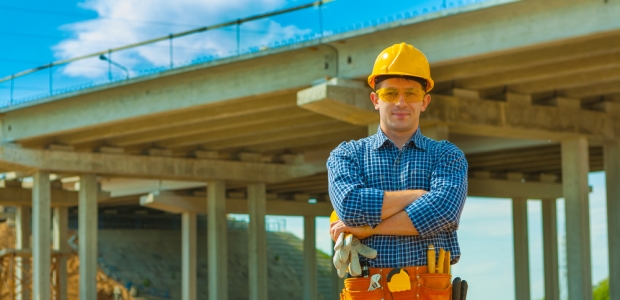
Keeping Hand Injuries in Check
With 139,820 lost-time cases resulting from hand injuries in 2013 alone, according to BLS, this is one of the higher incidence rates among all injury types.
- By Fred Elliott
- Apr 01, 2015
The U.S. Bureau of Labor Statistics delivered some holiday goodies, as well as a few lumps of coal, on Dec. 16, 2014, when it released data on non-fatal lost-time occupational injuries and illnesses during 2013. The overall incidence rate fell to 109.4 cases per 10,000 full-time workers that year, down from 111.8 the year before, and the median number of days away work also fell from 9 to 8. That's the good news.
However, the total number of days-away cases in 2013—1,162,210—was essentially the same as in 2012, BLS reported, and it also noted that musculoskeletal disorders accounted for 33 percent of all injury and illness cases in 2013 and accounted for 53 percent of total cases involving nursing assistants that year. For male workers, the third-highest incidence rate in 2013 for any category of injury was cuts, lacerations, and punctures, and there were 98,680 lost-time cut, laceration, and puncture cases during the year, according to the BLS data tables.
The occupations with the largest number of lost-time cases that year included nursing assistants; heavy and tractor-trailer truck drivers; laborers and freight, stock, and material movers; janitors and cleaners; construction laborers; and police and sheriffs’ patrol officers.
When BLS listed the number of 2013 lost-time cases according to the affected body part, upper extremities topped the list with 345,560—and 41 percent of them (139,820 cases) were hand injuries. Their median number of days away from work was six days.
Interestingly, the age group with the highest incidence rate for workplace lost-time hand injuries that year was 16-19.
Machinery, Cutting Hazards Predominate
What kinds of serious hazards can place employees' hands at risk? Hazards associated with machinery and cutting injuries top the list.
The hazards vary, of course, but a February 2015 enforcement case from OSHA's Region 5 is a recent example. Region 5 cited a steel tubing manufacturer, fined the company $139,800, and placed it in OSHA's Severe Violator Enforcement Program for repeat and serious machine guarding violations found at its Alliance, Ohio, facility. One serious citation item, with a $70,000 proposed penalty, involved employees' exposure to knife cutting injuries on two mill weld lines from reaching under the equipment to tighten and service equipment and from climbing above the equipment to hammer worn knives down. Another citation item for the repeat violations listed 17 types of equipment in the facility where employees were not protected from cutter, saws, moving parts, and pinch points, according to OSHA.
"Each year, thousands of workers are injured by dangerous machinery. These types of violations are among the most frequently cited by OSHA and often result in death or permanent disability," said Brigitte Frank, OSHA's acting area director in Cleveland, Ohio.
Another February 2015 enforcement case from the Parsippany, N.J., Area Office, in OSHA's Region 3, also cited amputation hazards and inadequate machine guarding. In this case, OSHA cited a Madison, N.J., manufacturer of carbide steel cutting tools for two willful violations for inadequately guarded or unguarded machinery, and the agency proposed $56,000 in fines. "OSHA previously cited this company for the same amputation hazards involving the same machinery, yet it continues to jeopardize worker safety by not ensuring the proper safeguards are in place. The proposed penalties in this case reflect the severe nature of the cited hazards," said Kris Hoffman, director of the Parsippany Area Office.
Hand injuries are difficult to repair because our hands are complex "tools," if you will, that are crucial to our performance of so many fundamental tasks. Suffering a loss of dexterity, motion, or gripping power in our hands—much less an amputation—can jeopardize our ability to perform basic life tasks. This fact is recognized by U.S. states' workers' compensation programs, most of which use a list of body parts that are covered by permanent partial disability benefits, which cover the most expensive category of cases in most states, according to an analysis published in the 2003/04 Social Security Bulletin by the U.S. Social Security Administration’s Office of Policy. The lists "invariably include the upper and lower extremities and may also include an eye. Most include the loss of hearing in one or both ears. The schedules are specific enough that they separately identify the individual fingers or toes or differentiate between the loss of a dominant or nondominant hand," Peter S. Barth explained in this paper.1 He noted that a nine-state study that examined the costs of cases as of March 2002 for injuries that had occurred in 1998-1999 found more than half of the cases in which temporary disability lasted more than seven days resulted in permanent partial disability in six of the states, with the median cost for such cases in the nine states topping $32,000.
Key Hand Protection Standards
The important hand protection standards for the U.S. market are ANSI/ISEA 105-2011, American National Standard for Hand Protection Selection Criteria, and OSHA's 29 CFR 1910.138.
The OSHA standard states:
General requirements. Employers shall select and require employees to use appropriate hand protection when employees' hands are exposed to hazards such as those from skin absorption of harmful substances; severe cuts or lacerations; severe abrasions; punctures; chemical burns; thermal burns; and harmful temperature extremes.
Selection. Employers shall base the selection of the appropriate hand protection on an evaluation of the performance characteristics of the hand protection relative to the task(s) to be performed, conditions present, duration of use, and the hazards and potential hazards identified.
The ANSI/ISEA 105-2011 standard (visit www.safetyequipment.org for information) includes a recommended hand protection selection procedure, as well as a section that describes how fit, function, and comfort are incorporated into selection, according to ISEA. It also includes a rating system for classifying hand protection PPE against various performance assessments, and it accepts different ASTM methods for evaluating gloves' cut resistance.
"As leaders in cut-resistance solutions, ISEA members spent a significant amount of time trying to reconcile the differences between the varying cut resistance methodologies that are widely accepted in the industry," Matt Reid, America Area manager of DSM Dyneema and the ISEA Hand Protection Group's chairman, said in February 2011. "We believe that allowing both test protocols represents the transition toward a single evaluation method, with appropriate classification levels, without creating a gap in a much-needed user resource. It will be important for end users to ensure that any comparison between gloves, first and foremost, be based on the same test method. ISEA member companies keenly understand that there is a wealth of information in the market to help in the glove selection process. We are certain that ISEA's standardized template will be a valuable tool to streamline comparisons and make the decision process easier."
References
1. http://www.socialsecurity.gov/policy/docs/ssb/v65n4/v65n4p16.html
2. https://www.osha.gov/oshstats/index.html
This article originally appeared in the April 2015 issue of Occupational Health & Safety.