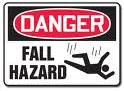
Know the Requirements for General Industry
General industry fall protection can be a real challenge.
Workplace falls continue to be a serious safety concern for employers. This is due to the fact that injuries resulting from falls often affect multiple body parts and require longer recovery times. Although there are many factors that contribute to workplace falls, such as wet floors, poor lighting, cluttered aisles, and improper use of equipment, most injuries are the result of falls to a lower level.
In fact, the U.S. Bureau of Labor Statistics data has revealed that falls to a lower level have been the most frequent type of fatal fall in the workplace, with a majority of those caused by falls from roofs, followed by ladders, scaffolds, non-moving vehicles, and building girders or other structural steel. OSHA has said such data demonstrate that fall protection safeguards have been absent, ignored, or inadequate.
What can employers do to protect employees from falls at elevated heights? They can provide fall protection. Fall protection systems serve one of two basic functions:
- Prevent or restrain a worker from falling
- Safely stop or arrest a worker who falls
For general industry, the trigger height for providing fall protection is 4 feet (with exceptions for construction, scaffolding, fixed ladders, dangerous equipment, and utility work). Throughout its entire history, OSHA has consistently reinforced this policy in public statements, as well as in documents issued to clarify and interpret the standard. As far back as 1978, the agency issued a Letter of Interpretation (LOI) on the "four-foot" requirement for fall protection.
What type of fall protection must be used? There are various options for employers. Regardless, each type must adhere to specific construction and use requirements in order to provide employees with the required and necessary protection.
Guardrails
Guardrails -– also called standard railings -– are the primary means of preventing employees from falling to lower levels in general industry as required under 1910.23(c). Specifically, all platforms 4 feet or more above the adjacent floor or ground must be protected by a standard guardrail on all open sides. This includes mezzanines, loading docks, roofs, etc. In addition, toeboards are often necessary to prevent the fall of materials to a lower level and to keep an employee's feet from slipping over an edge.
Under 1910.23(e)(1), OSHA says that a guardrail must have a vertical height of 42 inches nominal from the upper surface of the top rail to floor, platform, runway, or ramp level. "Nominal" simply means that 42 inches has been established as the de facto standard for guardrail height. OSHA allows for variance, however. Standard Directive 1-1.10 says existing guardrails must consist of a top rail, intermediate rail, and posts, or equivalent, and have a minimum vertical height of 36 inches to 44 inches.
Also, guardrails with heights greater than 44 inches are permissible, provided the extra height does not create a dangerous situation for employees. Openings beneath the top rail that would allow the passage of a 19-inch or larger spherical object would create an unsafe condition. In that case, OSHA says that additional mid-rails might be necessary.
It's important to understand that while variance is allowed, it's not exactly what OSHA requires per the standard. For this reason, the agency says that any guardrail which does not have a vertical height of 42 inches would be cited as a de minimis violation (meaning there is no monetary fine).
Safety Chains
Sometimes the installation of a guardrail isn't feasible or practical. One solution frequently considered is the use of safety chains, but are they allowed by OSHA? Even though the agency does not specifically address the use of chains in the Walking-Working Surfaces Standard, the agency has issued two LOIs on the issue that provide further guidance.
In the first letter, dated Feb. 12, 1982, OSHA makes mention of chains with regard to safety gates by saying, "if in fact the safety chains used for top and intermediate rails afford employees protection 'at least as effective as' the swinging gate, the safety chains would be adequate and noted as a de minimis violation."
This is further supported by a June 3, 1983 LOI, which says that "the anchoring of posts and installation of chains for railings must be of such construction that the completed structure shall be capable of withstanding a load of at least 200 pounds applied in any direction at any point on the top rail."
The bottom line is that if safety chains provide the same level of protection as a standard guardrail, they can be used.
