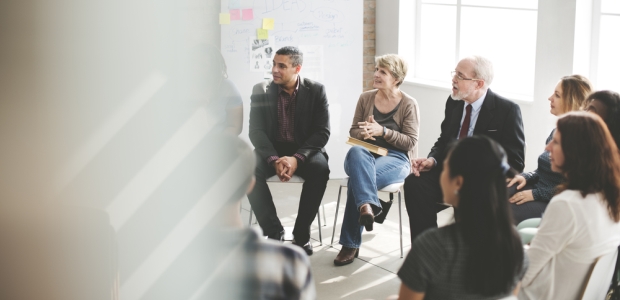
BBS and Leadership Analytics: Using Your Big Data to Engage Your Team
To assess their leadership engagement, safety professionals can poll their employees to determine the amount and the quality of BBS information disseminated.
- By Chuck Pettinger
- Aug 10, 2016
Many business publications often refer to "big data," "predictive analytics," or "business intelligence" as a huge differentiator in moving a good company to a great one. If big data and predictive analytics are not already a part of your job, they soon will be. And there is no better area in an organization to start than in the safety department.
The safety field collects a plethora of safety intelligence, from training records to safety observations. Unfortunately, after an initial assessment, this critical safety intelligence is often stored away and goes mostly unused. So, to evolve our safety cultures, we need to gather all of our safety "big data," put this critical information to use, and get our leadership teams to become truly engaged in using our valuable safety indicators.
Much of the safety data gathered by most organization comes from some sort of safety audit or inspection. These processes are used to gather information on the effectiveness of their safety management systems. Companies also gather a lot of data from behavior-based safety (BBS) observations.
For close to 40 years, consultants, safety professionals, insurance companies, and professors have been helping companies and our communities identify, reduce, and eliminate injuries through the application of the science of Behavior Analysis and interpersonal feedback (BBS). Even though many have questioned the effectiveness of behavioral safety, there are hundreds of articles focusing on the impact, philosophy, and success of behavior-based safety. Organizations that have struggled or reach a plateau with BBS have either failed to demonstrate the value of the process by not making use of their data and/or have not fully gotten their leadership engaged in supporting the process. To revitalize a stale BBS process or to set up your organization's new BBS process for success, try getting your team engaged with "leadership analytics."
Leadership Analytics
Measuring leadership's engagement can easily be accomplished through using the observation intelligence gained from your BBS process. To begin, organizations need to assess the quality of their observation data. This gives us two valuable pieces of cultural information that can be acted upon by our leadership team.
First, look at your BBS data trends to give your leaders a focus for improvement. Even more importantly, provide rewarding safety-related feedback to workers. One example of leadership analytics comes from a manufacturing facility that developed a simple, 3x4 "Focused Feedback" card to track these activities. This tracking method is simple, easy to track, and is publicly posted and talked about in weekly meetings. Leaders get recognized by the plant manager for submitting quality feedback cards, and the quantity of cards is used in their performance plan.
A second piece of cultural information from our BBS data comes in the form of a quality assessment. By looking at how the BBS observations are completed, we can gain insight into the engagement of your observers. For instance, companies suspect that many of their observations are "pencil-whipped" (just checking off boxes without observing) and do not trust their data. In addition to looking at the quantity of observation turned in, look at what proportion of your observations are turned in 100 percent safe. Some might argue that 100 percent safe is the ultimate goal. On the contrary, 100 percent safe observations either means you have a cultural issue with pencil-whipping as the indicator—or you are that good and the 100 percent means you should change up your checklist. Another cultural proxy of good culture can be measured by looking at the proportion of at-risk observations with an associated comment/picture.
By assessing the quality of their BBS observations, companies can start to get an idea of what "real" observations look like. If your quality is struggling, your leaders may be failing to communicate their BBS data or the culture as a whole is not supportive. In either case, leadership analytics can point to areas your leaders can engage with the employees or demonstrate the value of the information by acting on the issues identified.
Demonstrating Value
Organizations with world-class safety cultures who are leading the field in BBS are very good at demonstrating the value of BBS. This can be accomplished in many ways, but the most common is creating a "data-use plan." This plan outlines how the organization is going to put its observation intelligence to work. Typical BBS reports include:
1) Observer Summary: Observations completed by each participant
2) Data Summary: Safe, at-risk counts and comments with quality metrics
3) Area/project Summary: Safe, at-risk comments and quality for larger groups
4) Open Issues Report: Tracks issues identified and closed
A good, quality plan consists of identifying which of the above reports will be used by which leaders and will answer the following questions:
1) How often will the reports be run (daily, weekly, monthly, or quarterly)?
2) What information is captured?
3) What value does the report provide the organization (why is it important)?
4) How will each of the reports be shared (meetings, posting, communication boards)?
Once a detailed communication plan is developed, leaders can be held accountable for working the plan. To assess their leadership engagement, safety professionals can poll their employees to determine the amount and the quality of BBS information disseminated.
Putting Your Data to Use: Predictive-Based Safety
Once a solid data-use plan is in place, now is the time to put your observation intelligence to work. At your regularly scheduled meeting where you review your BBS data, use the "week-look-back/week-look-ahead" to prescribe where your observations should focus (or monthly, depending upon your frequency of meeting). This can be accomplished with the leadership team or your BBS/safety teams.
By looking at the past week of data, you can identify where risky things were observed and follow up on those areas. If there are any safety open-issues that need to be closed or followed up on, this could be a focus for observations. You also can identify areas or places that have not been observed and perform observations on those locations. The week-look-back can help identify which observers are participating and also help to assess the quality of their observations. If there were any injuries/incidents, you can also use this look back to see whether your data would have predicted the issue.
Once you have looked back, now take a look ahead. Are there any good opportunities for observations? Maybe there is a contractor on site. Maybe we are performing annual maintenance. Maybe it's the first day back after a long weekend. The week-look-ahead helps organizations use their data, provide value, and helps to engage their leaders.
The idea is to prescribe your observations using your data intelligence, instead of performing "observations of opportunity." By using this week-look-back/-ahead method, we are using our data to be more of a predictive-based safety process. Our BBS process, along with using our leadership analytics, can help to proactively identify issues, create a more fact-finding process, help engage our leaders, and eventually eliminate death on the job this century.
This article originally appeared in the September 2016 issue of Occupational Health & Safety.