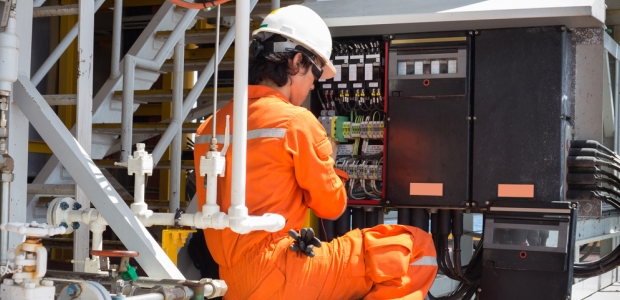
Workplace Electrical Safety and Organizational Context
Good safety practice requires that workers take responsibility for their own safety and that of their co-workers. But it's also important that organizations empower them to do so.
- By Richard Campbell
- Jun 01, 2018
When it comes to workplace injury, prevention is invariably the best medicine—for workers and employers alike. This maxim is particularly true when it comes to electrical injuries, which oftentimes involve severe physical wounds, emotional trauma (for victims as well as co-workers and family members), difficult rehabilitation, and expensive medical treatment.1,2 Unfortunately, while electrical injuries are generally on the decline, they are not rare events. On average, there are more than 2,000 non-fatal electrical injuries at work each year, as reported by the U.S. Bureau of Labor Statistics (BLS).3,4 Although not all of these injuries are serious, a substantial portion of them are; BLS data also indicates that more than 1,700 workers suffered fatal electrical injuries in the ten-year period from 2006 through 2015.4
Protecting workers from electrical injury has been the essential mission of NFPA 70E, Standard for Electrical Safety in the Workplace,5 since the mid-1970s, when it was first developed at the request of the Occupational Safety and Health Administration (OSHA). Electrical safety procedures involve a range of best practices to protect workers exposed to electrical hazards, including requirements around safety training, shutting off power prior to working on equipment, use of personal protective equipment, and many other preventive measures.6 But the extent to which those safety precautions are implemented in the workaday world of real life is another matter, and one that falls outside the control of technical requirements alone.
Research into workplace electrical injury clearly indicates that workers often perform work on equipment or circuits that are energized, are not always equipped with appropriate personal protection equipment, and oftentimes haven’t received the right training for the work they perform.7-9 There are multiple reasons for these failings in electrical safety—workers may be in a hurry to complete a job, or fail to recognize an unmarked hazard, or not have the right protective gear on hand to undertake the task at hand. It is accordingly important not just to gain a better understanding of how workers are getting injured, but also to make some effort to identify the "causes of the causes" of electrical injury and to highlight barriers to improved compliance with the best electrical safety practices that are already on the books.
To this end, organizational safety culture is gaining recognition as a crucial factor that shapes the extent to which safety considerations are incorporated into the performance of day-to-day work tasks. Safety culture is broadly defined as the "deeply held but often unspoken safety-related beliefs, attitudes, and values that interact with an organization’s systems, practices, people, and leadership to establish norms about how things are done in an organization."10 Without a strong and visible organizational commitment to safety, workers will arguably be more attentive to recognition and reward systems that emphasize tangible contributions to productivity than to the critical requirements of electrical safety procedure.
Sending Mixed Messages to Workers
We recently completed research that offers some indication of how extraneous considerations might influence task-specific electrical safety practices.4 As part of the research, we examined a number of OSHA investigation reports of workplace arc flash and electric shock injury events. It was evident in some of these incidents that electrical safety requirements were in subtle (or not so subtle) competition with pressures to get the work done.
Consider the role of mixed messages in communicating priorities to workers. In one of the investigations we reviewed, a managing partner of an electrical services company was electrocuted while working late at night on a lighting unit that had been left energized in order to save time and complete a job by the next day. While the decision to work live raises a host of issues relating to safety culture—including the unlikely prospect that subordinate members of a work crew would suggest to their supervisor that it would be better to turn the power off—it was in a company meeting after the fatality that the role of conflicting safety messages was most apparent. The meeting was called in order to talk about the fatality and discuss the remaining projects on the calendar in light of new circumstances. Meeting notes indicated that workers were reminded of the need to take appropriate safety precautions and not to work live—but were promptly reminded in the very next agenda item that forthcoming holiday bonuses were contingent upon how well the company managed to meet existing production schedules.
