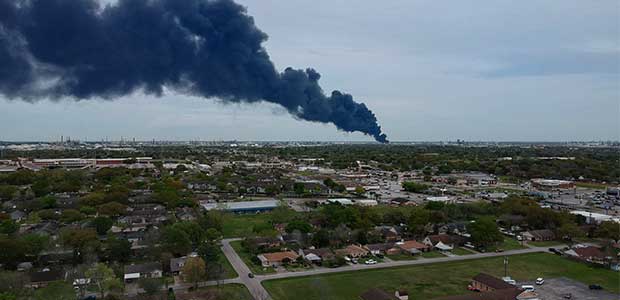
New Gas Detection Technology Isolates and More Accurately Measures Dangerous Compounds
Unfortunately, explosions are a real hazard for the petrochemical industry. Luckily, new technology allows communities to detect the right gases in record time.
- By Mark Heuchert
- Jun 01, 2020
For those who live in and around Deer Park, Texas, the site of a smoke plume or the sound of an alarm are relatively common. The community—which sits fewer than 20 miles from downtown Houston and was once the site of the Battle of San Jacinto where Texas won its independence from Mexico—is nestled in the heart of South East Texas’ petrochemical industry. Many of its residents work for chemical companies, refineries and storage facilities. Their families shop, go to school and attend church in the shadow of smoke stacks.
However, on March 17, 2019, familiarity didn’t make the sound of alarms and sirens any less frightening. A large explosion at the Intercontinental Terminals Company (ITC), a petrochemical storage facility in Deer Park, resulted in a fire in one of the company’s storage tanks. Over the next four days the fire would spread to consume six more tanks. Even after the fire was extinguished, a large black plume of smoke created by the massive fire could be seen throughout Houston’s greater metro area, and the elevated levels of toxic gases in the plume presented a legitimate threat to air quality. One particular concern was benzene.
According to the Center for Disease Control, the toxic gas—which can be found at various levels in volcanic eruptions, forest fires, crude oil, and even cigarette smoke—can cause shortness of breath, headaches, dizziness, confusion, an irregular heartbeat, tremors and unconsciousness, with extreme or extended exposure potentially causing death. And even in low concentrations, benzene is categorized as a carcinogenic.
This fact in particular led the National Institute for Occupational Safety and Health (NIOSH) to establish the Recommended Exposure Limit (REL) for benzene to be 0.1 parts per million (ppm), or 100 parts per billion (ppb). Since benzene carries such a slight REL, the chemical requires extremely low-level detection—it often has to be measured at levels at or below 0.1 ppm.
Measuring Volatile Compounds in the Field Can be Confounding
According to a press release issued by the Environmental Protection Agency on March 21, “one-hour levels of benzene in Deer Park were measured at a maximum of 190.68 parts per billion at 4 a.m., dropping to 48.03 ppb at 5 a.m. and 8.12 ppb at 6 a.m.”
The release went on to state that, due to wind shifts, elevated benzene concentrations of 165.17 ppb had also been measured nearly 15 miles from Deer Park the prior evening. The EPA’s release helps to illustrate how confounding it can be to gather timely and accurate field measurements for Volatile Organic Compounds (VOC).
One potential detection method is traditional air sampling coupled with laboratory analysis. This is not only expensive, but it is also too time consuming in an emergency when minutes matter. Photo-Ionization Detectors (PID), often used in combination with pre-tubes, are well-proven technology tools for detecting Volatile Organic Compounds (VOCs). However, while PIDs can detect benzene, they will simultaneously detect other VOCs as well, which severely limits their effectiveness for use by emergency response teams in the field. For starters, the presence of other VOCs, such as toluene and xylene, can cause a false positive reading. That, in turn, can lead to false alarms and misinformation being distributed to impacted communities.
