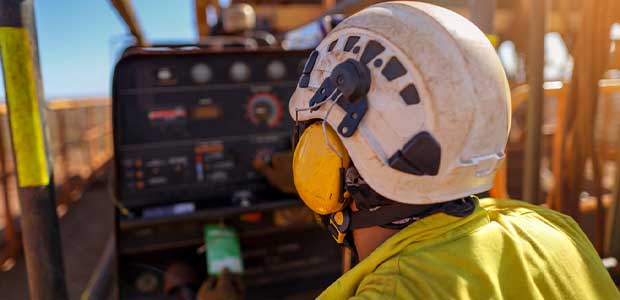
Hear Ye, Hear Ye: Using PPE to Protect Your Hearing
Protecting workers’ hearing is a team effort.
- By Randy DeVaul
- Dec 01, 2022
Hearing loss continues to be prevalent in work-related environments, and yet, this loss is 100 percent preventable. One can point to the employer as having responsibility, but we cannot ignore the employee’s personal responsibility as well. When a person fails to protect his or her hearing in a regulated work-related environment, it is no wonder that noise-induced exposures outside work also remain a concern.
As of 2019, 430 million people globally suffer from disabling hearing loss. In the U.S., 51 percent of the adult population report some level of hearing difficulty, with 13 percent identifying their loss as needing treatment. Our world is full of noise, and it seems that people have become complacent about maintaining good hearing health.
We all know identifying noise-induced exposures in the workplace requires conducting a risk assessment followed by documenting and creating action plans to reduce or remove exposures. Once identified, follow the hierarchy of controls: eliminate or reduce the noise level at the source through engineering controls; enact administrative controls through procedures and employee rotation; once all other controls are considered and done, establish a Hearing Conservation Plan (HCP) following OSHA requirements and identify the people and the PPE needed to reduce noise exposures.
An HCP, including making hearing protection available for affected employees, may be required. The simplest way to determine where and what exposure levels are (work areas, specific equipment) is with an inexpensive digital sound meter. This allows you to “map” noise levels, which can then be followed up with dosimeter sampling of employees in high-noise areas and validate the work areas that do not require an HCP.
It is imperative for employers to have a proactive HCP where the decibel level is 85 dBA (using the “fast A scale) or greater. Being proactive reduces (or prevents) having to report threshold shifts or hearing loss as an occupational illness. In my 40-year career as a safety professional, I never had a single employee tagged with a hearing shift or loss from annual audiogram results because I was able to show any shift as a non-work-related exposure.
The risk assessment findings and the implemented HCP will guide you in the selection of the right hearing protection. Modern technology today has provided several options that can be used to protect employees’ hearing. From traditional disposable and reusable earplugs and earmuffs to innovative noise-canceling inserts, there is no reason for any employee to have noise-induced hearing loss—whether at work or outside of work! Losing one’s hearing due to exposure to noise is unnecessary if the risk is known and precautions are taken.
OSHA’s Hearing Conservation Program standard (1910.95) gives the employer and the employee the information needed to protect hearing and be in compliance at work. One of those requirements for employees participating in an HCP is for the employer to provide a few types of earmuffs and earplugs for employees to choose what works best for them. Ask your safety distributor or manufacturer’s representative for samples to determine which styles are better suited for your employees prior to making a large purchase. Having your employees participate in the sampling and provide feedback will ensure buy-in and increase the wearing of the PPE in exposure areas. As the employee becomes more aware of noise exposures and how easy it is to be protected from them, proactive steps can be taken outside of work, as well.
When the decibel level is known, it is easier to select the proper noise reduction rating (NRR) needed to remain safe from the noise hazard. Each hearing protector is labeled by the manufacturer with the NRR number. For practical use, that NRR number should be cut in half and then subtracted from the measured decibel level. The objective is to keep the employee’s exposure below 90 dBA to prevent noise-induced damage to the ears once the hierarchy controls have been evaluated and put in place.
Just like other PPE types, there is not one hearing protector that works for every noise-induced hazard nor just one that is best suited for all employees. This is why OSHA requires more than one type of hearing protection to be made available. Based on the various shapes and styles of earplugs, it is reasonable to offer a couple of different shapes along with one earmuff style.
The purpose of providing an earmuff is twofold. One, an earmuff might be necessary for noisy areas that register 100 dBA (OSHA) or 105 dBA (MSHA) or louder, as dual hearing protection is required to reduce the exposure to 90 dBA or below. This would require the use of plugs and muffs during that exposure time. If the decibel exposure remains above 90 dBA after dual protection is in place, administrative controls with rotating employees out of that area would also be required.
The second purpose of providing earmuffs is for employees who, over time, suffer from impacted ear wax from daily use of ear plugs. Some are more prone to this condition, but many can suffer from it, over time. The use of muffs allows the wearer to alternate or change protection to prevent repeat occurrences.
Exposure to 90 dBA for a time-weighted average of eight hours is the magic number for wearing hearing protection. Any amount of time beyond eight hours at 90 dBA without protection has been proven to cause hearing damage, resulting in permanent hearing loss over time. The 85 dBA threshold for initiating an HCP is to ensure employees remain under 90 dBA to prevent permanent loss and to ensure quality of life as the employee ages while remaining exposed to that noise level.
Employers must ensure employees are working in an environment that is free from recognized hazards or protected from those that cannot be eliminated. Employees are responsible for working in a safe manner and wearing the provided PPE to protect them from those known hazards. It is a team operation where everyone is expected to do their part.
This article originally appeared in the December 1, 2022 issue of Occupational Health & Safety.