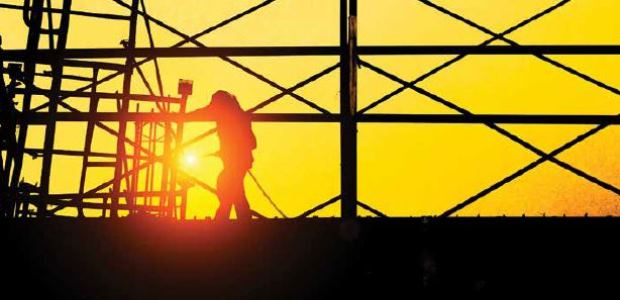
Do You Really Need a 5,000-Pound Anchor Point to Satisfy OSHA?
You may be eliminating perfectly good anchor points where it’s already difficult to achieve proper fall protection.
Anchor point selection can offer limited options when trying to comply with OSHA. For many safety professionals, it is a black and white area that offers no gray option in between. The rule says the anchor point must have the ability to support 5,000 pounds per person attached or it's no good. Is this true, or are you overlooking fall protection solutions typically discarded?
Perhaps the reason that this belief is so widespread is that it's the simplest way to enforce the rule: 5,000 pounds—yes or no? Most people relying on safety personnel to interpret the OSHA standards will think it sounds plausible enough and find ways to be compliant. The catch is, though, that this is not exactly what the standard says. In fact, by following this cut-and-dried rule, you may be eliminating perfectly good anchor points in a situation where it’s already difficult to achieve proper fall protection.
The OSHA standard states:
"Anchorages used for attachment of personal fall arrest equipment shall be . . . capable of supporting at least 5,000 pounds (22.2 kN) per employee attached, or shall be designed, installed, and used as follows: as part of a complete personal fall arrest system which maintains a safety factor of at least two." [29 CFR 1926.502(d)(15) and (d)(15)(i)]
There are various theories as to why OSHA settled on 5,000 pounds. One is that 5,000 pounds is twice the total forces incurred in the free fall of an average worker. A macabre explanation is that the weight was determined by dropping dogs from heights during testing (many years ago). Nevertheless, the regulations have been set forth for decades. In fact, when testing systems under OSHA, you are required to use a weight of 220 pounds (plus or minus 3 pounds) at a free fall of 6 feet [29 CFR 1926 Subpart M Appendix C].
The system would fail the force test if it records greater than 2,520 pounds of force during this test. If the system passes, then, a safety factor of two applied to 2,520 pounds would be approximately 5,000 pounds. However, 5,000 pounds is where many people stop reading. The "or" clause in the above standard often gets missed or ignored.
But why does it matter?
It matters because the forces incurred during a fall of a 220-pound worker who is utilizing a fall arrest system could be between 900 and 1,800 pounds, not 2,500 pounds. Be mindful that fall arrest systems would have some type of deceleration device that engages after free fall and reduces the force. If we look at the "or" clause in the standard and apply the safety factor of two, it means that in this scenario our anchor point may only need to support 1,800 pounds of force.
That's a huge difference from 5,000 pounds. In reality, there may be a number of fixtures in your work area that don't meet the 5,000-pound requirement but may satisfy a 1,800 pounds to 3,600 pounds requirement—a roof truss or a fixed ladder, for example. By eliminating all potential anchorage points that do not meet 5,000 pounds, we may be making a difficult situation unnecessarily more difficult by not installing (or removing) useful protection.
Don't Guess at Capacities and Imposed Forces
This does not mean that we can go tying off to things haphazardly. Whether reducing the capability requirement of an anchor point for use with a fall arrest system or increasing it due to a heavy worker or higher free falls, it is vital that you don’t guess at capacities and imposed forces.
Documentation is vital. Rather than make assumptions, check the manufacturer's paperwork and technical specifications to see what the exact numbers are. If that doesn't provide the answers you need, have a qualified person perform the necessary calculations to determine if what you plan to do is sufficient. (Note "plan to do"—this should always be done before beginning the work).
There is a flip side, however, where 5,000 pounds may not be enough. In some cases, especially where horizontal lifelines are used, the forces applied to the anchors, especially at corners or ends, could be large enough such that 5,000 pounds would not work, or at least not meet the two-times safety factor. In those cases, it's important to use a qualified person to calculate the forces on the system and make sure that the anchors are strong enough and what they are attached to is strong enough also.
You can always choose to keep it simple and stick with the 5,000-pound requirement for your personnel and subcontractors. You would still need to make adjustments for any combined weights 310 pounds and above or for horizontal lifelines. Anybody can choose to go above and beyond what OSHA requires. In this case, going above and beyond could reduce the chance that something is done incorrectly.
Following the regulation as written, though potentially more complex, could possibly open up new, perfectly safe solutions that were never seen before as an option.
This article originally appeared in the March 2018 issue of Occupational Health & Safety.