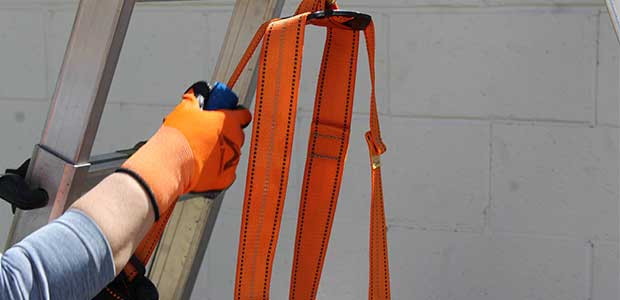
How and When to Clean Your Safety Equipment
By now we all know to wash our hands, but what should be done with shared PPE, such as full body harnesses and fall protection lanyards?
- By David Ivey
- Aug 01, 2020
As the construction industry ramps back up this summer, there is a focus on cleanliness and safety in shared workspaces, particularly around how to keep shared equipment clean. The health crisis has forced many of us to rethink how we clean and maintain our facilities and our gear. By now we all know to wash our hands, but what should be done with shared PPE, such as full body harnesses and fall protection lanyards?
Unfortunately, the sanitizers used to wipe down our hands are not safe to use on many pieces of equipment, and neither are bleach and other harsh cleaning products. Fall protection equipment in particular relies on the integrity of the material in order to function, so any harsh cleaners or chemicals can’t be used to sanitize these items.
So how can you clean shared safety equipment effectively?
How to Clean Personal Safety Equipment
As a general rule, start by checking the manufacturer’s product instructions for care and maintenance of any safety equipment. For personal fall protection equipment, material integrity is vital to its function and there are some general guidelines you can follow to disinfect without compromising the material. The same general rules can be used to clean other PPE such as gloves, safety glasses, hard hats and visors. Thankfully, cleaning these types of equipment doesn’t require any special products—just clean tap water and mild soap such as liquid dish detergent.
This combination is effective in killing the COVID-19 virus, inexpensive and safe for the integrity of the equipment. Cold or warm water will work equally well, but avoid hot water above 130 degrees Fahrenheit (54.4 degrees Celsius) that can damage some equipment.
All it takes to sanitize the gear is to wipe it down with soapy water using a damp cloth or sponge, and then rinse it with clean water to remove any soap residue. There is no need to soak or submerge the gear. After it’s clean, allow it to hang-dry in an open, well-ventilated area to prevent mold, but do not machine dry PPE, as this can damage it.
Chemicals and cleaning products such as sanitizers, rubbing alcohol, bleach, hydrogen peroxide, naphtha, turpentine, acetone or other industrial cleaning supplies are unnecessary, and are not recommended for cleaning personal fall protection equipment of any kind, as these chemicals can damage the integrity of the material you rely on to keep you safe in the event of a fall.
How Often to Clean Equipment
It is always a good practice to keep your equipment clean, but it’s especially important in this time of heightened risk from a potentially dangerous virus. As long as the contagion is making the rounds, it’s safest to clean the equipment in between each use. Consider making regular cleaning of your gear part of your process by adding it to your inspection forms or checklists. Because of the need to let equipment dry, it may make the most sense to make your policy to clean the equipment after using it each time, ensuring that clean gear is always available to the next worker who needs it.
Shared Equipment Policies
It has always been best for each employee to have his or her own safety equipment, to ensure that each worker has gear that fits properly and is comfortable for the individual to wear. Now there is more reason than ever to provide each worker with his or her own personal fall protection equipment and other safety apparel in order to minimize contact between employees and shared gear.
If workers must share communal equipment, cleaning the gear between each use before passing it on to the next employee is essential for safety during the pandemic.
As strange as it may sound, treating low-cost personal safety equipment such as work gloves and safety glasses as disposable items may be another approach to minimizing the spread of germs. These items can be cleaned regularly, of course, but it may prove more cost effective to simply discard inexpensive items at the end of a shift instead of investing the time into sanitizing them after each use. Think about what an employee gets paid per hour and ask yourself whether it’s worth them spending 15 minutes cleaning a three-dollar item, then build your policy accordingly.
Other Best Practices to Follow During the Pandemic
The Centers for Disease Control (CDC) and the World Health Organization (WHO) have provided general guidelines to follow to prevent the spread of COVID-19. Wash your hands regularly with soap and water for 20 seconds, or use hand sanitizer with an alcohol content of 60 percent or more.
Whenever possible, maintain a physical distance of at least six feet (two meters) from other workers, even those who do not appear to be sick. The CDC recommends wearing cloth face coverings in settings where physical distancing measures are difficult to maintain, such as on jobsites where workers must be in close proximity. These recommendations are especially important in areas of significant community-based transmission of the disease.
The CDC does not recommend using surgical masks or N-95 respirators because these are critical supplies that must continue to be reserved for healthcare workers and other medical first responders who are in frequent close contact with sick patients.
This article originally appeared in the August 2020 issue of Occupational Health & Safety.