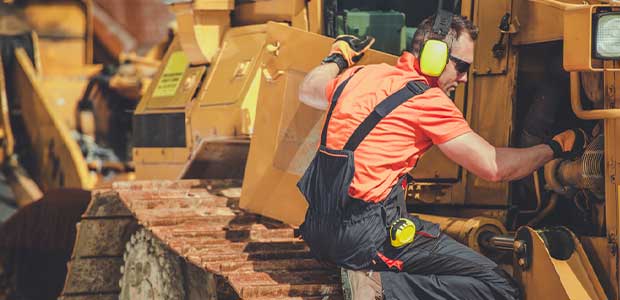
5 Dangers of Working Around Heavy Equipment and How to Stay Safe
- By Devin Partida
- Aug 12, 2021
People who work with heavy equipment, or oversee employees who do, know there are inherent risks with the associated tasks. However, understanding the threats and taking the appropriate precautions to minimize them can keep people safe. Here are five of the biggest dangers and the related preventive measures.
1. Operating a Machine Without Guards in Place
Machine guards cover potentially dangerous parts of a machine to shield workers from the components that pose elevated risks to them. However, some employees find the guarding interferes with the machine’s functionality and remove it. Alternatively, they may not know how to check that the guards are present on the equipment before working with it.
Workers can stay safe by understanding how the guards work and knowing how to verify they are working as expected. Employees should also notify supervisors if they notice that a piece of equipment does not have guards but should. It is possible a maintenance worker removed them and forgot to put them back.
2. Getting Crushed or Run Over
The weight, size and power of heavy equipment pose risks to people who could get crushed between moving parts or run over by a machine. Awareness and visibility help reduce the chances of both types of accidents. For example, educating a person about behaving safely around a machine goes a long way, as does ensuring the workforce has the appropriate high-visibility workwear.
Efforts are also occurring that involve robots and automation to keep people out of harm’s way. Experts have begun establishing associated principles and regulations, such as that robots must be safe and secure before working around humans. Some robots are also specially designed to do dangerous jobs that put people at above-average risk.
Emerging technologies include heavy equipment that operators move with remote controls. Those options keep them farther from the danger zone.
3. Being Involved in Equipment Transport Accidents
It is often necessary to move heavy equipment between locations. Unfortunately, accidents can occur for those involved in the transit or individuals nearby if people do not take the required steps to prevent them. Having a well-balanced load is crucial. More specifically, make sure the cargo rests between the trailer’s wheels and is properly centered to avoid tipping.
People should also plan the travel route before departing. Road features like narrow bridges, underpasses and unfinished surfaces can all cause unwanted but preventable challenges. The same is true for ongoing roadwork. Knowing what a route entails beforehand lets people prepare accordingly to remain safe.
4. Failing to Learn the Associated Risks of Machinery
Coverage of the most common violations of OSHA standards highlighted a focus on reducing employee exposure to risks that are most likely to cause serious injury or death. One of the most commonly cited general industry violations concerned a failure to have a written hazard communications program.
Practicing effective hazard communications involves implementing specific processes and procedures to tell people about the risks present in a task before people engage in it. However, safety managers can help people stay safe by making them aware of the threats by using understandable language and real-world examples.
5. Using Equipment Before Receiving Adequate Training
All employees need the right amount of training from a qualified provider before operating heavy equipment. However, one of the associated challenges is that there are different state-specific educational requirements for workers.
For example, all construction workers in Nevada must complete 10 hours of OSHA training. However, superintendents, forepersons and supervisors need 30 hours. Construction workers are not the only employees who are likely to work around heavy equipment, of course. However, this example shows the importance of ensuring the workforce gets the necessary coursework done or verifying that people have the training completed before getting hired.
Improved Safety Starts with Risk Awareness
It’s impossible to eliminate the threats associated with heavy equipment. However, knowing the most significant dangers helps all workers and safety personnel change their behaviors accordingly and adjust training content when applicable.