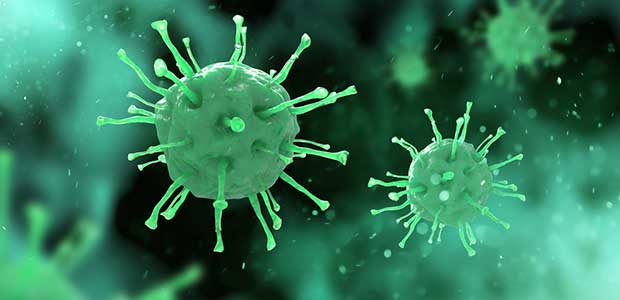
Contemporary Issues in HSE Management
Post-COVID-19, HSE management will confront new challenges and will have new tools and opportunities.
- By G. C. Shah
- Oct 01, 2020
In an important sense, we are at the cusp of a major transformation in HSE management. Although COVID-19 has accelerated changes, many other variables were at work which were necessitating changes in corporate and HSE management. Based on author’s experience and observation of industry leaders, the following are some of the key change agents:
Fiscal Prudence
As we all know, COVID-19 has had debilitating effect on worker health as well as on economy on global scale. Many companies, even including industry leaders, have registered unprecedented loss of revenue. Experts suggest that economic recovery will likely be slow.
In this environment, HSE budgets have been severely curtailed. Primary concern for an HSE manager is three-fold: worker safety, regulatory compliance, and cost-effectiveness. Some of the avenues a manager could consider are:
Prioritize expenditures based on risk. High risk items need to be resolved quickly; while low risk items can be deferred. Low risk items would need to be monitored, however, until they can be addressed.
Align HSE objectives corporate goals. This is not to say HSE managers do not align with corporate goals. However, the intent here is that HSE manager should critically examine expense issues and ask: “How would this expenditure help improve safety, health, and environmental compliance?”
Pair down without sacrificing safety. Get contractors to align with corporate goals of fiscal prudence without sacrificing rigor of worker safety, health, and environment.
Use “incremental” approach in buying new items. Try to avoid “nice-to-have,” items or the items with visual appeal but little effect on safety, health, and environment.
In many cases, the above list of avenues may be easier-said-than-done. However, the point I that following a systematic thought process geared toward fiscal prudence will help ensure cost effectiveness in the long run.
Digitization
The term “digitization,” is an umbrella term to indicate tools and software used for HSE compliance, communications, and plant and corporate management. Some of the examples are paper-less safety work permits/work orders, digital pads (say, I-pad), continuous monitoring of confined spaces, LDAR (Leak detection and Repair) management, digitized OSHA records, on-line meetings, and others. As you may expect, extent of digitization varies from company to company. It should also be pointed out that digitization creates its own problems, which of not managed properly could scuttle efforts for minimizing risk and achieving regulatory compliance. Consider the following:
Before purchasing and installing, make a thorough risk and cost assessment. Consider what could go wrong. (You may call this as HAZOP-Hazard and Operability Assessment). For digital systems, make sure data that is recorded in database is accurate. It should have means to identify instruments which are not working (self-diagnostics are typically available on many instruments).
Take incremental approach toward implementing digitization. For a small company with a single location, high powered digitization may not be cost-effective. However, small companies can take a step-wise, and economically calibrated approach to digitization. Here again issues to consider are: How does that help, in the short run as well as in the long run, manage HSE?
Network updates and instructions from IT department are not a direct part of an HSE manager. However, it is helpful to consider potential risk arising from poorly written instructions.
With depressed budgets, an HSE manager faces formidable challenges. On the one hand, she/he has to keep overall risk at manageable level, and also in the long run, need to stay competitive. Without doubt, the future of HSE management is “digital,” but the key is gradualism—implement digitization through fully in a risk-averse manner.
Data Analytics
In recent years, this term has emerged in HAS management lexicon. Briefly put, this term means collecting and analyzing HSE data to make actionable decisions. We all know, volumes of data exist including OSHA-300 logs, environmental stack testing, worker exposure to chemicals data, noise exposure, accident investigations and many others. We also recognize data by itself has no value. Data analytics software helps identify areas which could be improved. For instance, software can help identify potential trouble spots. An impressive array of software including Tableau, SAP analytics, Power BI(Microsoft), SAS, IBM-software, Thought Spot and many others are available. Some have Cloud based services with monthly rental charges. Consider the following:
For small one-site companies, data analytics may not be justifiable. Typically, data volume is relatively small. Excel (Microsoft) may be used with inhouse resources. Data sorting, descriptive statistical analysis, and correlations can be accomplished with your existing MS-Excel. Of course, statistics need to be applied carefully and with proper context. You want to stay away from broad generalization of results.
