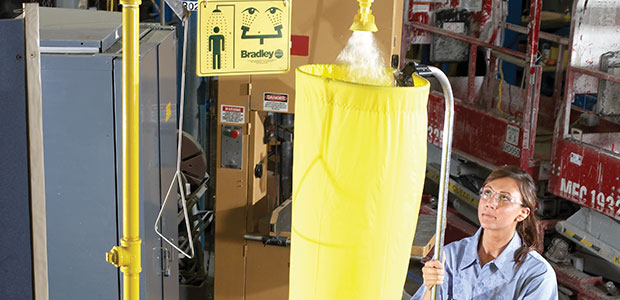
Page 2 of 3
Weekly Testing Ensures Eyewash/ Safety Shower Protection and ANSI Compliance
You may remember that long, high-frequency and screeching tone on your television or radio: “This is a test of the Emergency Broadcast System. This is only a test.” (In the actual event of a local, state or national emergency, vital information would then be announced.)
Whether it’s the Emergency Broadcast System1 or your facility’s plumbed emergency fixtures, testing is an essential part of ensuring that emergency systems work. Regular testing is a failsafe way to validate operational readiness and identify areas for improvement.
Emergency eye wash and shower equipment are used by people in dire exposure situations. Therefore, it makes perfect sense that these fixtures are inspected, tested and verified weekly to ensure immediate, reliable and proper usage. Weekly safety equipment tests are also required by the ANSI/ISEA Z358.1 standard (with a more in-depth evaluation to be conducted annually). Violations for inappropriate or inadequate equipment may result in costly penalties, not to mention the possibilities of life-altering injuries.
Work settings that involve hazardous materials are oftentimes in flux. ANSI’s definition of “hazardous material” includes caustics, as well as additional substances and compounds that have the capability of producing adverse effects on the health and safety of humans. Changes in materials, employees, machinery, operations and worksite risks are a moving target. Weekly tests and inspections ensure the placement and readiness of each fixture in such dynamic work environments.
Each weekly inspection should check that plumbed emergency equipment:
- is in compliance with the ANSI/ISEA standard
- works properly with no missing or broken parts
- was flushed to clear debris and stagnant water
- is protected against freezing
- uses tepid fluid between 60- and 100-degrees Fahrenheit or 16- and 38-degrees Celsius Here are guidelines on how to ensure compliance with ANSI weekly minimum performance requirements:
Per ANSI/ISEA Z358.1, emergency drench showers, eye and eye/face washes must be inspected and activated one time per week. This activation ensures that nothing is blocking the flow of the flushing fluid and eliminates any chance of contamination from stagnant water. It’s important that all heads of the device are activated, including the eyewash or eye/face wash head, as well as the showerhead.
Take time to flush lines long enough to clear the line of sediment and debris. Self-contained units should also be visually inspected weekly. Inspection tags are often included with fixtures to document testing and to satisfy a safety audit.
Keeping a dated checklist for inspections helps follow-through and accountability. Training workers on the location and operation of fixtures also helps reinforce proper usage.
Employ Testing Devices, Dust Covers and Support
Manufacturers provide specially designed materials to assist in weekly testing, such as a heavy-duty drench shower tester designed with a water-tight funnel to minimize getting wet during testing. The funnel directs water to a drain or bucket and prevents water from splashing in the surrounding area. For testing eye wash fixtures, a transparent plastic compliance gauge features clear instructions on how to test the eye or eye/face wash system according to ANSI Z358.1-2014 testing protocols.
Sometimes false activations and bowl tampering can impede emergency fixtures’ reliability and performance. Facility managers can avoid false activation issues by installing an eyewash signaling system with a dual set of contacts. The first set of contacts activates the visual and audible indicators, while the second may be wired into a central monitoring system to alert a supervisor or maintenance personnel that the fixture has been tampered with.
To protect emergency eye/face wash bowls and keep the units cleaner, use models that incorporate durable dust covers made of sturdy plastic or stainless steel that shield the entire bowl. Dust covers protect the bowl from unwanted debris, shavings or tampering. The covers open as the fixture is activated, and may be installed on barrier-free fixtures.
Some product manufacturers offer complimentary safety shower and eyewash system site surveys to help facilities ensure their equipment is in good working order, compliant with the ANSI/ ISEA Z358.1 standard, and/or meet designated corporate goals or best safety practices. Be sure to conduct site surveys in the event of expanding, relocating or modifying onsite work processes.
Ensure All Fixtures Are Stationed Properly
Units should be stationed close to hazards, easily seen and accessed, and be in immediate good working order. Consider these guidelines, which reflect the ANSI/ISEA Z358.1-2014 standard:
- Fixtures must be within 10 seconds of a potential hazard or approximately 55 feet. Access to the fixture must not be obstructed.
- Equipment must be on the same level as the hazard. If there are doors between the hazard and the fixture, they must swing in the direction of travel. The door may not have a locking mechanism, which may prevent the person access to use the equipment during an emergency. *The height of the eyewash flow pattern should be between 33 and 53 inches, and measured from the floor to the water flow.
- If a potential chemical spill in an area can affect multiple workers, enough fixtures should be in place for all to access. The number of eyewashes or showers needed for each hazard is based on the number of workers in that area and the probability that more than one will be exposed at the same time.
- All equipment must be identified in a well-lit area with highly visible signage, e.g., bright yellow; it should be able to be activated in less than one second.
Double Check Water Capacity
It is essential for every potential hazard at a worksite to be supported by a plumbed or portable device that has access to an adequate water supply at an appropriate pressure and temperature. It’s important that the amount of water supplied to the unit can adequately support a full 15-minute flow of flushing fluid. Therefore, a minimum water pressure of 30 pounds per square inch (PSI) should be supplied to plumbed emergency drench showers and eyewashes. Typical facilities supply their fixtures with 45 PSI inlet supply pressure. Extra care should be taken with any pressure that exceeds 80 PSI.
The water supply must also satisfy the ANSI minimum flow rate, which is at least 20 gallons per minute (GPM) for drench showers, 0.4 GPM for eyewashes and 3.0 GPM for eye/face washes. Because different products have varying flow rates, it’s important to confirm flow rates with the equipment manufacturer.
Test ANSI-Required Tepid Water Temperature
Lukewarm (tepid) water is required for the full 15-minute flush, for a drench shower, eye wash or eye/face wash. The ANSI/ISEA Z358.1 standard indicates that the use of tepid water encourages affected users to continue to flush the entire 15 minutes. Tepid is defined as 60-degrees to 100-degrees Fahrenheit. Prolonged exposure to near freezing water has been proven to affect the body’s ability to maintain body temperature, increasing the risk of hypothermia. If the fluid delivered to the affected user is over 100-degrees Fahrenheit, it’s possible that the hot water could exacerbate a chemical interaction with the eyes and skin. Whenever possible, consult a physician to determine the recommended temperature based on specific types hazardous chemicals or material.
Understand Safety is a Work in Progress
The absence of weekly testing may jeopardize the outcome of using the equipment when someone is in grave need after coming into contact with a hazardous or corrosive material. A regular review of facility conditions, placement and performance of equipment will prepare your facility for short- and long-term safety and ensure compliance with the ANSI/ISEA Z358.1 standard.
1https://computer.howstuffworks.com/e-mail-messaging/how-emergency-notifications-work.htm
This article originally appeared in the January/February 2020 issue of Occupational Health & Safety.