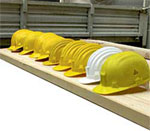
Wearing a Hard Hat is Only Half the Job
Inspections are essential to ensure this vital type of PPE can do its intended job.
- By Michael Lloyd
- Mar 01, 2007
MILLIONS of hard hats are worn every day. In fact, the hard hat is one of the most recognizable pieces of safety equipment in the industrial workplace. It's also one of the most important pieces of safety equipment because it protects the brain. Unfortunately, this ubiquitous piece of personal protective equipment (PPE) is rarely part of an inspection, maintenance, or replacement program.
undefinedMany workers may be wearing a hard hat well past its useful life without even knowing it.
The durable exterior of the rugged-looking hard hat can disguise the need for replacement. Hard hats must be replaced when they can no longer provide the protection intended, and sometimes this can be difficult to detect. Workers who use gloves on a work site can obviously see (and feel) the need for new gloves; the wear and tear is readily apparent. On the other hand, many workers may be wearing a hard hat well past its useful life without even knowing it. In every organization where workers wear head protection on the job, a regular hard hat replacement program should be clearly defined and implemented. This type of hard hat replacement program can be implemented and managed with a few considerations.
OSHA, ironically, does not specify the service life of a hard hat, and there is no standard expiration time frame for hard hats. The hard hat manufacturer can recommend a replacement guideline for its products, but hard hat life span may vary significantly based upon the conditions at each work site. Ultimately, an employer is responsible for defining a responsive and appropriate solution for hard hat service life issues.
Useful Life of a Hard Hat
Determining a specific time frame for hard hat replacement at your site will take some research. As a general guideline, most manufacturers recommend replacing hard hats every five years regardless of outward appearance. If work conditions include exposure to higher temperature extremes, sunlight, or chemicals, hard hats should be replaced after two years of use. Some manufacturers recommend the replacement of the hard hat suspension every 12 months, regardless of appearance. Careful review of each work site is critical to ensure that degradation of PPE is not being accelerated due to extreme work conditions.
Inspection and Maintenance
The typical ANSI Type I-compliant hard hat, which provides protection from objects striking the top of the head, consists of two components: shell and suspension. These components work together as a system. It is important for both the shell and suspension to be inspected on a regular basis.
Shell Inspection
Throughout history, many materials have been used to manufacture hard hat shells. Today, thermoplastics (polyethylene, polycarbonate, and others) and thermoset materials (fiberglass-reinforced polyesters and phenolic-impregnated textiles) are commonly used to mold shells of industrial hard hats. These materials have proven to be durable, reliable, and lightweight while providing effective protection. Given proper care, these materials will provide a reasonable service life under normal workplace conditions. But remember, these hard hats do not have an indefinite useful life, nor are they resistant to all physical and chemical exposures.
Regardless of the material, shells should be inspected routinely for dents, cracks, gouges, and any damage due to impact, penetration, abrasions, rough treatments, or wear that might reduce the degree of protection originally provided. Degradation of thermoplastic material may be apparent when the shell becomes stiff, brittle, faded, dull in color, or exhibits a chalky appearance. A hard hat should be replaced at first sign of any of these conditions.
undefinedCareful review of each work site is critical to ensure that degradation of PPE is not being accelerated due
to extreme work conditions.
Exposure to direct sunlight will affect the life of the shell. Although most manufacturers add an ultraviolet inhibitor to the shell material of hard hats to protect against degradation caused by sunlight, all hard hats are susceptible to ultraviolet light damage. Workers should never store their hard hats in the rear window or dash of a vehicle or in direct sunlight. This is the quickest way to degrade the shell material and reduce the life of the product.
Suspension Inspection
The hard hat suspension is just as important to worker safety as the shell. The suspension actually helps to absorb the shock of a blow, so it must be in good condition at all times. Like the shell, the suspension must be inspected regularly and replaced from time to time. Suspensions should be inspected closely for cracks, frayed or cut crown straps, torn headband or size adjustment slots, loss of pliability, missing components, or other signs of wear. These conditions can be caused by perspiration, hair oils, or normal wear.
Maintenance
As with everything on the work site, hard hats will get dirty. The hat and suspension should be cleaned with mild soap and lukewarm water. Strong detergents, solvent chemicals, gasoline, and other like substances could affect the resistance and other such properties of the hat over time. Contact the manufacturer if you have concerns.
General Guidelines
All new employees should be provided with a new, unused, and unexposed hard hat. The practice of reissuing cleaned hard hats must be avoided. The cost of a hard hat is negligible when the potential for injury, lost time, health care costs, and liability are considered.
- Hard hats are designed to protect you only once. If the hard hat has been struck by a forcible blow of any magnitude, both the hard hat shell and the suspension should be replaced immediately, even if no damage is visible. Hard hats also should be replaced if dropped accidentally by the worker from the height of a two story building or higher. Damage to the hat and suspension from the drop could seriously degrade the effectiveness of the product.
Assuming the hard hat has been stored in proper packaging--free from exposure to sunlight, chemicals, and extreme temperatures--the product service life would begin at the time the hard hat is put into service, not from the date of manufacture. Be sure to check with the manufacturer about product warranty because it may not allow for storage time. All hard hats have a molded-in date code (date of manufacture) per ANSI Z89.1-2003 industrial head protection requirements. These date codes are usually located on the underside of the shell. Check and log this date prior to sending the hard hat into service to help track the age of the product.
- Supplying and enforcing the use of hard hats is only half the job. Safety officials must implement and maintain a hard hat replacement program to ensure that hard hats are providing the level of protection intended. This is not only necessary, but well worth the effort when considering the implications of providing a hard hat that has outlived its usefulness. Check with the hard hat manufacturer for additional tips, guidelines, and warnings.
This article appeared in the March 2007 issue of Occupational Health & Safety.
A Field Test for Your Hard Hat
The following is a simple field test that can be performed by an employee or supervisor to determine possible degradation of polyethylene shells:
Compress the shell inward from the sides about 1 inch (2.5 cm) with both hands and then release the pressure without dropping the shell. The shell should quickly return to its original shape, exhibiting elasticity. Compare the elasticity of the sample with that of a new shell. If the sample does not exhibit elasticity similar to that of a new shell or if it cracks due to brittleness, it should be replaced immediately.
This article originally appeared in the March 2007 issue of Occupational Health & Safety.