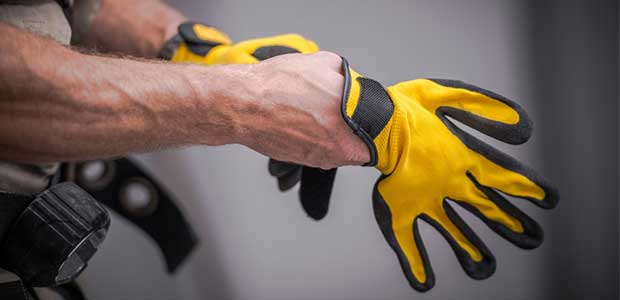
A Requirements Checklist for Work Safety Gloves
When accidents occur, the proper set of gloves can save a worker’s hand.
I have spent my entire life in the business of making gloves. I grew up in Acton, Canada, where the smell of the leather tanneries hung in the air day and night. I started helping my father make and sell gloves when I was eight. After I got a degree in chemistry, I was sent to study at the Reutlingen leather school in Germany, which you might call the “Hogwarts of leather making.” I continue to work in the family business, which has grown into one of North America’s biggest glove suppliers.
If there’s one thing I understand, it’s how important the proper gloves are for safety. When accidents occur, the proper set of gloves can save a worker’s hand.
When you set out to buy gloves, you need to compile a clear set of minimum requirements. These requirements will be based on any industry/government standards that apply to your work as well as the features your workers need in a glove to be able to complete their jobs safely.
Your requirements checklist will depend on the specific task the glove is needed for, but to help you get started, here’s a general checklist of things to look for.
Dexterity
There are standards for dexterity, but really you need to run specific trials to understand the dexterity needs of your workers. Before purchasing gloves, you should acquire samples and have workers test them out for about a week. If your workers can’t complete their tasks while wearing the gloves, they won’t wear them, and gloves only work if they’re worn.
Grip
As with dexterity, determining your requirements for grip requires specific trials. The gloves may also require special coatings. Sheet metal, for example, is usually covered in a metal-handling oil to prevent rust—and you need a specific glove for the work. If you’re making a large sheet of glass, say for the skin of a highrise, then you need an extremely good grip, along with cut resistance. If the glass slips, you instinctively tighten your grip, and the glass can cut through you like a blade. “General purpose” gloves will not suffice.
Cut Resistance
Cuts are the overwhelming number one on the list of hand injuries, so cut resistance is critical.
Modern materials have revolutionized cut resistance. For example, Kevlar, the same material used in bulletproof vests, can be spun into thread and knitted into gloves to provide remarkable cut resistance. If you’re wearing the correct glove and a piece of glass slides into your hand, you may not get cut. If you do get cut, the wound will be far less severe than it otherwise would have been.
You should make your choice on cut resistance based on standard ANSI cut levels. You’ll find this and other safety standards at www.rethinkinghandsafety.com.
Abrasion Resistance
Abrasion injuries are second only to cuts, which makes abrasion resistance another important factor. Leather still provides great abrasion resistance, but modern materials are catching up fast.
Abrasion resistance also relates to the overall life of the glove. I have seen manufacturing environments, for example, where even high-quality gloves must be changed out for a new pair four times a day. If your work includes substantial abrasion, you will want to run a glove trial long enough to see if the glove holds up over time.
Puncture Resistance
When choosing gloves for puncture resistance, you need to know if you are specifically dealing with small objects like needles, or larger objects like broken glass. You will find specific standards for each. Puncture resistance always reduces dexterity and comfort, so difficult choices must be made.
Impact Resistance
Gloves with impact resistance include padding on the top of the hand and the fingers. They evolved out of sporting gloves, like those used for dirt biking, and are surprisingly comfortable.
Some industries often expose workers to severe impact dangers, especially from heavy equipment—and over the last few years, impact-resistant gloves have dramatically reduced things like back hand fractures in the oil and gas industry.
