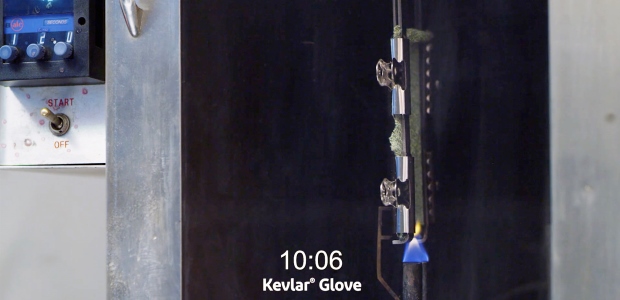
More Choices, More Challenges for Choosing Hand Protection
Choices in hand protection have grown significantly during the past 30 years.
- By Jill A. Clements
- Jun 01, 2019
How often do you think about your hands? Typically, our hands are an afterthought to our daily routines, especially when it comes to protecting them. But could you easily go about your daily tasks without the use or even limited use of your hands? Most of us could not, but more importantly, none of us want to find out.
According to the U.S. Bureau of Labor Statistics data for 2016, of all nonfatal occupational injuries and illnesses involving days away from work, 13 percent were for hand injuries. And 20 percent of disabling workplace injuries involve hands.
Taking a closer look at the data, we see nearly 70 percent of hand injuries occur because the worker was not wearing gloves. What does that mean for the other 30 percent? It may mean they were wearing the wrong gloves. As odd as it may seem, wearing the wrong gloves can be just as dangerous as wearing no gloves at all. Clearly, there is room for improvement when it comes to protecting workers' hands.
There are thousands of different styles and types of gloves and more than a handful of new and updated standards addressing hand protection. With all these choices and new and updated standards to review, it's no wonder many people find it difficult to choose the correct hand protection.
First, Understand All of the Potential Hazards
There are numerous things to consider when choosing hand protection. Questions such as "What cut level do you need?" "Do you need impact protection?" and "What happens to the gloves if they’re exposed to high heat or a short-duration fire?" are all a good place to start.
This is where a job task analysis can be critical. Thoroughly understanding the task that needs to be done and all hazards associated with that task are critical to choosing the correct hand protection.
A job task analysis should start with the worker or safety manager (preferably both) taking time to understand all of the possible hazards associated with the task. It is helpful to have a certified industrial hygienist brought in to assist with the analysis. Sometimes, it's beneficial to involve an employee who performs different tasks to gain perspective from someone who has not become complacent to the potential hazards of the task being evaluated.
Taking time to acknowledge all of the potential hazards and gain the information needed to make an informed decision about choosing the correct personal protective equipment, including hand protection, often can save a worker from a serious injury, or even potential death, and should always be a critical component of any safety culture.
Second, Understand the Different Standards
After determining the possible hazards associated with the task, the next step is to understand which standard or standards apply and which one you are referencing so that you can make an informed decision when choosing hand protection.
This can be a daunting task because existing standards are regularly being updated and new standards are being issued. It's an important, and often difficult, responsibility to stay informed about all the changes in standards. Consider the fact that within just the past year, two PPE standards have been updated with changes that affect glove testing and classification; and one new glove standard will be issued later this year. These are in addition to the major changes that the industry saw in 2016 when the ANSI/ISEA 105-2016 handbook was issued.
Consulting with an expert who can help you navigate new and updated standards can be invaluable.
Holding Gloves to the Same Standard: Changes to NFPA 2112
In 2018, NFPA 2112, Standard on Flame-Resistant Clothing for Protection of Industrial Personnel Against Short-Duration Thermal Exposures from Fire, was updated to also include items such as balaclavas, hoods, and gloves. Some think of NFPA 2112 as the "thermal manikin standard," but this standard contains many more test methods. In fact, gloves are not even covered under the thermal manikin test.
Gloves are covered under three other test methods:
- heat transfer performance test to determine how gloves would react to a combined convective and radiant heat source
- right-angle test to determine flame resistance of the material
- heat transfer test (oven test) to determine shrinkage in a hot air environment
One common theme among these three tests is the requirement that the material should "not melt and drip." After all, if a worker is wearing garments that are covered under these tests, shouldn't their gloves perform to the same level of protection? This seems so logical, yet it is not the case for many workers.
