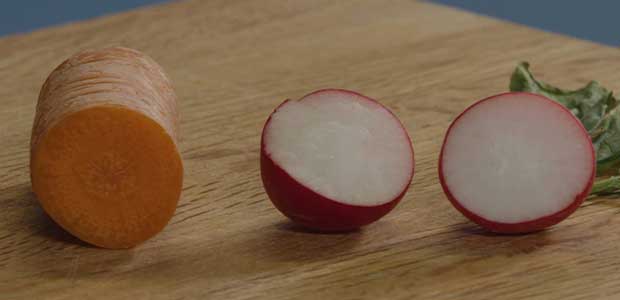
Solution-Dyeing Versus Piece-Dyeing: Does it Make a Difference in PPE?
Understanding the complete fabric creation process can aid in making better PPE choices.
- By Rich Lippert
- Jun 01, 2022
Most of the discourse surrounding personal protective equipment (PPE) is justifiably concentrated on the ability of a garment to minimize exposure to hazards, ultimately making workplaces safer. However, there is one important factor of PPE fabrics that is often overlooked—the dyeing process.
As you weigh your options for PPE workwear, you might be surprised to learn the differences between the “solution-dyeing” process and more traditional dyeing processes known as “piece-dyeing” or “stock-dyeing.”
Visualizing the Difference
In order to envision the contrast in solution-dyeing and piece-dyeing, consider the difference between a carrot and a radish. When cutting into a carrot, you’ll notice the orange color is consistent throughout the vegetable—top to bottom, in and out. Conversely, slicing into a radish will reveal a white interior color which is very different than its reddish exterior.
This is an excellent analogy for solution-dyeing versus piece-dyeing methods, with the carrot representing solution-dyed fabrics, which has pigmentation added directly to the polymers, and the radish symbolizing piece-dyed fabrics, which is dyed after the fiber has been created.
Technically Speaking
In solution-dyed fabrics, color pigmentation is added to the polymer at the very beginning of the process, rather than after it becomes yarn and woven into fabric. Colorless polymer chips are melted together with color pigments. This melted mass is then extruded through a spinneret, which is a device resembling a showerhead, to create the fiber, and then spun into yarn.
In comparison, piece-dyed fibers are dyed following extrusion, meaning the color only penetrates the outer surface of the material. Both methods have their redeeming qualities, but the question still remains—how do these disparate processes impact PPE and its effectiveness?
Durable Dyes
There are many benefits to utilizing solution-dyed fabrics in PPE garments, most notably the increased durability in the workplace and improved color fastness following industrial laundering. Because the color is built-in to the fiber, solution-dyed PPE retains its color much longer than piece-dyed fabrics. The prolonged lifetime of these products underscores the fact that solution-dyeing maximizes an organization’s PPE dollars.
Sustainable Solutions
Aside from maintaining color uniformity for PPE, which is integral for compliance and long-term cost-effectiveness, the solution-dyeing process consumes far less water and waste than its piece-dyed counterpart. It’s estimated that the textile industry loses up to 200,000 tons of dyes to effluence, or liquid waste, annually. While that is a staggering figure, the vast majority of that waste derives from traditional piece-dyeing methods, which can use one to three gallons of water per yard of material produced. In fact, research indicates the solution-dyeing process consumes 90 percent less water and results in 96 percent CO₂e savings.
Piece-Dyed Positives
Although data suggests solution-dyed fabrics are more economically efficient in the long run due to their durability, one area piece-dyed fabrics have an advantage is the initial investment cost. On average, piece-dyed fabrics are less costly up-front than other methods for a number of factors, mainly because this method of dyeing is more commonly used and consequently easier to access.
Another positive is that piece-dyeing can be used for both natural and synthetic fibers, whereas solution-dyeing can only be used for synthetic fibers.
Additionally, because the color is added later on in the textile process, it is easier to make changes to the color. Further, smaller lot sizes are possible and commonplace with piece-dyed fabrics, with solution-dyed materials requiring lot sizes around 10,000 pounds.
Playing a Part in PPE
With a few exceptions, the technical textile industry mainly uses piece-dyed fibers in PPE garments due to the initial savings on material. Considering the color retention and durability benefits, solution-dyeing is used more regularly in industries focused on outdoor materials and furniture, marine equipment, and carpeting. Given the fact that PPE, particularly AR/FR PPE, is worn and utilized in harsh environments, it’s only logical that solution-dyeing would be a beneficial addition to that industry.
Assessing your Options
From initial investment to environmental responsibility, there are a variety of factors to consider when choosing AR/FR PPE for your company. As you ensure your workers’ safety by purchasing the most effective PPE available, it’s important to evaluate whether the garments you are buying are inherently AR/FR, solution-dyed fabrics or treated, piece-dyed fabrics.
The combination of durability and sustainability gained from the solution-dyeing process is unequivocally the best choice for color retention after regular use and laundering, thus extending your PPE dollars. However, budgetary limitations might necessitate piece-dyed fabrics in the short-term. At the end of the day, it’s crucial that your organization purchases PPE that best protects your workers, maximizes your budget and looks the best.
This article originally appeared in the June 2022 issue of Occupational Health & Safety.