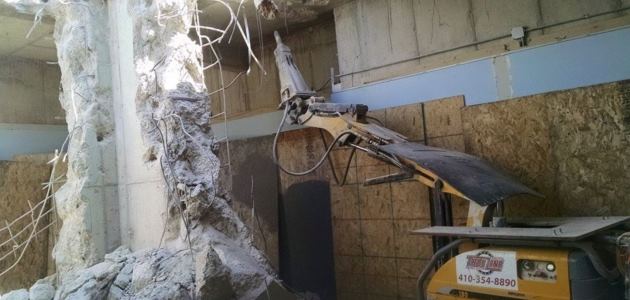
Innovating for a Safer Workforce
Companies can address an aging construction industry with sophisticated technology.
- By Peter Bigwood
- Jul 01, 2017
Much of the incoming millennial workforce doesn’t want to take the time to brew a cup of coffee when they could just use a coffee pod. Where before they would need to hail a cab, they now press a button on their phone and a car comes directly to them. And why go to a restaurant when food can be ordered by just sending a pizza symbol on Twitter? This tech-savvy generation craves efficient tools to achieve the fastest results in whatever they do. While some of it may seem lazy and self-serving, it's a theme that has hard-work industries, such as construction, foundries, and mining, changing their ways.
At the same time, the existing workforce is aging. Nearly half of all workers will be 55 or older by 2018, reports the U.S. Bureau of Labor Statistics. Construction industry jobs are expected to grow by 19 percent between 2008 and 2018. That combination drives a pressing need to recruit more young workers to fill the gaps left by retirees. Add in the increasing burden of workers’ compensation claims due to workplace injuries, and employers are scrambling to find ways to cope. Not surprisingly, technology may point to a better way.
A History of Accidents
Safety is the first issue to address. Manual labor in construction, demolition, foundries, and mines has long included pneumatic tools, such as rivet busters and paving breakers, with heavy vibrations that can lead to injuries such as carpal tunnel syndrome, nerve damage, and hand-arm vibration syndrome, after prolonged use. Workers are also constantly at risk of falls, falling debris, and toxic air. The Occupational Safety & Health Administration reported 874 construction workers were killed in 2014—20.5 percent of all private-industry deaths. The leading causes were falls, followed by electrocution, being struck by an object, and being caught in or between objects. In the meantime, there were 201,000 cases of work-related injuries and illnesses in construction, 10,300 in foundries, and 6,500 in mining, not including oil and gas. Of all those, about 80,000 resulted in days away from work.
While experienced workers suffer less frequent injuries than their younger counterparts, the Epidemiologic Reviews reports they're more severe and costly and require more time away from work. An American Journal of Industrial Medicine study followed, showing that expense claims for those 65 and older were about triple those of their 18- to 24-year-old co-workers. The high price tag is largely due to lost wages paid to workers for days away from work, disabilities, and physical limitations. In addition, employers incur extra costs when hiring and training new workers to replace injured or retiring employees.
Technology for Safety and Productivity
The risk of many of these injuries could be reduced if the worker had a way to do the work while avoiding hazards. That's why contractors, foundries, and mining operations are turning to remote-controlled equipment. The machines allow workers to operate them and monitor their work from a safe distance in applications such as crushing concrete on demolition sites, tearing out refractory in a foundry, breaking rock in mining, and excavating in tunneling. This keeps operators away from hazards and improves productivity by virtually eliminating physical strain and fatigue. Many remote-controlled demolition machines are electric powered, able to run with zero emissions in confined spaces.
These features reduce a number of costs for contractors. Carl Jones, vice president of the Coring & Cutting Group, a collective of concrete sawing, drilling, and breaking contractors with 25 locations across 12 states, said they've used remote-controlled saws and remote-controlled demolition machines for precision demolition for about 15 years. He said they reduced injuries and improved profits by making the switch. A combination of factors—including the new equipment, a drop in surgery costs, and more competitive insurance markets—lowered annual demolition workers' compensation claims by about 50 percent. The group of companies also saves about $40,000 to $50,000 a year, or around 25 percent, in injury costs since the switch.