For example, at a recent outdoor safety fair for a major petrochemical company, all of the workers were wearing flame-resistant (FR) coveralls and while their gloves were cut resistant, they provided no FR protection. When these gloves were set on fire as part of a demonstration, they melted and dripped. This demonstration was an eye-opener for the attendees who quickly realized their hands were at risk of not only being burned, but having the glove melt and fuse to their skin.
What's more, non-FR gloves will melt after hot-surface contact, such as touching a pipe containing >100°C fluid.
Gloves Now Specified for Arc Flash Resistance in ASTM F2675
Updated in 2019, ASTM F2675, Standard Test Method for Determining Arc Ratings of Hand Protective Products Developed and Used for Electrical Arc Flash Protection, addresses testing gloves for resistance to an arc flash. This test should only be applied to gloves that are specifically designed to protect against an arc flash, which is not the same as a glove that has been designed for short-duration flash fires or for hot-surface contact protection. These three glove types should never be used interchangeably.
Prior to this change, the test was performed on fabric rather than the glove form. This is an important distinction because protection levels may be different when in glove form. To avoid any confusion, when you see "HRC rated 2 glove" on a package, be sure to check whether it also states "tested in glove form."
Testing Gloves for Impact Protection with Changes to ANSI/ISEA 138
The International Safety Equipment Association (ISEA) has issued a new standard in 2019 enabling workers to determine the impact protection of gloves (ANSI/ISEA 138, American national standard for performance and classification for impact resistant hand protection).
This new standard requires one of the three levels of impact protection defined in the standard be displayed directly on the glove and that manufacturers who want to reference the standard must have their gloves certified by a laboratory meeting the requirements of IEC 17025 for laboratory conformity assessment.
In addition to the knuckles, this new standard includes fingers as part of the testing requirements, which is a major distinction from the European standard for impact protection, which covers only the knuckles.
New Cut Protection Levels and More: ANSI/ISEA 105-2016
A little more than three years ago, the guidelines for hand protection were updated when the ANSI/ISEA 105-2016 handbook was issued. Several sections of the handbook were updated, but the section that received the most attention is the one that addresses the levels used to determine cut protection.
With this update, the industry went from having five levels to choose from to nine. When the update was issued, there were new levels for which gloves didn’t yet exist, but the industry has been quick to supply workers with choices up to level A9 now.
Hypodermic needle puncture protection versus stylus puncture protection is a critical distinction now offered in the handbook. Gloves that offer protection from a stylus (the tip of which is 1 mm in diameter) will not guarantee protection against a hypodermic needle (the standard uses a 25-gauge needle as the reference), and serious injury can result from wearing the wrong glove.
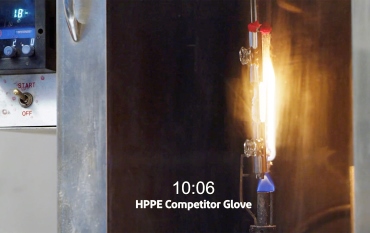
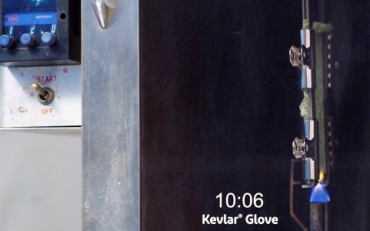
The vertical flame test shows a glove made of Kevlar not igniting or burning, while a glove made with HPPE ignites and continues to burn during a 12-second testing time.
Choose the Right Glove for the Job and the Hands
Choices in hand protection have grown significantly during the past 30 years. Having so many choices can make selecting the correct hand protection more challenging; however, it also has been a key component of improved worker safety by allowing safety managers to choose hand protection that properly fits their workers and meets the on-the-job hazards they face.
The keys to success when choosing hand protection include a safety culture that promotes frequent job task analyses, as well as a good understanding of which test method or standard applies to the hazard that has been identified. And remember, if you need assistance with navigating the plethora of hand protection standards, consult with an expert.
This article originally appeared in the June 2019 issue of Occupational Health & Safety.