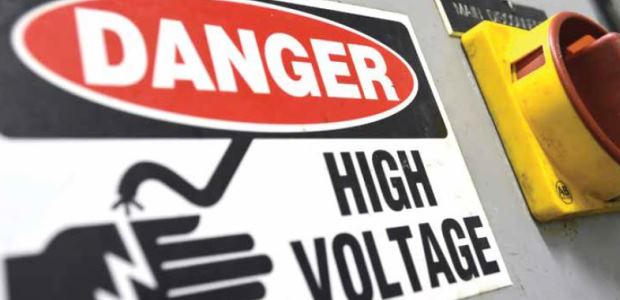
Incident Energy Analysis—One Way or Another
Having labels with warnings on them is just one piece of the pie when it comes to a robust electrical safety program.
Innovation in Arc Flash
Innovation in electrical safety? Yes, as old school as the electrical industry is, as far as power systems are concerned, arc flash is still one of the newer things. It may not be as fancy as the addition of the variable frequency drive, but we are talking about blasts of plasma, the fourth state of matter, and this plasma can be hotter than the surface of the sun. Even in incident energy analysis, which began its start decades ago, there is something new—which is the reverse-study table method. These are tables in the spirit of the NEC (National Electric Code), which is the goddess of shortcuts and common-sense applications, of which the backbone is plain, boring, tedious engineering.
Standards for Incident Energy Analysis
This article covers the options for performing arc flash incident energy analysis and labeling equipment for the arc flash hazard. The Institute of Electronics and Electrical Engineers (IEEE 1584) provides the equations for incident energy analysis, and the National Fire Protection Association (NFPA) has adopted the 2002 version of those equations into its own standard, NFPA 70E. OSHA (Occupational Safety and Health Administration) refers to NFPA 70E for its regulatory approach in the United States. In Canada, the sister standard to 70E, CSA Z462 (Canadian Standards Association), is referred to within its borders as the go-to standard for electrical safety and arc flash.
Cover All Your Bases
Let's cover all the steps involved with incident energy analysis and the time it takes to get it done. We’ll also discuss the pros and cons of each methodology from a safety standpoint, and why ESH managers and safety engineers should be open to promoting either way within their company. You must get it done one way or another.
First Steps for Incident Energy Analysis
What is the first step with incident energy analysis? With the reverse-study method, the first step is labeling. Yes, first you go and apply the labels using the reverse-study tables. To do that, you have to check a few things in the field at each location (such as upstream transformer kVA), and then you select and apply a pre-printed label using a table. Using the other method for incident energy analysis, the one where an engineering study is still required to be done, you do a walk-down and complete data collection. So these are your first steps. . . .
When you are completing either of the first two steps, you must send someone familiar with electrical code compliance. They must identify code violations and take note of them so they can be raised to management for resolution. The equipment must be marked as extra-hazardous and de-energized for hot work in all circumstances until the code violation is fixed, unless it is a matter unrelated to the arc flash hazard. Correcting code violations is often up to operations or maintenance managers, sometimes a safety professional, and occasionally an electrical engineer.
Second and Third Steps for Incident Energy Analysis
What is the second step with incident energy analysis? Well, labeling is already completed with the reverse-study method. If data were collected during labeling to produce a one-line, or update an old one, then this is the second step. In the case where you collected data for an engineering study, well, this costly and time-consuming step has to be done now. The engineering study will create a one-line from the engineering software. It also will create reports so you can do step three. One-lines can be of CAD quality with the reverse-study method, and the computer-generated software one-line could be, too.
Step three for the data collection/engineering study method is to go back into the field and apply the labels. Now, you're done with labeling compliance. However, employees need to have training and proper PPE so they know how to work safely; workers need oversight to successfully work around hazards. Having labels with warnings on them is just one piece of the pie when it comes to a robust electrical safety program.
Mitigation of High Arc Flash Hazards
What about mitigation of high arc flash hazards identified and coordination of protective devices? With the reverse-study method, high arc flash hazards should be noted on ESWP forms (electrical safety work process forms) or some other kind of form. An ESWP form can note the code violations mentioned before and note high-level PPE warnings applied with the tables. An engineer can look at the form and determine whether a localized coordination study is needed to lower a setting and reduce the risk. Most all devices on site are fixed fuses or breakers; by looking in the NEC, one can determine whether a fixed trip breaker can be sized to a lower size.
With the other method (data collection/engineering study) these things are picked up when the arc flash study is completed and recommendations are made to management in a report to correct these issues and apply labels later when the recommendations are implemented. Either way, the fixes mostly include retrofitting fixed trip breakers and fuses with new ones, and lowering settings on large power breakers.
Good Arc Flash Labels
With either method, a good label should include incident energy at a working distance, information about PPE requirements, voltage, a warning sign saying "arc flash hazard," and a flash protection boundary. Shock protection boundaries and the "shock hazard" warning sign also may be included.
Cost and Time Savings
A reverse-study means savings on cost and time. It doesn't take as much time to just go and apply labels in one step. The potential is for compliance to increase when cost and time are reduced. If you determine to take on the arc flash hazard where you work, or go through the five-year redo process per NFPA 70E, you might just want to be done and compliant sooner than later, especially if you have a lot of scope. With the reverse-tables, the idea behind the table method is to apply labels only once and then as needed for new installations and retrofits.
Disadvantage of Reverse-Study Arc Flash Tables
There is one disadvantage to the tables—in a few spots, it can be conservative, but it shouldn't be by much. The engineering study behind those reverse tables should dial down the incident energy in good alignment and if it doesn't, the product is not sound. Secondarily, if your system has operational problems and you’re losing money or safety confidence because of it, then you need more than a localized coordination where arc flash is high. In reality, you might need several software studies for your plant, including site-wide protective device coordination, harmonics, short circuit, load flow, voltage drop, and/or load shedding studies. But for the arc flash hazard, your diagnosis likely requires labeling via either method and electrical worker arc flash hazard training and proper PPE.
Closing
This article is just one aspect of the continual training we all go through to be safe. Be safe and be innovative!
This article originally appeared in the September 2018 issue of Occupational Health & Safety.