With large volume of data, Excel or in-house resources may be unsuitable. Many data analytics programs offer utilities for data cleaning, modeling, and visualization. Software makes it easy to quickly identify actionable areas for enhanced HSE compliance and risk reduction. Before such a purchase, consider
- What systems you need to be able to use the software?
- What are data requirements? (Is your data reliable?)—In any data analytics, remember the GIGO principle (Garbage In Garbage Out)
- Cost (rental or purchase the product)
- What type of training and personnel would be required to use the software effectively, or cost-effectively?
- What is the market resilience of the vendor? (Could the vendor be merged or be divested and what quality of service do you get then?
- Survey current users, get their opinion on the product value, service/help they received from the vendor, startup difficulties, and others.
With the current pricing levels of software, data analytics software becomes an economy of scale issue—smaller data volumes (such as small organizations) may find data analytics not justifiable in short run.
To sum up, data analytics would be helpful if results of statistical analyses are viewed in proper context along with relevant assumptions. Full discussion of descriptive and inferential statistics is beyond the scope of this paper, but worth considering while embarking on data-driven HSE management.
Workforce Management
While this is not a new issue, it is the essence of HSE management. Today, an HSE manager faces three key issues:
- Ethnic/geographic diversity
Today, most work force is diverse. Workers respect and recognize ethnic and geographic diversity and work as a cohesive team. For multi-site or multi-national organizations, HSE managers should stay familiar with cultural differences, differences in societal norms, their sensitivities, and language differences. The bottom line is ALL workers must have unambiguous understanding of HSE policies and procedures.
In the HSE field, anecdotal data suggests team work transcends gender differences. The key goal is to instill team work and work for the common good of the company.
Generational diversity sometimes shows up as follows: Older workers are less enthused about new digital “gadgets,” while younger workers tend to view safety for granted. Strength of both groups could be harnessed: Consider developing training programs which would enhance acceptance of new devices by older, or more experienced workers. Often poor instructions (As is, sometime, the case with IT instructions), or lack thereof tends to turn off experienced workers.
Younger workers can learn from their experienced counterparts: say, interpret results of confined space monitoring, doing safety audits, maintain respiratory protection gear, managing stack testing for environmental compliance and so on. Risk of not implementing cross-training is that when older workers retire, you may be left with a void of practical knowledge, and this could lead to greater risk.
In addition, consider the following:
Online training. Partly as a result of COVID-19, there is increasing interest in online training. Of courses, this training helps reduce travel and conference cost, it may lack rigor of face-to-face meetings. Document the training. Get workers’ opinion on effectiveness of the training.
Plant Operations. Some HSE workers lack an understanding of plant operations. For example, a refinery HSE worker in a refinery may not have a working knowledge of crude distillation, or delayed coking, or other similar operations. This understanding, in the author’s view will help improve communication between Operations personnel and HSE workers. This understanding could also help improve risk management.
Accurate Records. Ensure HSE manuals, procedures, and compliance records are accurate, updated, and quickly available to workers.
Mergers and Acquisitions
In a turbulent marketplace, mergers and acquisitions tend to be more frequent than those in a placid economy. Mergers (or say divestitures) cause anxiety among workers. Rumors tend to proliferate. Obviously, this puts strain on HSE management. Consider the following:
Maintain Positivity. In divestitures, anxiety of workers could result in distraction and this could contribute to a greater risk of mishaps or omissions. Workers may get hurt and environmental and industrial hygiene compliance could suffer. HSE manager has to assume the role of a coach. Despite an environment that could be filled with negativity, the manager has to encourage them, inspire them. Obviously, this is by, no means, easy. HSE manager herself/himself could end up losing job as a result of divestiture.
Accurate Records. If a company or a plant is being acquired by another company, their due diligence will focus on the HSE infrastructure: HSE manual and its updates, regulatory compliance, training records, and other related documents. Poorly maintained documents or incomplete records could lead to reduction in price the company is willing to pay. Beyond that, it simply makes ample sense to have a robust HSE infrastructure.
Due Diligence. If your company is acquiring another company or a plant, your due diligence should include, at least, HSE systems, records on training and regulatory compliance.
To sum up, HSE management today is presented with some formidable challenges as well as unique opportunities.
This article originally appeared in the October 2020 issue of Occupational Health & Safety.