Jones said the most common claims had been lower back strains. The heavy and repetitive lifting that caused the strains was replaced with a lightweight remote control box to operate the robotic equipment. In addition, the group reduced diamond blade costs by limiting diamond saw use to scoring concrete before breaking it with the machines. Before the new equipment, Coring & Cutting Group tried to cut back on wear on their employees by focusing on cutting and not breaking. The safety and lack of physical strain from remote-controlled demolition machines allowed the group to add breaking back in, reducing the amount of diamond blades they needed to use for cutting.
Another concrete contractor, Mike Iiams, owner of Precision Cutting & Coring in Kansas City, Kansas, has seen much of the same. He bought the first of his company’s three remote-controlled demolition machines six years ago and estimates they’ve helped him reduce pneumatic tool use by 60 to 70 percent.
He said the improved safety offered by the new machines has also helped reduce the company's workers' compensation claims, as well as its experience modification rate, or EMR, every year. Insurance companies calculate the EMR by looking at a company’s safety record and using it to gauge future chances of risk. The higher the EMR, the costlier the insurance premiums.
In addition, Iiams said, profits have increased and productivity on the job is at least 50 percent higher than it was before he bought the remote-controlled equipment. The high-tech tools also reduce diamond blade costs and increase wall saw lifespans by reducing the amount of cutting needed. Iiams said Precision Cutting & Coring completes 20 percent of its work with the machines, and it’s work they either would have done another way or couldn’t have done without the equipment.
Drawing a Younger, Savvier, Crowd
In addition to improving safety, this new technology is pivotal to enticing a younger workforce. The new generations have been raised on advanced technology and have a strong desire to avoid manual labor. Cutting-edge robotics that appeal to the sense of technology and reduce or nearly eliminate manual labor will be much more successful in attracting younger workers. The Coring & Cutting Group used robotic demolition and sawing equipment to adapt their group of 25 companies to millennials and, as a result, the average age of their team of about 300 workers is just 25 years old. The group cut their turnover rate from 33 percent before the new equipment to 23 percent today. Productivity, including the speed with which the group completes jobs and the amount of new work coming in, increased 17 percent over the past three years. Carl Jones said they keep the young workers excited and eager to work by holding regular training sessions and spending money on new technology. Jones said the group made the choice to invest in the machines after realizing insurance costs were getting too high and that it would be difficult to attract new employees to eventually replace their older crew if they continued their traditional approaches to strenuous work.
Iiams explained turnover is low for him as well, and about half of his 45 employees are 25 or younger. The contractor said his younger workers are drawn to the high-tech equipment and are naturals at using it, while his older workers generally prefer not to run the units. But, as a result of using the machines for a portion of the project, the workers don’t need to use handheld tools, and experience the associated wear, as often. He also noted that the robotic equipment helps extend the careers of his older workers as they can limit the more physically demanding aspects of their work. The result is that the company benefits from keeping experienced workers around longer.
Solutions from Unique Tech
The new, fresh-faced workers are demanding safe and efficient methods instead of unnecessary hard labor in their daily tasks. By choosing new technology, such as remote-controlled demolition machines as well as cutting equipment, contractors, foundries, and operations in other tough industries can reduce workplace injuries and workers' compensation claims. They can then use the ROI to pay for the new equipment. Iiams estimated that, with the savings in injury, EMR, and diamond blade costs along with the increase in productivity, it took about one year for him to pay off his smallest demolition robot, and two years for his medium-sized unit. In addition, the investment can improve morale, lower turnover rates, and attract a young generation of workers eager to learn to do their work in a unique, new way.
This article originally appeared in the July 2017 issue of Occupational Health & Safety.