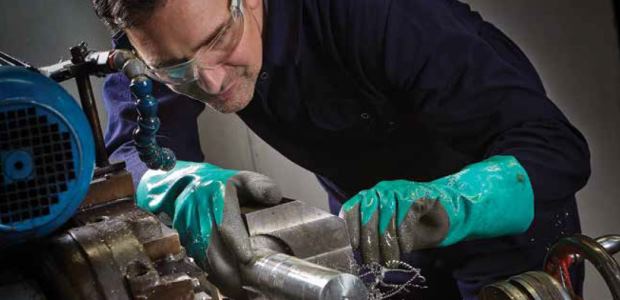
Chemical Growth Fuels Innovations in Hybrid Cut and Chemical PPE
Workers are speaking loud and clear—with increased cut risks abundant in today’s machinery-heavy workspaces, cut protection can be as critical a factor as chemical protection.
- By Steve Genzer
- Apr 01, 2018
The chemical industry is currently in the midst of expansive growth. According to the American Chemistry Council, as many of the world’s major economies experience an upturn, the chemical industry stands poised to prosper, with U.S. chemistry production volume expected to increase by 3.7 percent in 2018. This momentum and expansion translates into a powerful workforce; the chemical industry alone employs 811,000 people in the United States, and for every one job created from the business of chemistry, 6.8 jobs are created in other sectors.1 Talk about a true chemical reaction.
As with any growth comes evolution, and the chemical industry is no exception. To meet growing industry demands for innovations and efficiencies, automated machinery and technology are becoming more common in the workplace than ever before. With workspaces outfitted with advanced technologies and businesses challenged to forge paths of accelerated growth, the need to multitask and quickly change from a chemical setting to a mechanical setting is the new norm. Workers are being challenged to move more quickly and efficiently from task to task for better productivity and performance.
As chemical work becomes increasingly more complex, so does outfitting workers with proper personal protective equipment (PPE). Chemical workers regularly dealing with automated machinery or advanced equipment are routinely exposed to cut hazards in chemical applications, putting themselves at an increased risk of injury, poor comfort, and loss of productivity.
So a new challenge arises for safety managers and workers alike: finding safety solutions that provide comfort and performance without compromising chemical or cut protection. Thanks to innovations in PPE, such options exist, but they do so in a sea of gloves that settle for cut or chemical protection at the expense of grip, comfort, or dexterity. Safety managers must wade through a wide array of cut and chemical safety products to find the right balance of protection.
Understanding Existing Worker Needs
Let's take a step back—what are chemical workers looking for when it comes to hand protection?
With more than 60 million chemicals registered in the Chemical Abstract Service registry, finding the right chemical protective glove is not an easy task. Many different chemicals and chemical mixes are used in a typical product process or production facility, and every unique set of chemicals requires specific safety precautions. To match the expansive set of chemicals that can be present in any given work space, chemical-resistant gloves come in a wide variety of barrier materials, thickness, and designs.
However, the glove game becomes even more complicated when cut risks come in the mix. Not only does the glove need to protect against permeation breakthroughs of chemicals, its fabrication also must stand up to cuts and abrasion to ensure workers are protected against other possible risks.
According to the current chemical workforce, this is where current gloves aren’t standing up to the task at hand. A 2017 Ansell market research shows 86 percent of chemical glove wearers indicated they would like cut protection in their current chemical gloves, and cut protection was the number one desired improvement to the design of chemical gloves. Workers are speaking loud and clear—with increased cut risks abundant in today's machinery-heavy work spaces, cut protection can be as critical a factor as chemical protection.
Breaking Bad Habits
Identifying worker PPE needs is the first step; breaking bad habits is the next hurdle when it comes to protecting against both chemicals and cuts. Faced with inadequate protection, workers have developed inefficient and dangerous work-arounds to fit their glove needs or get the job done.
Without multipurpose gloves that protect against all possible risks, some workers don gloves that offer only chemical or cut protection—not both, leaving them only partially protected. Those who choose to wear mechanical gloves only are at a risk of exposure to hazardous chemicals if the glove barrier is compromised. Those who choose to only wear chemical gloves run the risk of harmful lacerations if the barrier material can’t stand up to sharp objects.
Others choose to double up on protection, either wearing a mechanical glove under a chemical glove or a disposable glove under a mechanical glove in an attempt to achieve both chemical and cut protection. Unfortunately, the process of double gloving to achieve additional protection comes at a cost: comfort and performance. Two gloves can prove uncomfortable and stiff, while also decreasing the dexterity and tactility needed to complete daily tasks.
Finally—and perhaps the worst scenario—some workers choose to remove their gloves altogether, opting for the grip and comfort a bare hand provides while putting themselves at a massive safety risk. Any safety advocate can see we simply can’t stand to make the compromise between safety and performance any longer.
Compliance Over Compromise: PPE That Protects Against Cuts and Chemicals
Innovations in PPE are finally bridging the gap between chemical and cut protection, offering workers an all-encompassing safety solution. Advancements in nitrile, yarns, and fabrics allow for gloves that protect workers from many frequently used chemicals while still providing long-lasting snag, puncture, and abrasion resistance. Cut-resistant technologies and materials provide lightweight liners that can be added to chemical gloves, providing exceptional levels of cut protection in a chemical glove without losing comfort or ease of donning and doffing.
Advancements in glove designs are also keeping worker safety and health top of mind. New hi-viz liners can act as an indicator when the outer coating is cut or compromised, prompting workers to replace their gloves before any harm is done. Optimized fit techniques mold cut liners to nitrile shells for a second-skin feel and increased worker comfort leads to better PPE compliance.
Chemical workers are continually faced with greater demands and challenges that come with larger safety risks. It's time for PPE to match the industry's accelerated growth to ensure workers feel equipped to handle their unique set of tasks at hand.
Reference
1. https://www.americanchemistry.com/Media/PressReleasesTranscripts/ACC-news-releases/Outlook-US-Manufacturing-Turns-Corner.html
This article originally appeared in the April 2018 issue of Occupational Health & Safety.