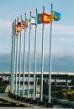
FAA Mandates Center Fuel Tank Inerting Technology
Within two years, all new aircraft must include technology designed to significantly reduce the risk of center fuel tank fires as part of a final rule announced Wednesday by U.S. Transportation Secretary Mary E. Peters. In addition, passenger aircraft built after 1991 must be retrofitted with technology designed to keep center fuel tanks from catching fire, she said. "We want to do everything possible to make sure safety examiners won’t have to investigate another plane shattered by an exploding tank," Peters said. "We can't change the past, but we can make the future safer for thousands of air travelers, and this rule does just that."
Peters, who spoke on the day before the 12th anniversary of the crash of TWA Flight 800, said the new rule was needed to help avoid a similar tragedy. She said the rule requires aircraft to have technology to neutralize or eliminate flammable gases from fuel tanks under the center wing of commercial passenger planes.
In the wake of the TWA crash, researchers with the Federal Aviation Administration developed a breakthrough system that replaces oxygen in the fuel tank with inert gas, which effectively prevents the potential ignition of flammable vapors. She added that commercial aircraft manufacturer Boeing also has developed a similar system. "Today’s rule will add another layer of safety, reducing the chance that the vapors in the tank will ignite, even if there is a spark," said FAA Acting Administrator Robert A. Sturgell.
Peters said the cost of installing the new technology would range from $92,000 to $311,000 per aircraft, depending on its size. The U.S. aircraft that will be retrofitted include approximately 2,730 aircraft belonging to the A320 family of 900 airplanes, 50 A330s, 965 Boeing 737s, 60 Boeing 747s, 475 Boeing 757s, 150 Boeing 767s and 130 Boeing 777s.
The rule is published on the FAA's Web site at www.faa.gov/regulations_policies/rulemaking/recently_published and in the Federal Register.