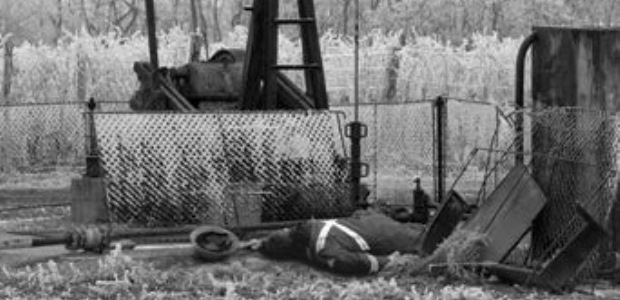
Five Common Safety Practices That Are Putting Your Workers at Risk
Buddy systems can increase complacency of workers in the field due to a false sense of greater safety.
- By Garrett Genest
- Jul 01, 2014
Every day, people go to work with the expectation that they will get home safely at the end of the day. To meet these expectations, businesses deploy various techniques and equipment to help keep their employees safe and healthy, such as providing training or mandating the use of personal protective equipment. While many of these methods have improved safety, there are others in use almost universally that actually heighten employees' risk of injury or death.
Using a Phone to Check In or Monitor the Safety of Your Employees
Chances are, if you have employees working alone or in isolation, you've made every effort to ensure that they carry a phone or smartphone at all times. While communication is the key to discovering an emergency, phones require the user to be able to see the device and dial a number. Workers who are severely injured, blinded, or incapacitated may not be capable of reaching for their phone and requesting aid manually. Additionally, phones do not offer much help when an employee is not able to manually request help.
Responding to an Emergency As Soon As a Check-in is Missed
Many businesses require their employees to check in every one or two hours. If a worker misses a check-in, managers attempt to contact the missing employee and, failing that, a search is mounted and emergency responders are contacted. The problem with this model is that an injured or distressed worker might be slumped on the ground in a field, unconscious, suffering from a heart attack or stroke, for as much as an hour or two before anyone even realizes that something is wrong. Those precious minutes (or hours) that are lost can mean the difference between life and death. Beyond being ineffective, these check-in solutions become a productivity drain on organizations as workers spend increasing amounts of time performing their routine check-ins rather than working.
Relying Entirely on PPE
No one is arguing the value of PPE, but relying too much on gear to prevent injuries without paying attention to the possibility that injuries can (and probably will) continue to occur can be a lethal oversight. Workers can suffer heart attacks, strokes, be overcome by gases, or suffer any number of other incidents in which PPE may not be enough to ensure they get home safely at the end of the day. When a safety incident occurs, the overall safety investment, including PPE, has failed to avert the situation. What occurs next may hold the employee's life in the balance.
Employing a 'Buddy System' to Keep Your Employees Safe
If someone asked you to double the salaries of your employees with minimal expectations of improved productivity or safety, would you do it? Probably not—yet, very often when businesses deploy buddy systems for safety, they are doing just that. Maintaining a buddy system means your business needs to pay two people often to do the work of one. The idea behind this type of system is that should something happen to one employee, the other one can call and request help… but what happens if both employees suffer the same incident or are rendered incapacitated? Larger events such as gas leaks, explosions, and vehicle collisions do not discriminate based on the size of the team. To make matters worse, buddy systems can increase complacency of workers in the field due to a false sense of greater safety.
Performing a Facility Sweep to Find Injured Employees
When the alarm goes up inside a facility, operations stop and every available hand is often pulled from the floor to help find the injured or distressed employee. Aside from the interruption in operations, the business spends precious time searching for the injured worker. Because searchers must spend time looking in every possible area, minutes and even hours can be lost while searching. Every minute that passes while the searchers wander about increases the risk of a worse outcome for the employee's health.
One Best Practice to Replace Them All
Recent advances in technology have given us the key to avoiding the use of these risky techniques through automation, instant alerting, and built-in fail-safes to mitigate as much risk as possible. This evolution in safety has emerged as "employee safety monitoring," often known as "lone worker safety monitoring." Utilizing automated safety monitoring devices, managers can finally discover emergency incidents right away.
Unlike phones, employee safety monitoring devices are designed for one purpose: to monitor and report on the safety of your employees. These devices simplify the alerting process by eliminating the need to pull out a phone and dial a phone number, instead triggering an immediate alert in the event that a worker is rendered unconscious or suffers a slip, trip, or fall. Unlike a phone-based check-in, these devices also will monitor worker safety in between check-ins. If a worker suffers an incident, he or she won’t need to wait for the check-in timer to count down before help is sent out. In addition, some employee safety monitoring products include indoor location technology, allowing employers to find injured workers located within a facility with pinpoint precision. This eliminates wasted time spent search the entire facility; it can not only improve the potential outcomes for injured employees, but also reduce operational downtimes caused by extensive facility sweeps.
Safety managers can complement their investments in PPE by putting in place these automated alerting systems that notify them when an emergency does occur. Receiving and responding to an emergency alert immediately can significantly improve the chances of a better outcome in the event that a piece of PPE is not enough to prevent an injury.
This article originally appeared in the July 2014 issue of Occupational Health & Safety.