Heat Resistance
Industry has made huge strides in protecting workers from heat dangers through automation and tool redesign, but in certain applications, gloves remain crucial for handling things like hot cooking oil, welded parts and molten metals. Heat-resistant gloves have specific temperature ratings, and you need to do careful research on what you require.
Vibration Resistance
Vibration resistance is a vital requirement for workers using pneumatic tools or similar equipment, which can cause hand-arm vibration syndrome (HAVS), a serious disability.
For tools with high levels of vibration, like a jackhammer, choose a glove with a lot of anti-vibration padding; for smaller tools like a grinder, go with a thinner, more form-fitting glove. A glove with too much padding can actually increase forearm strain and increase the likelihood of HAVS. Also, full-finger gloves are much better than half-finger versions, as HAVS is most likely to develop in the fingertips.
Hazardous Substances Protection
There’s no such thing as “generic hazardous substances protection.” If a job includes the handling of chemicals, it’s critical that the glove company you use knows exactly which chemicals, so the glove or glove coatings can be exactly right.
For example, there’s a glove made of polyvinyl alcohol that’s resistant to a wide range of quite hazardous chemicals, but it’s soluble in water. If it comes in contact with water, it will fall apart quickly.
Importantly, no chemical-resistant glove will keep the bad stuff out forever. You need to know how long a resistant glove can hold out, and when it needs to be thrown away.
Microorganism Protection
Microorganism protection is a feature found in disposable gloves used mostly in healthcare applications. Make sure to also consider abrasion resistance, puncture resistance, allergies, powdering and more.
Winter Warmth
When workers operate in cold conditions, warm gloves are essential to protect against frostbite. To choose the right winter gloves, you need to know what temperatures workers operate in and for how long.
Any good winter work glove will have multiple layers, manage moisture effectively, and stay warm even at the fingertips. The lining should be wool, polypropylene, or Thinsulate—never cotton.
Length of Cuffs or Separate Sleeves
Are your worker’s arms also in danger from burns, cuts and abrasions? If you need a cut-resistant glove, it’s likely you also need a long cuff or a separate protective sleeve.
Custom Requirements
Do workers finish up a task by pushing in a pin with the palm of their hand? Maybe you need a glove with a thick pad right at that spot. Do you need extra cut protection along the thumb?
Large manufacturers may have what you need or may custom design a glove—do your homework and be specific.
Laundering Ability
A glove’s laundering ability is often ignored during the glove selection process, but it’s crucial to long-term value and total cost.
Most companies will simply throw out even highly expensive, custom gloves when they become overly sweaty or dirty. I find this a tremendous waste of money and resources. If you pay $10 for a pair of gloves and manage to launder them just once at a cost of $0.50, you’ve saved $9.50. In a company with thousands of employees, that can add up to real money.
Coatings
An enormous number of specialized coatings are available for work gloves, either for the entire glove or just for the palm and underside of the fingers. These coatings may apply to a variety of needs above, and you definitely need expert help in selecting the right coating.
Comfort and Fit
The question of comfort and fit is vital to all glove types, but comfort requirements may depend greatly on the length of time each glove is worn for a specific task. That makes a real-world trial even more important. Remember: a glove means nothing if it’s not worn.
Choosing a Glove Based on Your Checklist
We live in a world where more means better, but that’s not the case with gloves. The proper glove is the one that meets—not exceeds—the minimum requirements.
If you exceed the minimum requirements, the glove will most likely wind up too bulky, and workers won’t actually wear it. As with Goldilocks, “just right” is just right. Because of this, you will likely find that you need multiple types of gloves for different tasks.
With this checklist as a guide, create your specific list of requirements, per task. Give this information to a reputable glove company and let them choose two to three samples for you to test out, alongside the incumbent glove. Based on these tests, you will then be able to determine the proper glove and ensure that your workers are protected.
By putting thought and research into this important decision, you just might save a hand.
For more advice on hand protection, you can find Rethinking Hand Safety on Amazon.
This article originally appeared in the October 2020 issue of Occupational Health & Safety.