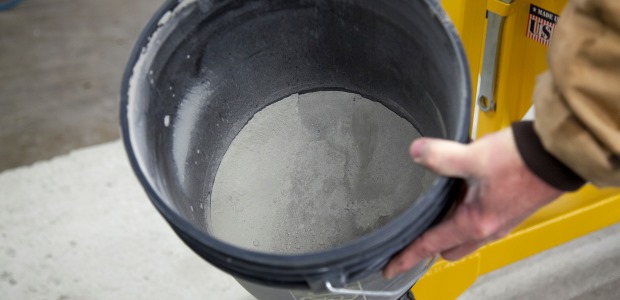
Don't Get Left in the Dust
Here's how to easily and successfully meet OSHA standards with your concrete drill.
- By Rick Walstad
- May 01, 2018
The changes have been made, regulations have been implemented, and thousands of dust collection systems are hitting the streets—OSHA's Table 1 requirements are in full effect. While the regulation itself may seem cut and dried, when it comes to implementing the changes, things can get a little clouded. Here are some guidelines to help clear the air.
What's the Issue with Silica?
Silica is a mineral found in a variety of materials, including concrete, masonry, and rock. As these materials are drilled or cut, they disperse dust particles that, according to OSHA, can be as much as 100 times smaller than a single grain of sand. The organization recognizes this is where the problem with silica dust lies; those particles are tiny enough to settle deep into the lungs when inhaled, which can lead to silicosis, an incurable lung disease. Exposure also can lead to other serious or life-threatening diseases, including lung cancer, tuberculosis, and kidney disease.
The Regulations
OSHA mandates that contractors who break, chip, cut, or drill into concrete must have a dust collection system that captures at least 99 percent of the dust created during operation. This means respirable silica dust levels must be at or below 50 micrograms per cubic meter of air over an eight-hour shift. In addition, employers must also ensure operators, as well as those working in close proximity to the drill, wear fit-tested dust masks with an assigned protection factor of 10, or APF 10.
Following the guidelines not only enhances the safety and the health of workers, but also ensures contractors avoid hefty fines. As of January 2018, OSHA's penalty for first-time-violations is $12,934 and is $129,336 for repeated or willful violations.
For those unsure whether their current system is up to par or if they need a system at all, they can have a local environmental representative perform a sampling and analysis.
How Does a Dust Collection System Work?
Dust collection systems are available for all types of concrete drills, from single- to five-gang units and even handheld drills. The systems include a shroud that surrounds the drill bit and connects to a hose leading to a dust canister, where collected dust is stored. These canisters generally hold about 5 gallons of material, but larger bags are also available for use with many systems, which minimizes the frequency of cleanouts.
How Will the System Affect My Operation?
Contractors can purchase a dust collection system with a new drill or have their dealer retrofit it onto an existing drill. Depending on how many gangs the model has, the size air compressor needed to power the system along with the drills varies, as does the number of dust canisters, which ranges from one to three.
For example, a single-gang slab-rider needs 100 cfm to operate and an additional 40 cfm to power its single-canister dust collection system. This means a contractor can continue to use its 185-cfm compressor after adding the system. While a two-gang slab rider may not need another canister for the dust collection system, it will require 60 cfm to operate and 200 cfm for the drill, 100 cfm per gang. To power all of the equipment effectively and efficiently, contractors will need to bump up to a 260-cfm compressor.
Keep in mind, however, not all dust collection systems are the same. One manufacturer's unit may require 40 cfm per gang, while another may require 50 cfm. This can be the difference between using an existing compressor or having to purchase a new, higher cfm model.
While adding a dust collection system may call for a larger compressor, the system has a minimal effect on daily operations. However, there are a few things operators will need to keep in mind to ensure the drill operates as efficiently as possible. Purging should be done every two or three sets of holes. This removes any built-up dust from the filter so the system will continue to collect dust with optimal efficiency. Operators also will need to occasionally empty the collection bucket or bag.
Respiratory Protection
Even though collection systems are extremely effective at capturing and containing dust, OSHA's Table 1 requirements require employers to also provide operators with another level of protection via respirators with an assigned protection factor of 10. The respirator manufacturer 3M explains this as meaning the respirator will reduce the user's exposure to dust by a factor of 10. So, when fitted and used properly, an APF 10 filter can safely be used where hazardous concentrations are up to 10 times the Permissible Exposure Limit.
Both filtering facepieces, also known as dust masks, and elastomeric half-mask respirators offer the appropriate protection factor, using negative pressure as the user inhales and a filtration method to purify the air. Dust masks, however, cost less and can be thrown away once they've reached their end of life. If the mask is damaged, soiled, or its shape has been compromised, the mask can no longer provide adequate protection and should be tossed. Elastomeric half-mask respirators feature washable filters or disposable rubber-like facepieces.
To ensure the respirator fits the operator and can effectively do its job, contractors must fit test each employee. This ensures the size, make, model and style are matched to each individual's facial structure. This must be done at least once per year or when changes, such as scarring, weight gain, or weight loss occur. OSHA requires contractors use one of two methods to determine proper fit: qualitative or quantitative. A qualitative fit test relies on the user's sense of taste or smell, or reaction to an irritant. A quantitative fit test, on the other hand, uses a machine to measure the amount of leakage. If the respirator fails the fit test, another size, make, model, or style must be chosen and tested. Facial hair can also cause issues when it interferes with a mask's seal, allowing dust to enter the mask.
In addition to an annual fit test, ensure operators perform seal checks each time they use the mask. This confirms the mask is properly seated to the face. Refer to the OSHA and NIOSH websites for more information.
Train Your Team
One of the best ways contractors can ensure they are consistently following OSHA's silica guidelines is to train operators on the Table 1 requirements, why those guidelines are important to follow, and how to follow them.
Outside of general drill operation, be sure operators understand that using an air compressor to blow off surfaces, clothing, and filters increases exposure to silica and should not be done. Contractors need to instead provide a HEPA-filter-equipped vacuum that employees can use to remove the dust.
Create a Written Plan
Ensure all team members are on the same page with how the business will adhere to the guidelines by assembling a written plan. In fact, a written plan is required by OSHA and should include four things: 1) a list of all tasks that expose employees to respirable crystalline silica dust; 2) how the contractor will reduce exposure levels to acceptable limits; 3) housekeeping initiatives to help minimize exposure; and 4) how the contractor will minimize the number of employees working with respirable silica dust.
To help ensure the guidelines are being met on a company-wide level, it's a good idea to designate a point person who can make frequent job site inspections, answer questions, and address any changes that may need to be made to equipment or procedures.
What Should I look for When Choosing a System?
When choosing a dust collection system, keep productivity in mind. Look for units with kits that make installation easy and that have a filter with a large surface area that can be easily purged.
Further, research the manufacturer. Simple vacuum units may not pass new regulations. Choose a manufacturer with a history of experience in dust collection system manufacturing to assure quality and a good ROI.
Ergonomics is also something to consider, particularly when it comes to purging the dust system, since that should be done frequently. Choose a system with easy-to-access purge levers.
Health and safety continue to drive changes on the job site. While change may not always be met with open arms, preparing for it will ensure no one is left in the dust. For more information on OSHA's crystalline silica dust guidelines, visit www.osha.gov.
This article originally appeared in the May 2018 issue of Occupational Health & Safety.