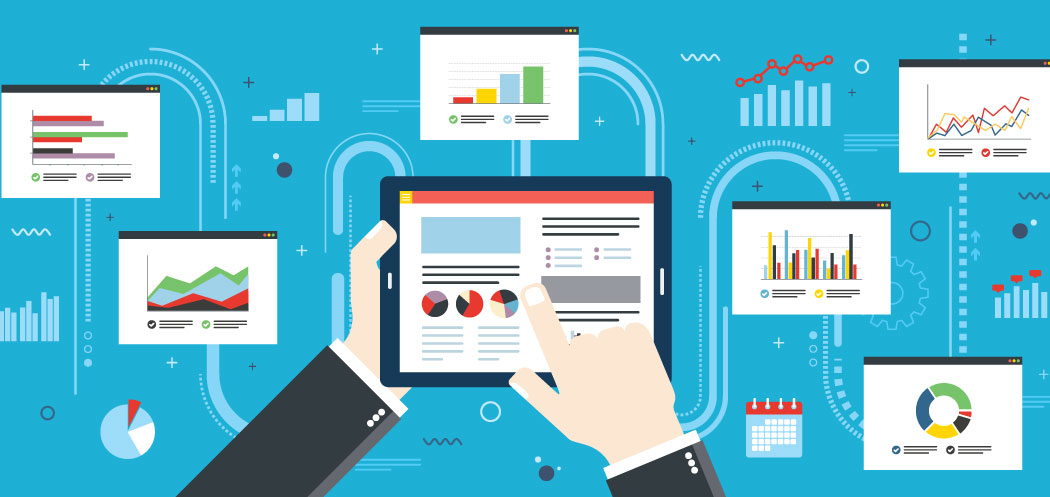
SPONSORED
5 Safety Metrics You Need to Start Tracking
Increasingly, more and more organizations are digging into their data to uncover new insights and make better-informed decisions. But building out your EHS reporting process from the ground-up can seem daunting. With so much data available, where do you start? Which KPIs are most important to track? Consider this post a primer on the five safety metrics your EHS department should be reporting on each month.
5 Safety Metrics Worth Tracking Every Month
1. Incidents and Near Misses
Historically, many organizations have focused most of their reporting on lagging indicators, like incidents and near misses – which is a great starting point. Measuring these kinds of lagging indicators tell us how we’ve been performing and provide a solid foundation to build upon. Once you’ve established your baseline performance level, you can then consider putting controls in place to improve these key safety metrics.
2. Inspections and Audits Completed
While lagging indicators like incidents and near misses can show us how we’ve performed in the past, they can’t provide us with much insight into future risks we need to be aware of. To build a world-class EHS program, it’s essential to shift your reporting focus to leading indicators – starting with the number of inspections and audits completed on your job sites on a monthly basis. To collect good quality data, make sure all your employees are aware from day one of potentially unsafe conditions and conduct formal training sessions that cover how to complete inspections and hazard assessments.
Related: How to Use Leading Indicators to Scale Your Safety Program and Amplify Your Safety Culture
3. Corrective Actions
As EHS pros, we’re all striving for safety excellence, and assigning corrective actions is an important part of the continuous improvement process. On a monthly basis, you should be assessing the number of corrective actions your workforce is completing. It’s also critical to monitor the number of corrective actions that are being assigned but not completed. Use this data to instill a sense of urgency in your workers – make sure everyone is on the same page and working together to get all corrective actions closed out as quickly and as safely as possible.
Learn More →
4. Employee Training
Managing employee training records can seem tedious, but it’s one of the most essential safety metrics to track each month. Keeping on top of which members of your team have valid training certificates (and when those certificates are going to expire) shows you’re taking a proactive approach to workplace safety and can help you stay compliant.
Related: The Unconventional Guide to Employee Training
5. Worker Participation
To prevent incidents and reduce risk, every member of your organization needs to be involved and actively participating in your EHS program. This means every employee at every level needs to know what the company’s safety goals are so they can contribute appropriately. When measuring worker participation, a few key safety metrics to track each month include:
– Number of safety meetings and toolbox talks attended
– Number of training courses completed
– Number of inspections conducted and submitted
– Number of closed out corrective actions
Next Steps
Now that you have a better idea of the safety metrics you should be tracking each month, watch this webinar to learn data collection strategies you can implement to enhance your reporting process.