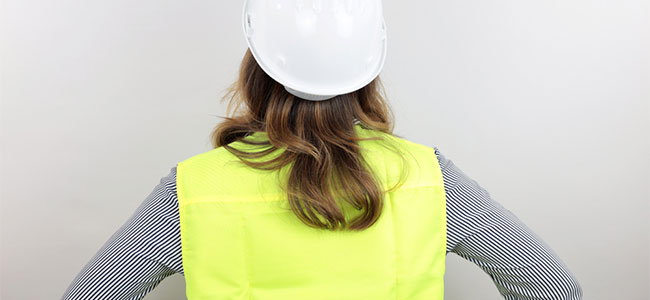
Addressing an Overlooked Danger
Why current helmet standards must be updated to account for rotational motion, a key cause of concussions.
- By Joe Brandel
- Sep 06, 2023
Those in the construction industry are responsible for building the places where we spend our lives, but they continue to face some of the greatest risks on the job. In the U.S. construction industry alone, a total of 21,400 non-fatal workplace injuries and illnesses were caused by slips, trips and falls in 2020. These types of accidents can lead not only to severe injuries but fatalities as well: Between 2003 and 2008, one of the leading causes of occupational fatalities caused by a traumatic brain injury (TBI) was falls at 29 percent.
While the Occupational Safety and Health Administration requires that head protection must be worn by employees at risk of head injury from impact, falling objects, electrical shock, or burns, construction workers are still at risk while on the job. Furthermore, where you work can have an impact on your safety as well. Workers at small construction companies with 20 employees or less are over 2.5 times more likely than those in larger companies to experience fatal TBIs.
Understanding the Risk
One of the most important steps that both employers and employees can take is to understand the risks involved in TBIs. Simply put, traumatic brain injuries are injuries that affect how the brain functions. There are three types of TBIs: mild, moderate and severe. Some types of TBIs can lead to temporary issues, such as how a person thinks, communicates, or moves, while long-term TBIs can cause permanent disability or death.
Accidents such as slips, trips and falls can be critical: When a person’s head makes an impact with the ground or an object, research shows that this typically occurs at an angle, exposing them to rotational motion. Rotational motion is the combination of rotational forces (angular acceleration) and rotational energy (angular velocity) potentially resulting from oblique impacts to the head. In instances where rotational motion is transferred to the brain, the brain can start to deform, which may cause shearing and damage to the brain’s axons or cable transmitters of the neurons.
Rotational motion can lead to diffuse injuries, including diffuse axonal injury and subdural hematoma, while linear injuries (injuries that occur from straight impacts to the head) can cause focal injuries, including fractures and contusions. It’s important to note that in most real-life accidents, both linear and rotational motion occurs, leading to a greater potential risk of injury.
The History of Hard Hats
Today’s helmets and hard hats are not very different than what they were over 100 years ago. Hard hats date back to World War I, when the United States was building ships for the Navy, and the Hard-Boiled Hard Hat was made out of boiled leather and metal in 1919. In 1928, an inner suspension was created, intended to help absorb the impact from dropped objects. Over the course of the 1930s and 40s, helmets made out of aluminum and then fiberglass were developed before plastic hard hats were introduced in 1951. Since then, helmets have been updated to include attachments for face shields, hearing protection, integrated eyewear, and rated chinstraps, yet the helmet itself remains relatively similar to those of the 1900s.
Today’s PPE
The two helmet types under the ANSI/ISEA Z89.1 standard include Type I and Type II helmets. Type I helmets are designed to reduce the force of impact to the top of the wearers’ head, while Type II helmets, in turn, are designed to reduce the force of a side (lateral) impact resulting from a blow that may be off center, in addition to the top of the head. Then there are three classes of helmets: G, general; E, electrical; and C, conductive.
Currently, helmets undergo five performance tests which must be met in order to assign safety helmets their classification under the ANSI/ISEA Z89.1 standard. These consist of impact energy attenuation, flammability, force transmission, apex penetration, and electrical insulation. Force transmission tests determine whether helmets are able to reduce the force of linear impact to the crown of the head. Furthermore, energy attenuation tests analyze a larger protective area of the helmet, including linear impacts to the front, rear, and sides of the helmet.
However, none of the current tests involved determine the impact of rotational motion to the wearer’s head. While some standards in the sports and moto industries are starting to take rotational motion into account in their standards, the construction industry has yet to apply such tests.
For those in the construction industry today, many employers are requiring that Type II helmets, which can include chinstraps, be worn on jobsites. This is an improvement from Type I helmets, which seldom include chinstraps, and, therefore, often fail to protect the worker’s head in cases of slips, trips and falls, as the helmets risks falling off of the wearer’s head. Despite providing additional safety compared to Type I helmets, most of today’s Type II helmets still fail to account for rotational motion and its harmful effects.
What to Consider
While each accident is different, oblique or angled impacts to the head are a far more common accident scenario than linear impacts. What’s more, research has found that the human brain is more sensitive to rotational motion than linear motion, meaning concussions caused by rotational motion occur at lower levels of energy than those caused by linear motion. Yet, there are still steps that workers can take.
The first step is to wear a helmet that is firmly attached to your head. Second, ensure the helmet meets the latest standards and is best suited to your line of work. Third, find a helmet that’s comfortable for you. The helmet that you’re most likely to wear is one that is most pleasant to wear for long periods of time. Lastly, check if your helmet has a tested rotational motion mitigating system installed. Thanks to research and new technology, there are, for example, a number of helmets equipped with a system that allows the helmet to move relative to the wearer’s head, designed to help redirect rotational motion that could potentially be transferred to the head in angled impacts.
While the helmets of today are not too different from when they were first invented, there are ways that workers can do to help reduce the risks of TBIs and rotational motion. The first is education: It’s impossible to know how to keep yourself from harm if you’re not fully aware of the risks involved. Second, prioritize safe PPE usage and ensure that your equipment is up-to-date with the latest standards. Lastly, understand what rotational motion is, its risks, and what options are available that are designed to help mitigate its impact. While the construction industry will continue to face jobsite risks, it’s crucial that employers and employees alike have a deep understanding of the PPE available to them.
This article originally appeared in the September 2023 issue of Occupational Health & Safety.