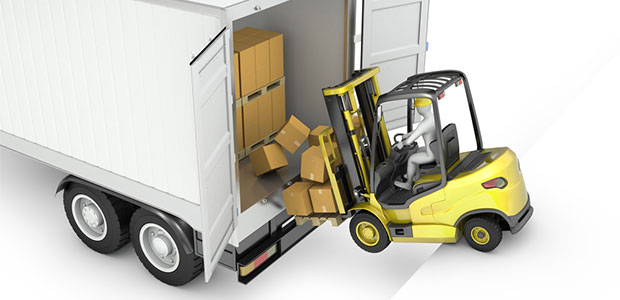
Death by Forklift is Really the PITs
Powered Industrial Trucks are critical to many industries. By implementing a forklift safety program and effective training, you can ensure that this asset doesn't become a liability.
- By Chuck Paulausky
- Sep 01, 2013
The owner of a machinery and equipment training school was killed while filming a forklift safety video. He was thrown from the forklift and crushed. The investigation revealed the fatality was due to driver error, high speed over rough terrain, and an unused seat belt. Unfortunately, this type of forklift fatality is all too common. OSHA statistics indicate that there are roughly 85 forklift fatalities and 34,900 serious injuries each year, with 42 percent of the forklift fatalities from the operator's being crushed by a tipping vehicle.
The safest place for the driver to be is strapped into the seat with a seat belt. According to OSHA, its enforcement policy on the use of seat belts on powered industrial trucks is that "employers are obligated to require operators of powered industrial trucks which are equipped with operator restraint devices or seat belts to use the devices." Compliance officers will enforce the use of such devices under Section 5(a)(1) of the OSH Act, the General Duty Clause.
OSHA has established detailed regulations for operation of "powered industrial trucks," which include all types of material-handling vehicles, from forktrucks to powered pallet jacks to order-pickers. The Powered Industrial Truck (PIT) regulations can be found at 29 CFR 1910.178. Incorporated into the regulation by reference, ANSI B56.1-1969 covers the design and construction requirements for PITs.
The OSHA regulation provides specific designations for PITs based on the type of power source and safeguards. In addition, "designated locations" are identified, such as hazardous atmospheres. The regulation also covers a variety of other topics, including operation, maintenance, and regular, documented inspections of the vehicles. One critical part of the regulation covers operator training.
PITs can be especially unforgiving under the wrong conditions. Operators need to understand that PITs are very different from regular vehicles in the way they maneuver and are balanced. Employees who have never driven a PIT will not have the innate knowledge and skill to drive one without training. For this reason, much of the required training is focused on operation, load capacity, stability, and operating limitations.
Some of the key factors that should be covered to help operators understand technical aspects of forklift operation include:
- Center of Gravity: The size and the center of gravity of a load can directly affect the safe lifting capacity of the PIT. Positioning the center of gravity as close as possible to the center of the PIT will help keep the vehicle from toppling sideways, especially when turning.
- Load Center: The load center relates to the distance of the center of gravity from the vertical face of the forks. Keeping the load as close as possible to the vertical face will help keep the load from overcoming the counterweight at the rear of the vehicle and causing it to tip forward. Simple calculations can be used to determine whether a load can be handled by a particular forklift: Capacity x rated Load Center = Maximum Allowable Inch-Pounds. Dividing this by a load's actual load center will tell you the maximum allowable weight for the load. For example, let's say a forklift has a 4000-pound capacity with a 24-inch load center. The Maximum Allowable Inch-Pounds is 96,000 in-lbs. Suppose a load has a 30-inch Load Center. Dividing 96,000 by 30" results in 3,200 pounds, the maximum the load can weigh to be safely lifted by this forklift.
- Stability Triangle: This is a triangle formed by the front axle and the rear center point inline with rear axle. The combined center of gravity (load center plus vehicle center of gravity) must stay within the stability triangle to maintain stability. Speed of travel, centrifugal force from turning, load height, mast tilt, ground slope, and various other factors also will affect the location of the combined center of gravity.
Site-Specific Training is Required
Operators must receive training for each type of PIT they will be operating, including the use of any attachment (e.g., manlifts, drum attachments, etc.). The training also must include the conditions under which the vehicle will be operated, such as surface conditions, ramps and slopes, hazardous locations, visibility, and pedestrian traffic. Because these factors are different from workplace to workplace, OSHA requires the training to be site-specific.
Training must be conducted by "persons with the necessary knowledge, training, and experience to train powered industrial truck operators and evaluate their competence." The training must include both formal instruction and practical driver training. Trainees also must be evaluated initially and every three years thereafter to establish that they are qualified to operate the equipment safely.
Refresher training is required: (1) whenever an operator is observed operating unsafely, (2) when an operator receives an unsatisfactory evaluation, (3) when an operator is assigned to a different type of PIT, and (4) when changes in workplace conditions could affect safe operation. As with any OSHA-required training, the training and evaluations must be documented.
The use of Powered Industrial Trucks is critical to many industries. By implementing a forklift safety program and effective PIT training, you can ensure that this asset doesn't become a liability.
Stay Safe!
This updated article was originally published in the June 2008 issue of the Journal of Environmental Management-Arizona.
This article originally appeared in the September 2013 issue of Occupational Health & Safety.