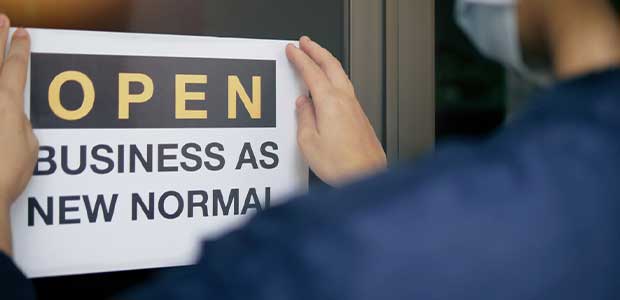
5 OSHA Guidelines to Follow During Reopening Procedures
- By Devin Partida
- Jul 13, 2021
The logistics of opening operations back up in the wake of the pandemic is more complex than ever. All organizations must ensure employees return to a safe and healthy work environment, whether industrial or otherwise. It’s not just about the sanitation and cleanliness policies that have been on all of our minds lately either. OSHA graciously reminded everyone that other, non-COVID-related safety obligations, are still important — and could easily fall by the wayside. It raises the question: what are some of the more pertinent OSHA and general safety guidelines that everyone should be aware of?
1. Health Monitoring
COVID-19 has certainly made everyone more aware of his/her personal health, but it’s something that both employees and employers should have always been concerned about. Workers who feel sick or are showing signs of health decline should stay home, not just to prevent the spread of illness, but also to take care of their bodies and rest. They should not be forced to work, and there should be policies and minor benefits in place to accommodate this. Paid sick time is the ideal approach, but at the least, employees should be allowed to seek additional health consultations or support. The appropriate health insurance should be available and active. As for the employer’s responsibility, there should be systems in place to monitor and detect employee health concerns. It should be done promptly, too.
For example, contact tracing is important, but it’s only useful after an illness has spread, and even then, it may be too late to take the proper precautions for everyone else’s health. Temperature monitoring stations, mask requirements, proper respiratory etiquette, regular workplace/workstation sanitation and a proper reporting system are all necessary. Vaccinations should also be considered and should be a requirement before workers return to the fold.
It may be possible to adopt some of the IoT technologies that are being used in health care to fight COVID-19. Remote patient monitoring, for example, could be deployed in the workplace to monitor the health and safety of various workers.
2. Safety Refreshers
One of the steps OSHA recommends employers take is to create a “refresher” or introduction course for employees which explores safety and health training. It should reveal and discuss measures that might have been deferred during the shutdown.
It’s also a good idea to incorporate common safety policies that employees might have forgotten, or just need reminding of. That includes, but is not limited to, standard operating procedures, safety requirements, preparation guidelines, equipment use, etc.
Some organizations may need to cover workplace exposure or hazard concerns, including those that might have cropped up during the shutdown because of neglect, inactivity or other events. Equipment, for example, may be prone to malfunctions or failures because it hasn’t been used in a while.
OSHA explains in more detail: “Employers should also revisit and update standard operating procedures and remember that exposures to hazards may increase during shutdown and startup periods. It is important for employers to review and address process safety issues — including stagnant or expired chemicals — as part of their reopening effort.”
3. Limiting Capacity
Not all regions or locations are opened back up yet, and there are some restrictions to consider before doing so. New York, for example, is opening in phases thanks to a program that divides the state into smaller regions for “reopening purposes.” It follows CDC, OSHA, and EEOC guidelines to “focus[...] first and foremost on getting people back to work and easing social isolation, without triggering renewed spread of the virus or overwhelming the hospital system.”
What’s more, it continues to remain a valuable resource for OSHA and safety recommendations, just as it did early on in the pandemic, before the second wave hit. The major idea presented is to open back up slowly, by limiting the capacities of the workforce. It’s similar to how non-essential employees were first allowed to work from home before it became more widespread and applied to everyone. In most cases, it’s up to the employer to decide who should be returning to work and when.
Yet, it’s still crucial to maintain lower capacities to prevent the spread of COVID-19 and to allow everyone the opportunity to safely return.
4. Open Communication
OSHA also specifically mentions the fact that employees have the right, by law, to raise concerns about health and safety conditions without fear of retaliation.
“Employers also should remember that Section 11(c) of the Occupational Safety and Health Act, 29 U.S.C. 660(c), prohibits employers from retaliating against workers for raising concerns about safety and health conditions.”
It calls for developing or maintaining a proper communication channel so employees can report health-related concerns or suggestions. There should be a clear path that reports follow, so they’re not just taken by a minor level of management and forgotten. It may or may not call for the introduction of a health and safety board that has the time and manpower to vet potential safety requests and come up with the appropriate solutions.
Finally, all concerns should be elevated appropriately and not just the ones pertaining to COVID-19.
5. Proper Planning
OSHA urges employers to consider “potential hazards related to the Coronavirus, as well as those stemming from routine workplace processes.” In other words, there’s a lot more going on than just physical sickness. Employees are also stressed, fatigued, distracted and sometimes may incur mental ailments, like depression, as a result of the ongoing pandemic and workplace events. These situations and potential problems should be heavily factored into the workplace reopening.
Some workers are hesitant to return, fearing not just their safety, but also because they’re contending with any number of additional problems. Employers should be mindful and empathetic, but more importantly, there should be clear guidelines in place to help workers through such times. OSHA even goes on to say that these problems can compound, creating bigger health and safety concerns: “Employers should carefully plan before attempting to increase production or tasks to make up for downtime.”
The Return to Normal
As organizations plan and kickstart efforts to bring the workforce back into the workplace, there are a ton of concerns that need to be considered. Namely, the health and safety of all returning to the office, warehouse or factory should remain a priority. It’s always a good idea to have monitoring and health reporting programs in place. Everyone should be given a proper safety refresher when they return, too. Capacities should remain limited, with workers brought back to the workplace in groups.
Finally, there should be an open channel of communication for health and safety concerns to be voiced, as well as a proper plan for the big return event, including direct support for affected employees.
It’s important to remember that many of these ideas or strategies were presented by OSHA directly to help employers prepare for the reopening of the economy and greater operations.