Measuring Safety Excellence: A Practical Framework
What one measurement would provide the greatest insight and facilitate performance and cultural transformation?
Hearing the scores before watching Olympic competitions provides an interesting perspective. Being in the United States at the time of the London 2012 Olympics, the results are known hours before the events are broadcasted. Viewers know who won prior to watching their performance. This vantage point moves the viewer beyond results to understanding what performance contributed to it. We must think the same way with our safety measurement systems.
In last month's column, "Zero Incident Goals Motivate Risk-Taking, Not Excellence," I urged readers to evolve beyond zero-based goals and initiatives. This doesn’t mean setting your goal as beyond zero, because that is too vague. Let me be clear: Of course zero incidents and injuries should be a goal in safety. It just should not be the goal. Once you achieve zero incidents or injuries, your measurements no longer provide insight as to how to get better. The purpose of this article is to provide a framework to measure safety excellence that is not only practical but internally implementable, as well.
Injury data measurements will move from prescriptive to descriptive to pointless and, eventually, demotivating and misdirecting. Excellence is achieved when successful performance is continuously repeated, unprompted, producing predictable positive results. How predictable are your results based on your measurement systems? If you achieve success, do your measurements tell you why, or even the difference in luck or purposeful intent?
Of course we want no injuries, but remember, this is a negatively defined goal that motivates failing less. What do you want to achieve? What do you want to exist that currently does not, or at least not consistently today? Like watching an Olympic event after knowing the winner, what performance would you observe that would give you a sense of confidence that great results should be expected? To get started, gather a representation of the culture and collaboratively answer these questions:
1. What does safety excellence mean? Clarity and alignment of this question first cannot be stressed enough. If you ask 10 different people in your organization for this definition, you will receive 15 different answers. Create a definition most believe in. If some do not share your goal, how can you influence their beliefs?
2. What would excellence look like?
3. What performance would you see from executives, managers, supervisors, employees, and contractors if you had reached your definition of safety excellence?
4. How will you measure or gather insight into whether these individuals' performance is aligned with your vision or definition of safety excellence?
5. What activities or initiatives need to be deployed to create competency or structure for the desired performance to exist?
6. How will you measure the impact these activities and new performance have on results?
It is important to first know where you are and have a clear understanding of the destination prior to identifying initiatives to close the gap. Once these have been clearly outlined, a customizable framework is necessary to begin measuring. Figure 1 outlines a customizable methodology to capture a better understanding of progress and consistency of expectations. Each category has proven crucial to better understanding the correlation among activity, performance, and results, as well as progress.
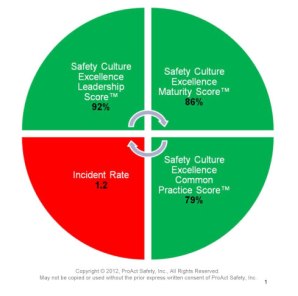
Figure 1. Client Sample Transformational Safety Performance Scorecard™
Safety Culture Excellence Leadership Score™
What are leaders at all levels effectively doing to lead safety as a core value and progress toward excellence? While there are many things that can be identified in this category, it is important to distinguish the difference in activities and transformational performance. Certainly activities such as the number of action plans, audits, inspections, observations, and percent trained are important, but do not get stuck in the easy trap of measuring just the things leaders are doing. While these may be leading indicators, by themselves they do not demonstrate progress or transformation. If you identify five primary things you desire to observe a leader doing or saying, how consistently is this occurring? How many leaders are in alignment with your desired definition of what a great leader looks like? How is this maturing your culture?
Safety Culture Excellence Maturity Score™
Our research and experience has indicated nine elements of excellence in culture and performance. Using a comparison to best practices is one approach. Another is to determine internally the vision of what a mature safety culture would look like at your location.
Safety Culture Excellence Common Practice Score™
Common sense isn't always common practice. If we know what we are directing, influencing, or asking people to do, are they doing it? How often and how effective are they? Are they performing one way in the presence of others and another when no one is looking?
Incident Rate, Frequency, Cost
This is your qualifier, and these are your lagging indicator results. If we are working our plan and the plan isn’t producing initial or sustainable improvement in the results, we need to modify and evolve our plan. We will always be held accountable for the results, but are we influencing and holding individuals accountable for proactive performance?
Remember, the purpose of this article is to provide a framework, not a prescribed approach. You will need to do much of this internally to create the ownership and motivation that the measurements are intended to generate. Once your framework has been established, continue to question the status quo. While there are a vast amount of potential leading measurement opportunities in safety, keep your focus on transformation. What one measurement would provide the greatest insight and facilitate performance and cultural transformation? Once you find this, how will you create ownership so this becomes the culture's measurement, and not just yours?
This article originally appeared in the October 2012 issue of Occupational Health & Safety.