Handrails and Railings
A handrail and a guardrail are not the same thing. There are three definitions for the term "handrail" in the standard, but in simplest terms, a handrail is a single bar or pipe supported on brackets from a wall or partition. Handrails literally provide a handhold for support to assist employees going up or down stairways, ramps, or other walking/working surfaces. Railings, on the other hand, protect employees from falling over the edge of an open-sided stairway.
Under 1910.24, OSHA prescribes the use of handrails and railings as fall protection. Paragraph (h) says that standard railings must be provided on the open sides of all exposed stairways and stair platforms. Handrails have to be provided on at least one side of closed stairways. In addition, both railings and handrails must be installed in accordance with the provisions of 1910.23. These requirements are dependent upon stairway width and the number of closed sides for every flight of stairs having four or more risers. For example, on a stairway more than 44 inches wide but less than 88 inches wide, there must be one handrail on each enclosed side and one stair railing on each open side.
Hole Covers
Depending on the type and size of a floor hole or opening, OSHA says they must be guarded by a cover, screen, or fixed standard railing with a toeboard to prevent falls to a lower level. These requirements are outlined in 1910.23(a). For example, every skylight floor opening and hole must be guarded by a standard skylight screen or a fixed standard railing on all exposed sides.
The standard also says that for some floor holes and openings, such as a manhole, the opening has to be constantly guarded by someone or by a removable standard railing -- but this is only for when the cover isn't in place. Again, certain floor openings and holes must be guarded with a cover first and foremost. Employers need to carefully review the requirements to make sure that each opening is correctly guarded in their facilities.
Ladder Cages and Wells
All fixed ladders of more than 20 feet to a maximum unbroken length of 30 feet must be equipped with a cage or well as prescribed under 1910.27(d) (the length of measure is based on the length of the ladder, not the start of the climb). Cages are fastened to the ladder's side rails enclosing the employee in the climbing area of a fixed ladder. To help employers understand design, clearance, and other construction requirements, numerous diagrams are provided as examples in the standard.
If the fixed ladder is less than 20 feet, OSHA does not require the use of fall protection. However, if a fall hazard(s) exists, employers must assess the situation and circumstances to determine whether fall protection is warranted. In those cases, personal fall protection may be necessary.
Personal Fall Protection
Another means of fall protection includes personal fall arrest systems to stop an employee after a fall from a working level. These are widely used in the construction industry, but OSHA only specifically permits their use in general industry under the standard for powered platforms for building maintenance. Again, OSHA generally requires the use of guardrails as fall protection.
While the vast majority of systems in use now meet national consensus standards, OSHA says if a personal fall arrest system has to be used, it must consist of an anchorage, a connector, and a body harness. The arrest system also may include a lanyard, deceleration device, lifeline, or a combination of the above.
As stated, OSHA only outlines general industry requirements for personal fall arrest systems under Appendix C to 1910.66, which requires that anchorages to which personal fall arrest equipment is attached be capable of supporting at least 5,000 pounds. Appendix C also states that personal fall arrest systems must bring an employee to a complete stop and limit maximum deceleration distance an employee travels to 3.5 feet. Again, fall protection is required at 4 feet in general industry. That's why the required stopping distance is 3.5 feet.
While these requirements are for powered platforms used for building maintenance, they provide valuable guidance to general industry employers.
Elevate Your Safety Program
General industry fall protection can be a real challenge. First, identify the fall hazards in your facility that must be eliminated. Then implement the fall protection that not only meets OSHA requirements, but elevates your safety program by also best preventing workplace falls.
About the Author
Jennifer Stroschein joined J. J. Keller & Associates, Inc. in 1998 with a BA in Environmental Studies and Biology and expertise in regulatory compliance with federal regulations and standards. As Editor – Workplace Safety, she is responsible for providing timely, accurate information and technical support to workplace safety professionals regarding a variety of issues. Her areas of specialty include safety incentive programs, audits and inspections, walk-working surfaces, and pandemic preparedness.