For PIDs to effectively isolate and accurately measure benzene gas, emergency response teams would need to be equipped with gas detector tubes, or pretubes. Pretubes are glass vials that are filled with a chemical reagent that reacts to a specific chemical or family of chemicals. Thus pretubes are necessary for PIDs to precisely identify which VOCs are present in the air. However, pretubes are consumables with a limited shelf life. Since incidents like the ITC fire can be widespread and take days to resolve, it is not always feasible for response teams to stock sufficient quantities of pretubes for such large-scale emergencies.
New Technology Advances Measurement Methods
Just two months after the Deer Park incident, Dräger, an international manufacturer of medical and safety technology, introduced a new device that combines the PID sensor with another reliable technology, Gas Chromatography (GC).
GC is a technique involving the separation of compounds based on their volatility and unique chemical characteristics. GC makes it possible to target and measure the levels for one selected chemical without having to wade through data on other compounds that might be present. That means that a team can quickly and effectively test for a predefined substance, such as benzene, in a matter of seconds.
Moreover, these technologies, together with an advanced, proprietary algorithm, can detect and measure more than 29 toxic gases to the parts per billion (ppb), depending on the gas. Specifically, the technology can measure concentration levels as low as 50-70 ppb—that’s critical when attempting to measure a gas like benzene, given its especially low REL.
How the Combined Technologies Work
The device, called X-PID 8500, combines two tested technologies—Gas Chromatography followed by Photo-Ionization Detectors—to successfully achieve selective VOC detection. GC uses a column to separate different gas molecules based on their boiling points. Different gas molecules remain on the column for a certain amount of time, known as the retention time. As ambient air passes through the column, gases with lower boiling points generally exit more quickly, while gases with higher boiling points take more time to exit. While traditional lab technology requires the use of compressed gases to transport a sample through the instrument and fuel a flame detector, this device effectively employs ambient air as a carrier gas and thus does not require compressed gas to fuel a flame detector.
Next, the device employs Photo-Ionization. Gases exiting the GC column are ionized by UV light emitted in the PID. The high-energy light ejects electrons from specific molecules, creating an electrically conductive gas called a cold plasma. If it hits the detector, a space between two wires becomes conductive and a current flows.
Separating the substances in the GC-column and subsequently ionizing and detecting them will create a characteristic model of a sample. Each detected gas is shown as a peak on a time scale. Highly volatile substances will be found at the start of this scale, with less volatile molecules following behind. Complex mathematical algorithms help separate peaks that are in close proximity or overlap and assign them to specific substances (by type and concentration) using databases.
A Solution for Emergency Testing
This new technology would be particularly advantageous in emergencies like the ITC fire. When a variety of VOCs are present, as was the case in Deer Park, running Gas Chromatography in a lab is slow and impractical. Each compound has to be separated, and to support such separations, a long GC column must be used, sometimes reaching 100 meters in length or longer and taking hours to measure.
The technology uses a shorter GC column while limiting the compounds to be analyzed. This allows for benzene to be isolated and measured in as little as 30 seconds, even if other VOCs are present. Not only is that speed important, but by minimizing cross sensitivity compared to a standard gas detection PID, this new technology also significantly reduces the potential for a false-positive measurement and resulting false alarms.
Additionally, the device does not require the use of pre-tubes, so it is faster and easier than conventional methods. Perhaps most importantly, because it uses no costly consumables with limited shelf lives, there is no need to continuously maintain an up-to-date inventory. Other features include a robust exterior design to ensure the device performs in the most severe conditions and a temperature control sensor unit maintains a constant temperature above the ambient air temperature and separates water vapor from the target compounds to ensure reliable measurements in harsh environments.
No one wants to see or have to respond to a chemical plant fire, a refinery explosion or an accidental release of toxic chemicals. However, as residents of Deer Park know all too well, in the petrochemical industry, the potential for such an event is an unpleasant and ever-present reality. To protect communities, planning and preparedness are essential—that includes identifying the best tools and technology to accurately measure air quality and detect volatile compounds—so when emergencies happen, the appropriate teams and officials are equipped to respond.
This article originally appeared in the June 2020 issue of Occupational Health & Safety.