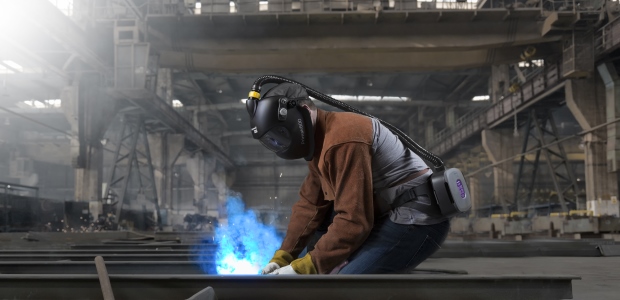
Breathe Easy
Today's welding helmets and PAPR advancements mean that the prospect for worker safety is brighter than ever.
- By Victoria Frank
- Jul 15, 2019
There is no denying it – developments in technology accelerated to near "warp speed" in the 20th century. Thanks to these technological improvements, industrial PPE has significantly improved the life of welders around the globe.
But how did we get here? Advances in the medical sciences have deepened our understanding of the human mind and body, which has helped fuel vast improvements in worker safety.
Today, welding employs approximately 650,000 in North America. Anywhere we see metal formed into a structure, welding was a part of the process. Protecting welders with advances in today's personal protective equipment (PPE) has drastically improved since the old days of single shade filters, metal helmets and welding outdoors to avoid overexposure to fumes.
In the beginning, welding operations assumed the main concern was preserving welders' eyesight. The unprotected eye exposed to the intense brightness of a welding arc was just as dangerous as staring into the sun. Repeated exposure guarantees permanent damage to workers' vision. Dark, single-shade lenses did provide eyesight protection, but they had shortcomings, as well. Welders were still running the risk of accidental flash from other arcs being struck on the production floor.
New Advancements in Welding Helmet Design
One of the biggest and most impactful leaps was in 1981, with the introduction of the first auto-darkening filter (ADF). This filter allowed the welder to go from a less intense filter shade in "rest" state – which would allow more light into the helmet – to a much darker filter shade, which automatically protected the welder when he or she struck an arc. The light state allowed the welder to maneuver and get around without having to flip up the helmet.
Nearly four decades later, next-generation welding helmets are featuring an ADF that offers a "rest" shade of 2.0 – the lightest rest shade the industry has ever seen. This kind of ADF allows much more light in its "resting" state, making it almost like having no filter interference at all. It also allows welders to shift from welding to inspection to grinding without ever having to adjust the helmet or the ADF, which saves time and improves productivity. In addition, these helmet designs have the grinding shield over the ADF, which protects not only the welder, but the ADF itself. The average price to replace an ADF is around $300.
To appreciate the significance of this improvement, realize that some welding helmet manufacturers today still put the ADF on the outside of the helmet, which require welders to flip up the filter. This configuration can have significant impact on the product, the business, and, most importantly, the worker.
Older ADF configurations can result in:
- Potential product damage – Leaving the ADF exposed to damage by striking it against something when it is in the upright position.
- Loss of productivity – Welder may spend precious work time flipping the filter up and down in between welding, inspection, and grinding.
- Harmful exposure to flash – Flipping the filter can also expose the welder to accidental flash – when the unprotected eye is impacted by the arc of a welding torch anywhere within the welder's eyesight.
Adding Respiratory to the List of Protection Factors
Welders' acceptance of protecting their vision has never been a safety challenge. However, what has taken longer to accept and adopt is respiratory protection.
Welders, whether they acknowledge or realize it or not, are exposed to a myriad of contaminants. Depending on the type of welding and chemical reaction between the two metals, contaminants can be gases, vapors, or particulates – and all can be extremely dangerous to inhale.
The most common contaminants are welding fumes, which are considered aerosol particulates. One of the most common welding fumes is hexavalent chromium. Depending on its concentration in the environment, it is recommended for welders to use a tight-fitting mask and a P100 filter. The most popular configuration has been a half-mask with a flat P100 filter, which allows the respiratory protection to go under a welding helmet. Historically, it has been an inexpensive yet efficient respirator choice.
So, you may ask, why is respiratory protection a challenge if it is inexpensive and easy to fix? Well, for several reasons.
Welders may see adding a respirator to their "normal" set of welding equipment as additional time and maintenance that they aren't willing to invest in, even if it is required by OSHA. Plus, tight-fitting facepieces require male welders to give up something they may really love: facial hair. And we're not just talking full beards, mustaches, goatees, mutton chops, or any other deliberate facial hair style. It also means stubble – anything that can interfere with the skin-to-mask sealing area.
Again, thanks to technological advancements, there is a better solution – powered air-purifying respirators (PAPRs) with welding helmets designed with comfortable breathing tubes.
Powered air-purifying respiratory is the same basic concept as air-purifying respiratory (APR). The welder is in a contaminated environment equipped with a mask that seals off the face and prohibits contaminants from reaching the welder's lungs by forcing airflow through a filter on a mask. In APR, the worker uses his or her own lung capacity to draw air through the filter.
However, PAPRs add battery-operated "blower" units and integrated filters that use a motor to draw air through the filters to deliver clean air to the workers. The advantages to this design are less manual filtering work and more continuous air flow while working.
Advantages of PAPR in Welding
There are several advantages to PAPR. First, the wearer does not need to shave, which can really help with adoption and usage. Second, the blower does more than help filter the ambient air. It also provides airflow into the "mask" – which in this case is the welding helmet – and helps keep the welder cool and comfortable. Third, since the blower replaces the worker's lungs as the source of energy, welders' energy is used for welding, not working to filter air.
There are many options when it comes to PAPRs designed specifically for welding. Which one an employer chooses has a lot to do with the functionality and worker preference. Many times, safety directors or site managers will opt for worker consensus, price, and functionality. With the rapid changes and improvements made by suppliers, decision makers should look for what makes the most sense to the organization and train their crews on the benefits of the equipment instead of shopping on price or even sticking with old technology because it is "comfortable."
However, resistance to change is usually driven by lack of education. It is important for those in charge of safety to always be willing to learn and evolve with the technology. For the company, that can mean increasingly optimized worker productivity, and for the worker a more comfortable work experience. No matter what, though, at the end of the day, the purpose and goal for all PPE is to ensure every worker, who also has an important life outside of "the job," returns home safe and sound every day.
This article originally appeared in the July/August 2019 issue of Occupational Health & Safety.