determine the velocity it will be traveling at the full extension of the tether (aka lanyard), and, from that, determine the impact force that object will have when it is suddenly stopped by either the tether or the ground (hopefully, the ground and not a person below).
This force is many magnitudes higher than the just the simple mass of whatever was dropped. A 10-pound weight dropped 120 inches has an impact force of 460 pounds! To test the DOP device, a lab attaches it on a static (not moving) tensile testing rig and pulls or stretches it from both sides. The lab increases the force on the device until it breaks. If it breaks with a force higher than the minimum impact force, then it passes and is deemed safe for use. If it breaks at a force lower than the impact force, it's back to the drawing board or to a lower weight rating. You also get nice-looking graphs like this one, below, showing the load and the displacement (how much the tether stretched) as an output of the testing.
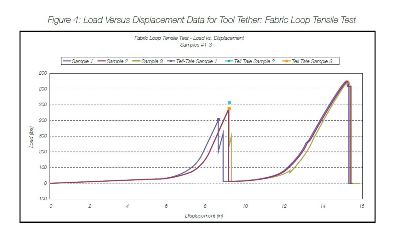
Seems simple, right? What could be better?
There is one problem with static testing. Static testing is an excellent way to determine how much force a safety device can withstand before it breaks (called load capacity) when it is pulled straight down and everything is perfectly aligned. However, in real life, objects dropped rarely fall straight down. They tend to swing, ricochet off structures and scaffolding, bounce, and recoil in unpredictable ways. Want to see how violent this really is? Here is a short clip simulating a real-life drop. As in the example above, the weight is 10 pounds dropping 120 inches:
https://www.youtube.com/embed/IlY9_loXa6s?rel=0
A device may pass a static test with flying colors, but when put into a real-life situation, when the straps or cable, d-rings, carabiners, and other parts are stressed and strained in ways that are not perfectly aligned by gravity, motion, and dynamic force, it may still fail and break, and that's bad for anyone standing underneath. This is something no contractor, worker, or manufacturer wants to discover on the job site, where lives are at stake.
With a dynamic drop test, an object of known weight is dropped multiple times. If the device prevents a drop, it passes. If it breaks and the object drops, it fails. The device is still subjected to the same impact force as it would be in a static test, but with the added challenge of proving the total solution can withstand the stress and strain of swings, bounces, and recoils real devices are subject to every day. When (not if) things don't perfect align during the test, the device must still fight off gravity and prevent a drop, and that is something you just can't simulate with a static test.
If it was you standing below someone working at height, how would you want their tethers tested? If it was me, I'd be sure to ask my DOP supplier to produce their dynamic drop testing certificate before I'd let my teams work at height.
This article originally appeared in the December 2018 issue of Occupational Health & Safety.
About the Author
Nicholas Voss is Director of Product Management for West Coast Corp in Ontario, Calif. He worked in the oil and gas industry for 15 years before moving to his current home at WCC. Better known as KEY-BAK Pro, WCC has been manufacturing retractable solutions in the USA since 1948. As a member of the ISEA committee for dropped object prevention standards, Nick and WCC are committed to developing new products that help make tomorrow a little bit safer than it is today. Building on his experiences in the oil and gas industry, Nick had launched the START Work Fundamentals, designed for any organization to deploy a dropped object program founded on continuous improvement. For more information, visit www.dropsafetyequipment.com.