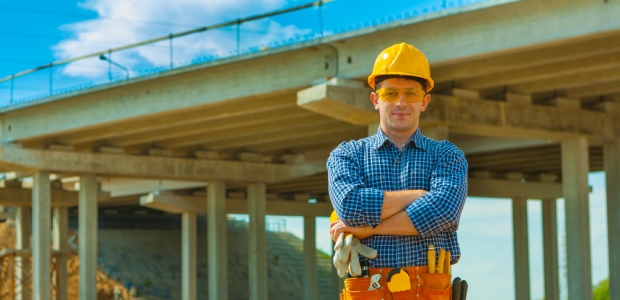
Temp Work More Hazardous, Research Shows
NIOSH's blog highlighted research findings presented during a joint session of the NORA Manufacturing Sector and Services Sector Councils.
A long post to the NIOSH blog on June 16 highlighted research findings presented during a joint session of the NORA Manufacturing Sector and Services Sector Councils about injury frequency and claims of temporary workers. An estimated 17 million workers engaged in some type of temporary employment in the United States during 2013, the largest number for this category of workers in the nation's history, and the research shows temp workers have twice the risk of suffering severe injuries on the job, according to NIOSH.
"There is also evidence that this upward trend [in temporary employment] will continue," according to the post. "Complexities of temporary employment arrangements have created some ambiguity over the responsibility for complying with health and safety standards, which can result in increased health and safety risks in the workplace." It cited two studies that showed temporary workers have higher rates of workplace injury (OSHA, 2013; Fabiano, 2008) and also ProPublica research that found temp workers have double the risk of suffering severe injuries on the job, including crushing incidents, lacerations, punctures and broken bones.
The research presenters included NIOSH employees and Michael Foley, a Services Sector Council member from the Washington State Department of Labor & Industries, who discussed data from the Washington State workers' compensation database that show temporary workers have higher claim rates in certain industries compared to permanent workers. Differences in machine operations, vehicle operations and construction were most notable, according to NIOSH.
Steve Wurzelbacher and Chia Wei from the NIOSH Center for Workers' Compensation Studies discussed comp claim frequency and injuries among temporary manufacturing workers, using data from the Ohio Bureau of Workers' Compensation. Industry groups with the most claims were manufacturing, commercial, and services.
Other presenters included two from staffing companies: Cheri R. Duggan, senior regional safety, health & environmental manager for Kelly Services, and Kristen Schweizer of The York Companies, Inc., who discussed these best practices to minimize risks and exposures for contingent employees:
- Safety must be a priority of senior management.
- Provide continual training at all levels.
- Participate in "captive insurance" for workers' compensation, which is an arrangement under some states' workers' compensation systems where a group of staffing agencies share risk and assist others toward best practices.
- Partner with client companies to clearly delineate co-employment of workers.
- Perform pre-agreement and quarterly safety evaluations of client companies and contingent employee job functions.
- Conduct an in-depth analysis of every incident and accident.
Ken Rosenman of Michigan State University discussed a needs assessment done of the 304 temporary service agencies in Michigan. More than half of the respondent agencies provided training on general procedures, ergonomics, hazard communication, lockout/tagout; and PPE; more than half of them indicated that they had a contract with the host employer specifying safety and health responsibilities; and 90 percent said they visit a work site prior to placing temporary employees at a company, he explained.