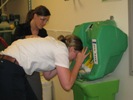
Six Critical Areas in Emergency Shower/Eyewash Programs
They work in unison to help ensure that should a shower or facial flush become necessary, there is little risk of the injury's becoming more aggravated.
- By Steven Gray
- Sep 01, 2011
The first 10 to 15 seconds after exposure to a hazardous material are crucial to prevent further damage to the person's skin and eyes. Even a few seconds' delay could make the difference between serious injury and blindness.
Emergency showers and eyewash systems must be properly placed and fully functional to be effective. Employees need to be made aware of the location and proper use of the stations, the chemicals they are exposed to, and the potential hazards those chemicals present.
Accidental exposure can occur even with proper engineering and written safety procedures. Emergency showers and eyewash stations should be the last line of defense and be supplemented with a written personal protective equipment program. Showers are also useful for extinguishing clothing and removing contaminants from skin and clothing.
ANSI's standard, Z358.1, originated in 1981 but continues to change with advancements in science and accident case studies. It has been revised to improve worker safety in 1990, 1998, 2004, and most recently in 2009. Fixtures that may have been compliant 30 years ago might not necessarily be compliant today.
Regardless of the potential hazard, all eyewash and drench programs should include six critical areas: performance, use, installation, test procedures, maintenance, and training. These six criteria work in unison to help ensure that should a shower or facial flush become necessary, there is little risk of the injury's becoming more aggravated.
Performance
Plumbed showers should deliver at least 20 gallons per minute at 30 psi for a minimum of 15 minutes for showers and 0.4 gallons per minute for an ocular flush. One of the most common problems found in the field are showers with insufficient water pressure; this usually results from faulty installation. A shower/eyewash that is connected improperly will not deliver fluid with enough force to remove contaminates from the skin or quickly extinguish fires.
The valve should be easily activated within one second and should stay open without the use of the operators' hands until intentionally turned off. Most modern eyewashes/showers are ANSI compliant as long as they're installed properly and are constructed from plastic or stainless steel, but some older models were made with lead and should no longer be used. Showers and eyewashes also should be a one-step activation process. Many businesses utilize sink-mounted units that take two or even three steps to activate and are not considered ANSI compliant.
The most recent update to ANSI Z358.1 (2009) specifically focuses on ensuring that the temperature of the flushing fluid is tepid, defined as within a temperature range of 16-38 C (60-100 F). This ensures the affected worker will be able to withstand the continuous flow for 15 minutes without risk of scalding or hypothermia.
Use
Showers and eyewash systems must be used correctly to be effective. Employees must be trained to hold their eyes open during the flushing process. The water coming out does not neutralize, but instead dilutes and washes chemicals away. This is why large amounts of water are required.
However, it is important to be cognizant that different chemicals may require longer rinsing times, especially penetrating corrosives, which may require up to 60 minutes of flushing time. In all cases, if irritation persists, continue flushing and consult a physician as soon as first aid has been given. All employees should be trained on the use of fixtures before they handle hazardous chemicals.
Installation
Proper installation of stations may be the most critical element of an eyewash program. If possible, have the installer consult with the safety director or another employee who is familiar with ANSI Z358.1-2009. Mistakes at installation can lead to costly plumbing and structural changes later and fines for improperly functioning stations in the event of an incident.
Is there a chance that more than one person will be exposed to the hazard? Will one station be enough? Are there special-needs employees who may need access to the eyewash? Should an alarm be installed for isolated workers to alert nearby workers of activation? Consider the water source; will it require a thermostatic mixing valve? What measures have been taken for freeze and scald protection? Can the chemicals you use be drained to the sewer or should they be collected in a temporary bladder? Are there doors or stairs between the worker and the station?
Regardless of the type of unit, be sure the installer is aware of the critical dimensions that the ANSI standard requires to ensure proper spray pattern and accessibility. Be sure that the eyewash location is identified by a highly visible sign. At the completion of the installation, ensure all standards are met by using a flow meter and test gauge and that all applicable accessories are available and easily accessible. In situations where the chemicals used could require the removal of clothing due to exposure, a privacy curtain -- though not required -- should be given careful consideration.
Testing and Maintenance
One person in the work area should be designated as responsible for inspecting, operating, and documenting findings for the shower, eyewash, and combination units and drench hoses weekly. For large facilities with multiple units, it is advisable to use a contractor or vendor to eliminate inconsistent checks because of vacations, promotions, sick days, etc.
Contractors should be familiar with the ANSI standard and be able to give a detailed report on any shortcoming. The weekly check ensures flushing fluid is available at the correct temperature, pattern, and flow and serves to clear the supply line of sediments and minimize the risk of microbial contamination caused by still, sitting water.
During activation, check for any visible damage, leak, rust, and flow obstruction. Replace any defective part immediately. Ensure that spray nozzles are protected from contaminates and that protective caps and covers deploy easily. Ensure the unit continues to run until intentionally turned off. Self-contained and gravity-fed units should be checked visually to determine whether or not the flushing fluids need to be supplemented, changed, or, in some cases, condemned. Also ensure the unit has not been disturbed by confirming the tamper-proof seal is in place.
Visibly check applicable fluid capture systems to ensure that gravity-fed units are at full capacity. In certain situations, it may be necessary to use non-slip mats to eliminate trip hazards and define the perimeters of the "critical dimensions" specified in the standard. All plumbed and self-contained equipment should be checked at least annually to ensure conformity with Z358.1-2009. The inspector should keep a signed data record on the fixture or in a dedicated binder or other central location. Documentation is crucial information that must be provided during an audit or inspection.
Training
Employees who are at risk of being exposed to hazardous chemicals should be made aware of the location of emergency flushing stations. Written instructions should be made available to all employees, with special consideration for all employees who read a language other than English. Workers with contact lenses also warrant special consideration. Chemicals can become trapped under contact lenses and cause serious injury, so part of the training should include contact removal. Demonstrate the use of each unit, even if the differences in the units are slight.
A helpful tool in training and determining the proper placement of equipment is to have the affected employees stand by their appointed workstations and ensure they can reach the stations unassisted in less than 10 seconds (usually, this distance is 55 feet). For caustic or corrosive chemicals, the stations should be immediately adjacent to the hazard. For employees who are farther away than 55 feet, secondary units may prove helpful. Secondary or supplemental equipment only serves as a temporary means of relief until a primary (15-minute) unit can be reached. If bottles are used, ensure their dates are permanently displayed on the bottle. Under no circumstances should expired product be allowed to remain accessible to employees. Secondary units should be checked monthly to ensure that seals and caps are unbroken. Any bottle without a date or that has been used should be replaced immediately.
This is also an excellent opportunity to introduce and explain the importance of the Material Safety Data Sheets. Employees should know the location of the MSDS and should refer to it whenever they are handling a chemical with which they are unfamiliar. Make sure they are aware of the various MSDS sections and their purpose, paying particular attention to section 4, which describes the first aid measures to take in the event of accidental exposure. The MSDS will have information on the PPE that should be worn while handling the chemical. Have all employees sign and date a sign-in sheet saying they have been trained on the location and usage of the emergency fixtures and the MSDS sheets.
This article originally appeared in the September 2011 issue of Occupational Health & Safety.