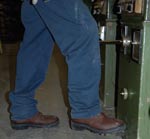
The Art of Making Tough Boots
Footwear worn by workers in aluminum smelters around the world must meet exacting standards.
- By Jerry Laws
- Apr 01, 2010
Manufacturing a protective boot that can meet exacting national standards is challenging enough. When the relevant industry adds its own performance testing to the mix, as the aluminum smelter industry around the world has done, the challenge grows — but this happens for all the right reasons.
Since the early 1990s, 75-year-old footwear manufacturer L.P. Royer Inc. (Royer) has concentrated on niche markets, including smelters. Although the company is relatively small — it has close to 100 employees and produces about 65,000 pairs per year, said General ManagerSerge Boucher — it is well known for its smelter's footwear, having built a reputation for quality and customer service since entering that market in the mid-1970s, when a Canadian customer requested metatarsal protection be added because of crushing injuries its workers were suffering, said Jerry Hould, Royer's business development manager.
The industry became concerned in the 1980s with molten metal getting inside the workers' boots and causing serious, costly injuries. Companies began calling Royer to ask how its boots could be changed to prevent penetration. Royer, which is based in Quebec, Canada, answered with a VELCRO option that allows the worker to remove the boot quickly.
And in the mid-1990s, one large company began developing its own molten metal dip test for footwear, with the test subjecting the boots to temperatures of 950 to 975 degrees C, Hould said. "So now, to be able to sell to this company, our product has to be able meet the Canadian standard, or the ASTM standard in the USA, or the European standard — the CE marking. Now, they request to have the footwear meet their dip test. It is dipped into molten metal, and after the test, they make sure they have no infiltration of the molten metal inside the footwear. No sole separation from the boot."
Companies throughout the industry and around the world now use dip tests. Alcoa developed its own, Houldand Boucher said. Independent laboratories perform the testing.
"They request that we meet these tests," Boucher said."These are special, and there are very few companies around the world that could meet these requirements."
"The comfort of safety footwear today is one of the most important points for the workers, especially in this type of industry. The guys work 12-hour shifts. The work area is generally one kilometer in length or longer. So the people walk, and walk, and walk all day," he said.
Royer has an R&D team of about five people, including engineers and designers, and it outsources work for special services, Boucher said. The company also provides linemen's boots, conductive footwear, chemical-resistant footwear, and protective footwear for agricultural and forestry workers. It produces custom boots and even can produce orders as small as 10 pairs. Hould said the company has supplied boots to a customer who needed a left sole 2 inches taller than the right boot's sole, and it filled orders of two left boots several years ago for a worker who had lost a leg and previously would discard the right half of each new pair he received.
Working closely with customers entails focus groups and face-to-face meetings with customers, health and safety professionals, smelter managers, and distributors to discuss what is good about the boots and what should be improved. The comments are brought back to the R&D team.
"I think it's the best way," Hould said,"because, in the past, to be honest, we developed some products without talking to the customer. And then we took that product to the customer, who said, 'Oh, no, I won't need this. I need this, and this, and this.' We realized we should sit down with the customer and talk with him. Knowing the situation is very important to us; we reduce our time spent in product development."
Reactive and Price-Driven Customers
Last year, while visiting Dubai Aluminum, to which Royer has supplied smelter's boots since 1984, Hould asked his customer why the company bought the Royer boot. "He said,'You know, a lot of people have knocked on the door to sell us safety footwear. And we tried a lot of safety footwear. But we were not able to find safety footwear that lasts as long as your product.' And he told me, 'When we buy your boot, it's more expensive, but at the end of the year, we save money because we buy only one pair per year.' "
Still, many buyers look at price alone. "In the USA and Canada, it's the same: The purchasing department looks at price, price, price. What's happening is, the worker gets very uncomfortable footwear. …The problem is, the guys are buying three of four pairs a year," said Hould.
Too many companies work reactively, they said, explaining that such companies adjust their PPE equipment only after they have an injury. Hould said a smelter in Quebec experienced an explosion last summer in which a worker suffered burns on most of his body but not on his feet, which were shielded by protective boots. That smelter then decided to develop its own dip test, which the Royer boot smet easily. "It is sad that it was an accident, but for us, it proved that we can meet the test that the client needed us to," Boucher said.
The biggest companies in the aluminum smelting industry want to prevent foot burns among their workers because those injuries are so expensive, Hould said. Supplying the industry's major players is beneficial because smaller ones sometimes take their cues from the leaders. In any event, smelting operations and their attendant hazards are similar, wherever they are located, and companies that have multinational operations typically want the same PPE to be used in all of them.
"Each country requires their own standards. In fact, it is the same boot with subtle differences. The same boot meets all three standards," Hould said.
Canada has no compression test for steel-toed boots, but the European Union does, for example. Would it help to harmonize on a single international standard? "Yes and no,"said Hould. "For us, meeting each standard is not a big issue. It's just little things we have to adjust. And then, we have tests." But meeting each standard incurs expenses and investment, such as when Royer is required to get CE or ASTM markings. So an international standard would reduce costs, he said.
This article originally appeared in the April 2010 issue of Occupational Health & Safety.