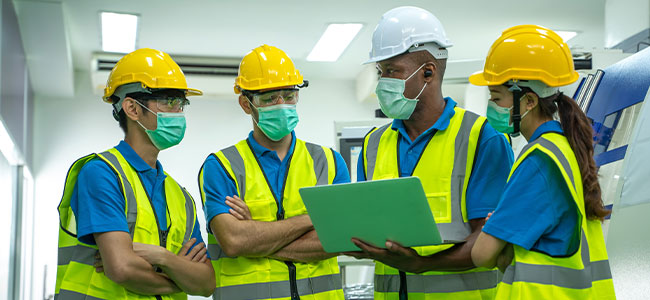
Industrial Hygiene: The Science Behind Safety
Safety on the job is no accident. Industrial hygiene is the science of protecting workers’ health and safety.
Going to work shouldn’t be dangerous. Yet, 5,486 fatal work injuries were recorded in the U.S. in 2022. The construction industry had the most workplace deaths; transportation and warehousing had the highest injury and illness rate tied to days away from work per 10,000 workers.
The three leading causes of work-related injuries/illnesses in 2021-22 were 1) Exposure to harmful substances/environments, 2) Overexertion & bodily reaction, and 3) Slips, trips & falls.
These top three hazards account for more than 75 percent of all nonfatal injuries and illnesses involving days away from work.
So, what can employers do to help keep workers safer? One way is to implement an industrial hygiene program.
What Is Industrial Hygiene?
Hygiene is the science that deals with the preservation of health. Industrial hygiene is the science of protecting workers’ health and safety. OSHA expands the definition to the science and art devoted to the anticipation, recognition, evaluation, and control of environmental factors or stresses arising in or from the workplace, which may cause sickness, impaired health and well-being, or significant discomfort among workers or the community.
The process of industrial hygiene involves identifying, analyzing and controlling workplace conditions and hazards to prevent dangerous and harmful work environments. It can help prevent potential illness, injury, and stressors at workplaces.
By incorporating industrial hygiene principles early in your planning and recognizing potential issues before they escalate, you can support the health and safety of your workers and manage your company’s exposure to potential risk and liability.
Industrial hygienists use environmental monitoring and analytical methods to detect the extent of worker exposure to hazards. They utilize engineering, work practice controls, and other methods to control potential health risks. Another common way to practice industrial hygiene is by mandating proper use of Personal Protective Equipment to improve working conditions, provide protection and mitigate workers’ exposure to hazards.
OSHA Standards
OSHA places a high priority on using industrial hygiene concepts in its health standards and as a tool to enforce regulations.
Today, nearly every employer is required to implement an industrial hygiene and safety, occupational health, or hazard communication program and to be responsive to OSHA and its regulations. Under the OSH Act, OSHA develops and sets mandatory occupational safety and health requirements applicable to the more than 6 million workplaces in the U.S. Some examples of OSHA standards involve requiring employers to prevent exposure to infectious diseases/harmful chemicals, ensure the safety of those working in confined spaces, and provide fall protection, training for dangerous jobs, and safety equipment such as PPE.
Four Steps of Industrial Hygiene
Industrial hygiene strives to reduce or remove work hazard exposure by implementing a series of controls and programs to keep the workplace clean, free from environmental stressors, and hygienic.
1. Workplace Analysis. OSHA describes a workplace analysis as the essential first step that helps industrial hygienists to determine what jobs and workstations are the sources of potential problems. Examples include inventories of hazardous materials and chemicals, reviewing accident and incident reports, incident investigations, job hazard analysis, routine worksite inspections, and analysis of injury and illnesses.
2. Identify Hazards. The second step involves identifying workplace conditions and hazards to prevent dangerous and harmful work environments. These risks can fall into different categories, including biological hazards (viruses and bacteria), chemical hazards (vapors and fumes), physical hazards (heat and radiation), airborne contaminants (aerosols), and ergonomic hazards (lifting or pushing heavy equipment).
3. Put Controls In Place. Once the workplace hazards have been identified, the next step is for an industrial hygienist to put proper controls in place to eliminate or reduce the risk of the hazard. OSHA lists three different controls that can take place:
• Engineering controls: Either reduce or remove hazards at the source or isolate workers from the hazard.
• Work practice controls: Alter how the task is performed. This can include changing work practices, maintaining equipment, prohibiting food and drinks, etc..
• Administrative controls: Reducing exposure by scheduling production and tasks during the lowest exposure potential hours.
4. Personal Protective Equipment. The final step revolves around PPE. While engineering controls are being instituted, or if they’re not possible, appropriate PPE must be used, used properly and be applicable to the hazards in place. Various categories of PPE include respiratory protection, fall protection, hand protection, hearing protection, eye protection and face protection.
Examples of PPE products include gloves, safety goggles, helmets, safety shoes, earplugs, harnesses, protective clothing, and respirators.
For more information, OHSA has published rules and standards at www.osha.gov/personal-protective-equipment.
This article originally appeared in the April/May 2024 issue of Occupational Health & Safety.