In another incident, a machinery repairman, one with apparently limited electrical safety training, was electrocuted while troubleshooting an air conditioner. The worker touched a live wire with a finger on his left hand, and a current passed through his left arm and heart, then exited through his right arm. His employer had failed to provide him with either appropriate personal protective equipment for energized work or insulated tools, and the company's health and safety program consisted of two pages of general guidelines culled from state OSHA construction standards. It's hard not to read about a tragedy like this and wonder whether the worker knew about the risks he was taking in working live, or whether he knew the employer had an obligation to provide him with appropriate tools and personal protective equipment—and also whether he would have felt too vulnerable to even ask for them if he was aware of that requirement.
Ensuring Organizational Support
These examples are from small companies, but research into electrical injuries shows that production pressures often lead to cutting corners in safety practice, whether that involves failing to verify all potential sources of energy in pre-job planning, leaving equipment energized in order to save time or avoid inconveniencing building owners, working without personal protective equipment or electrically safe tools because they're back in the truck, or some other among a myriad of possible reasons.6-8 Management may counsel workers to practice safety, but supervisors who are accountable for meeting production benchmarks may let expedience trump time-consuming safety controls if productivity is what gets rewarded.8
Similar factors may influence what happens when employees are assigned tasks that expose them to hazards for which they haven't received adequate safety training, another common ingredient in workplace electrical injuries. Beyond the possibility that workers who lack appropriate training may not even be equipped to recognize when they are in hazardous situations—an issue in itself—the prospect that a worker will turn down a novel job assignment must be understood from the vantage point of the worker, who has an obvious interest in demonstrating a commitment to meeting company needs.
Good safety practice requires that workers take responsibility for their own safety and that of their co-workers. But it's also important that organizations empower them to do so and ensure that enough time is allowed for work to be done properly, that workers have the requisite training and experience for the hazards they will face, that every effort is made to ensure that work is performed de-energized, and that work is performed with appropriate personal protective equipment. The organizational components of good workplace health and safety practice go above and beyond technical safety requirements. Workers not only need to be knowledgeable about proper electrical safety procedures, but also need to be confident of organizational support in following them in practice.
References
1. Arnoldo BD, Purdue GF, Kowalske K, Helm PA, Burris A, Hunt JL (2004). Electrical Injuries: A 20-Year Review. Journal of Burn Care Rehabilitation 25:479-484.
2. Noble J, Gomez M, Fish JS (2006). Quality of Life and Return to Work Following Electrical Burns. Burns 32:159-64.
3. Cawley JC (2011). Occupational Electrical Accidents in the U.S., 2003-2009. ESFI White Paper. Available at: http://www.esfi.org/index.cfm?pid=11406&view=list&sb=date&st=desc&m=0&y=0&type1=0&type2=20&change=View. Accessed Nov. 8, 2014.
4. Campbell R, Dini D (2015). Occupational Injuries from Electrical Shock and Arc Flash Events. The Fire Protection Research Foundation, Quincy, MA. Available at: http://www.nfpa.org/research/fire-protection-research-foundation/projects-reports-and-proceedings/electrical-safety/other/occupational-injuries-from-electrical-shock-and-arc-flash-events
5. http://www.nfpa.org/codes-and-standards/all-codes-and-standards/list-of-codes-and-standards/detail?code=70E
6. National Fire Protection Association (2014). NFPA 70E: Standard for Electrical Safety in the Workplace, 2015 Edition. Quincy, MA: National Fire Protection Association.
7. McMann M, Hunting KL, Murawski J, Chowdhury R, Welch L (2003). Causes of Electrical Deaths and Injuries among Construction Workers. American Journal of Industrial Medicine 43:398-406.
8. National Institute for Occupational Safety and Health (1998). Worker Deaths by Electrocution: A Summary of NIOSH Surveillance and Investigative Findings. Cincinnati, OH: NIOSH Report No. 98-131.
9. Kowalski-Trakofler K, Barrett E (2007). Reducing Non-Contact Electric Arc Injuries: An Investigation of Behavioral and Organizational Issues. Journal of Safety Research 38:597-608.
10. Gillen M, Goldenhar LM, Hecker S, Schneider S (2013). Safety Culture and Climate in Construction: Bridging the Gap Between Research and Practice. Proceedings from CPWR sponsored Safety Culture/Climate Workshop, Washington, D.C., June 11-12, 2013. Available at: http://www.cpwr.com/sites/default/files/CPWR_Safety_Culture_Final_Report%20with%20links.pdf. Accessed Oct. 21, 2014.
This article originally appeared in the June 2018 issue of Occupational Health & Safety.