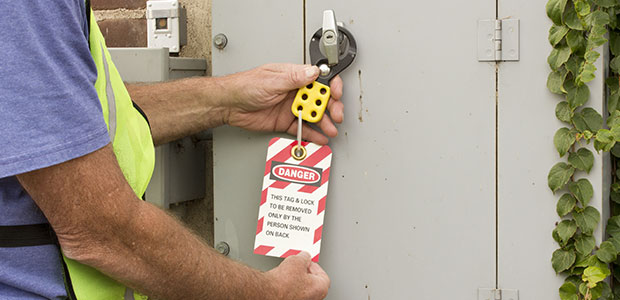
How Today’s Technology is Enabling the Next Generation of Electrical LOTO
Electrical LOTO programs are important for any safety program.
As we enter a new decade, lockout tagout (LOTO) will remain a mainstay of any safety program. However, as standards and regulations evolve, so must a company’s LOTO procedures, requiring it to evaluate, improve and expand upon its electrical safety processes. Many sources of energy must be considered in a LOTO pro- gram: mechanical, pneumatic, chemical, hydraulic, thermal and electrical to name a few. Electrical energy often presents unique challenges due to its invisible nature—we can’t see, hear, or smell electricity. Yet, if it is left unchecked and an incident occurs, it can be one of the most fatal and costly. Regardless of the industry, one thing that all modern manufacturing facilities have in common is the presence of electricity. From heavy industry to commercial and everything in between, identifying and controlling electrical hazards is an important part of every safety program.
When thinking about electrical hazards, it is important to take a comprehensive view. Not only does electricity impact all facilities, but it also impacts everyone present at the worksite. Electrical safety programs must address not just electrical work, but also electrical hazards encountered during normal plant operations as well as routine maintenance, un- scheduled service, cleaning, and repair situations. An electrical safety program will impact electricians, non-electrical maintenance workers, technicians, operators, cleaning crews and groundskeepers.
As manufacturing processes become more connected, it is not uncommon to see the need for multiple trades to access electrical equipment increase, and more distractions introduced. Even the best workers have bad days, and experienced workers can become complacent. Consequently, most incident investigations reveal multiple errors or deviations from the process. To establish a best-in-class electrical safety program, it is essential to look beyond compliance and embrace new technology and best practices that address human factors.
When working on or near electrical equipment, it is important to establish an electrically safe work condition. This is done by de-energizing the equipment, following lockout tagout procedures, and then verifying the absence of voltage. In the past, the verification step was performed by electrically qualified workers in personal protective equipment (PPE) utilizing portable voltage test instruments. The traditional electrical LOTO process is an administrative control that is inherently manual and relies on detail-oriented workers. However, recent advances in technology make it an ideal time to take a fresh look at this process and examine opportunities to prevent exposure to the electrical hazards encountered during this process.
Substituting a manual process that relies primarily on administrative controls like PPE and training with an automated process that leverages engineering controls designed into a system can provide an enhanced level of safety, increase the reliability of the process and decrease the risk of exposure to electrical hazards. This is critically important, especially for a process that is performed multiple times per day.

This is the idea behind the Absence of Voltage Tester (AVT). The AVT is a permanently mounted tester that can be used to make the verification step safer and less complex. Pushing a button initiates the absence of voltage test from outside the equipment before doors and cover are removed, greatly reducing exposure to electrical hazards. In addition, the AVTs are automated, performing steps that typically take anywhere from 10 to 20 minutes in less than 10 seconds, reliably reducing the many opportunities for human error that exist when using a portable tester.
AVTs are only the first step in innovation to the electrical LOTO and verification process. Although the AVT can be used as a standalone tester for the verification step, some products are equipped with a set of output contacts that allow the AVT to be integrated with other components or automation systems. One example is the combination of the AVT with an electronic lock. When utilized at the control panel or equipment level, this combination can both verify the absence of voltage without exposure to electrical hazards and physically prevent an enclosure from being opened or a manufacturing/robotic cell from being entered until the absence of voltage is confirmed. Bringing access control to the equipment level provides enhanced levels of both safety and security on the plant floor. This approach also reduces downtime, since an electrician does not need to be called to perform the verification step for LOTO applications that do not require electrical work.
New technology often requires changes in behavior and habits, and electrical safety technology is no different. Understanding technology and where best to apply it is crucial to establishing trust and confidence, which will make adoption easier. There are several features to look for when evaluating technology like AVTs and access control to ensure they will be reliable and increase the safety of operations. Look for products that include:
- Active status indicators. Positive feedback that the product or system is working is critical, and active indicators are one way to achieve that.
- Fail-safe designs. The safety functions in electrical products need to be designed so that if they fail, they will default to a safe state.
- Functional safety. Use to prevent and control dangerous failures and to measure the reliability of a safety function with a SIL (safety integrity level) designation.
- Standards. Look for UL listings and to standards like NPFA 70 and 70E for best practices with electrical installations and procedures.
The Significance of Prevention through Design (PtD)
Prevention through Design (PtD), as a principle, is an achievable solution to improve worker health and safety. Reducing hazards before any electrical exposure happens in the workplace should be a top priority for industry safety professionals. PtD includes all efforts to prevent injuries by reducing exposure to hazards primarily through design efforts rather than just administrative controls or personal protective equipment. It applies not only to products and equipment, but also processes and procedures used in the workplace.
With PtD, new technologies and products reduce human exposure to hazards to achieve higher levels of safety, and it makes electrical infrastructure safer to anyone entering the facility for the duration of its lifecycle. Product development by way of PtD can also simultaneously increase productivity, as it encourages designers to consider ways to limit worker exposure to electrical hazards throughout the product lifecycle. This can make both normal operation and maintenance activity faster and less complicated for operators and electrical workers.
It’s important to continually identify and assess potential hazards. As advances in technology occur and new products are released, new ways to mitigate old hazards will become viable. Designed-in control measures are more effective and provide greater business value than other administrative approaches such as training or PPE alone. AVTs and access control are just the beginning of modernizing electrical LOTO.
As companies prepare for the future of electrical safety, the use of Prevention through Design to mitigate risk at equipment or frequently performed tasks will take electrical safety to the next level and prepare them for the advancements ahead.
This article originally appeared in the March 2020 issue of Occupational Health & Safety.