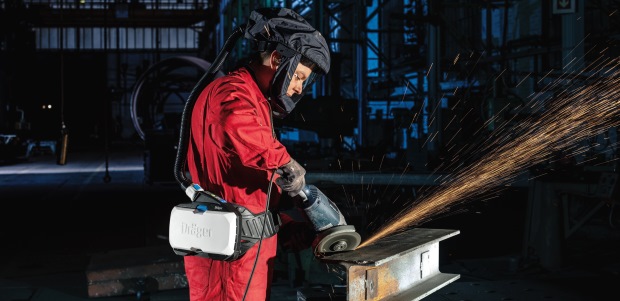
Harnessing the Powered Air Purifying Respirator
Differentiating between contaminants that are gaseous or dust can be crucial in ensuring your PAPR is the proper PAPR.
- By Paula Varsamis
- Nov 01, 2016
Workers' safety goes deeper and depends on more than simply donning their devices. Regardless of a company's industry of operation (food & beverage, water treatment, construction, etc.), equipping decision-makers and end users with the knowledge of the available safety solutions based on their workplace environment helps ensure they're choosing the proper device that matches, if not exceeds, the necessitated level of safety. In many instances, a powered air purifying respirator, otherwise known as a PAPR, can greatly improve its wearer’s safety, but it’s critical that it fits the workplace environment just as much as it fits its wearer.
Why Should I Consider Using a PAPR?
Elimination of Breathing Resistance
PAPRs differentiate themselves from negative pressure respirators through their motor blowers. Motor blowers draw air through a filter and into the wearer’s breathing zone, helping to reduce barriers to breathing, and also can provide a cooling sensation due to the mechanical movement of air. Not only does this reduce the overall burden on the wearer's body, but also it expands which type of wearer can don the device. For example, those who are not medically cleared to use negative pressure respirators can begin to view PAPRs as a viable option because there is less strain on the wearer. However, it's important to note that many employers require all potential PAPR wearers to undergo a medical evaluation to determine whether or not they can safely wear the proposed respirator.
More Flexibility in Regulatory Requirements
In the United States, OSHA respirator regulations prohibit any facial hair from coming between the respirator sealing surface and the wearer's face.1 They also require wearers to be fit tested each year to ensure the respirator can operate at its fullest potential.2 In order to return time on tools to the workers and maximize safety, PAPRs offer loose-fitting hoods and head covers that can accommodate limited facial hair. As long as they don't come between the headgears' seal, loose-fitting hoods and head covers would not need to undergo any fit testing requirements under OSHA standards.3 Not only does it allow for flexibility in requirements, but it can also reduce overall maintenance costs in the long run.
Improved Assigned Protection Factors (APF)
In accordance with OSHA's Respiratory Protection standard's paragraphs (d)(3)(i)(A) and (d)(3)(i)(B), the Assigned Protection Factor (APF) of PAPRs varies, extending their practical application. For example, PAPRs with tight-fitting face pieces APFs of 1,000 are ideal safety solutions for workplace environments with higher concentrations in chemical substances, such as a water treatment plant, while half-face pieces with APFs of 10 and full-face piece respirators with APFs of 50 may be better suited for the food & beverage industry, where lower chemical substance concentrations are more common.
It's important to be aware of the fact that full-face negative pressure respirators are only guaranteed 50 APF if they offer a quantitative fit—without a quantitative fit, it will not meet OSHA standards and cannot be worn in environments with contaminant concentrations greater than 10x the exposure limits, or 10 APF.4 Tight-fitting PAPRs not only offer significantly higher APF, but they use a less expensive qualitative fit test to achieve a higher level of efficiency for a lower cost.5
Respiratory Protection Standard 1910.134
1910.134(d)(3)(i)(A)
Assigned Protection Factors (APFs)
Employers must use the assigned protection factors listed in Table 1 to select a respirator that meets or exceeds the required level of employee protection. When using a combination respirator (e.g., airline respirators with an air-purifying filter), employers must ensure that the assigned protection factor is appropriate to the mode of operation in which the respirator is being used.
1910.134(d)(3)(i)(B)(1)
The employer must select a respirator for employee use that maintains the employee’s exposure to the hazardous substance, when measured outside the respirator, at or below the MUC.
How Do I Maximize a PAPR's Value?
Identify On-Site Risks and Workplace Hazards with a Risk Assessment
Risk assessments lay the basic groundwork for choosing the proper PAPR. Most PAPRs can filter out particulates, gases, and vapors; however, some are specialized for particulates only.6 Thus, it is critical to identify any potential risks in the environment.
Engage a trained professional who is qualified to carry out the tests and understands the testing equipment to perform this activity. Criteria in an assessment may include, but are not limited to, these:
- Oxygen levels in the workplace or sections of the workplace: Oxygen levels must be greater than 19.5 percent in all spaces, whether they're open or confined.7
- Any airborne contaminants present or potentially present: Risk assessments must account for any hazards in the air or hazards that may arise due to work site processes. For example, sodium hypochlorite is used for disinfection in the water treatment industry and is corrosive to the respiratory tract. Not only this, but if PAPR motors that are electronically powered by battery packs are used in a work site that has flammable or explosive hazards in the air, the combination could pose a dangerous threat to wearers.8
- Physical state of contaminants: Differentiating between contaminants that are gaseous or dust can be crucial in ensuring your PAPR is the proper PAPR. As stated previously, some PAPRs can only filter out particulates, while others can filter gases, vapors, and particulates.
- Concentration of contaminant: Contaminants can be dangerous at various levels of concentration, but it's important to know whether or not the concentration is within the capacity of the respirator. For example, most PAPRs' requirements for contaminants is to have a concentration that is less than IDLH (Immediately Dangerous to Life or Health) or less than the MUC (Maximum Use Concentration).
- Duration of exposure: Most PAPRs have a duration of only four hours or eight hours, so it's important to know exactly how long workers will be exposed to any harmful substances.
- Warning signs: Do the contaminants have distinct smells? Are there specific symptoms that are identifiable in workers if they have been exposed?
Understand your PAPR
PAPRs come in all different kinds of configurations, but it's important to know which configuration works best for the wearer. Should you use loose-fitting head covers or tight-fitting hoods? Have all wearers had fittings to ensure there’s an effective seal? Does the PAPR need to have chemical splash protection or ANSI Z89.1 head protection? Although workplace risk assessments greatly contribute to choosing the correct PAPR, it's also important to focus on the wearers themselves—after all, PAPRs are working hard to make their lives easier.
The features (and limitations) of the PAPR should be taken into account alongside the conditions wearers have to endure in order to ensure that the respirator can improve said conditions. For example, an electronically powered four-hour PAPR should not be used in an area with flammable gases for an eight-hour workday. Additionally, when choosing a PAPR, consider if workers are physically capable of donning the safety devices and doing so does not be impose any extra strain. For example, workers with serious asthma or lung conditions that could impede the benefits of respirator wear should be medically checked and cleared for use of the device. By understanding the ins and outs of each PAPR and the worker, you can properly pair the device to its wearer.
Conduct the Proper Training
Prior to using the respirators, wearers must endure training sessions that ensure they're using the PAPR to its fullest potential. According to OSHA, training sessions must cover the following topics:9
- Why is the respirator necessary?
- Limitations of the respirator
- Capabilities of the respirator
- Outcomes of risk assessment
- How to inspect, don, and doff the respirator
- Fit tests
- User seal checks
- Cleaning, maintaining, and storing respirators
- How to recognize medical signs or symptoms that prevent the use of a respirator
Whether you're testing drugs in the pharmaceutical industry or welding in the automotive industry, it's crucial to know how you can keep your workers, your colleagues, and yourself safe. By learning the hazards present in the workplace environment and the ins and outs of safety devices, wearers can be equipped with the right respirators that not only increase their productivity, but, most importantly, keep their bodies healthy and happy.
References
1. https://www.osha.gov/pls/oshaweb/owadisp.show_document?p_table=INTERPRETATIONS&p_id=28997
2. https://www.osha.gov/video/respiratory_protection/fittesting_transcript.html
3. Ibid.
4. http://www.med.navy.mil/sites/nmcphc/Documents/industrial-hygiene/RESPIRATOR-FIT-TESTING.pdf#page=4
5. http://www.med.navy.mil/sites/nmcphc/Documents/industrial-hygiene/RESPIRATOR-FIT-TESTING.pdf
6. https://www.osha.gov/video/respiratory_protection/resptypes_transcript.html
7. http://www.atsdr.cdc.gov/mhmi/mhmi-v2-b.pdf#page=3
8. http://www.ilo.org/wcmsp5/groups/public/---ed_protect/---protrav/---safework/documents/publication/wcms_190172.pdf#page=2
9. https://www.osha.gov/video/respiratory_protection/training_transcript.html
This article originally appeared in the November 2016 issue of Occupational Health & Safety.