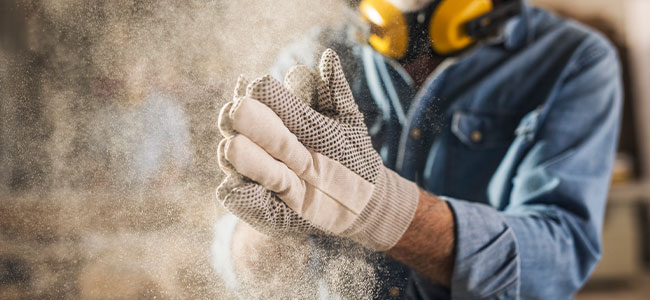
How to Safely Work With Combustible Dust
The strategies for managing combustible dust in and around manufacturing plants and processing facilities.
- By Brian Richardson
- May 01, 2024
If your manufacturing or production processes generate airborne particles, you (should) know that handling combustible dust is a challenging responsibility. However, you can implement effective measures to mitigate risks and safeguard operations despite the potential hazards. Through meticulous planning and keen attention to detail, you can reduce the dangers associated with combustible dust. Understanding the factors that contribute to explosions, as well as developing and executing a comprehensive safety protocol, can help you to manage the potential for harm to personnel and property.
This article examines the strategies for managing combustible dust in and around manufacturing plants and processing facilities. Armed with this knowledge, you can quickly identify unsafe conditions in the work environment, assess the risk posed to employees and determine appropriate actions to enhance workplace safety.
What Causes a Dust Explosion
When fuel, confinement, dispersion, oxygen and ignition come together, a dust explosion is looming. Dust is the fuel. Conditions for a dust explosion arise when a confined and concentrated combustible dust cloud encounters an ignition source. While activities such as vacuuming aid in dust removal from surfaces, an effectively designed and installed industrial dust collection system is essential for comprehensive threat mitigation, particularly for airborne particles.
However, it’s crucial to recognize that while extracting combustible dust from the air, a dust collector itself can pose a risk from dust explosions if not equipped with adequate safety features. Merely by functioning, a dust collector establishes conditions where four of the five elements necessary for an explosion come together.
As dust is drawn into the collector, it becomes confined. The pulse cleaning system, which utilizes compressed air to dislodge dust from the filter cartridges, will disperse dust into the airstream, forming a cloud. Subsequently, the dust mixes with oxygen-rich air, setting the stage for an explosion. All you need is an ignition source, like a spark, to enter the collector, causing pressure within to escalate rapidly. Without suitable explosion protection measures, the housing may rupture, unleashing a pressure wave along with heat, flames and hazardous projectiles into surrounding work areas.
A dust collector conforming to National Fire Protection Association (NFPA) standards and meticulously designed, sized and installed to suit the requirements of a particular manufacturing or processing facility provides optimal defense against dust fires and explosions. NFPA 652 Standard on the Fundamentals of Combustible Dust mandates that all facilities engaged in the production or handling of combustible dust must undertake a dust hazard analysis to adhere to OSHA regulations. (Note that the NFPA is currently working toward consolidating its six separate combustible dust standards into one, which will be named NFPA 660 Standard for Combustible Dusts.)
Combustible Dust Incident Statistics
Comprehending the materials commonly involved in dust explosions and fires is essential for ensuring workplace safety. According to the most recent data from DustEx Research Ltd., between January 1, 2023, and July 1, 2023, there have been 159 fires, 32 explosions, 71 injuries and 48 fatalities related to combustible dust around the world. Food, metals and wood processing resulted in 82 percent of the injuries and 52 percent of the fatalities. Incidents also occurred at facilities that handle pulp and paper, rubber, lawn products, graphite and carbon, pharmaceuticals, plastics and waste treatment. Dust collectors accounted for 11.5 percent of incidents in Q1-Q2 2023.
Loss history data from dust explosions in the United States from 2016 to 2023 shows an average of 28.4 combustible dust explosions per year, 28 injuries and 3.5 fatalities. This analysis does not include dust fires.
Recognizing the Danger
It is important to be able to identify and recognize the dangers in and around your facility when it comes to dust-generating manufacturing or storage processes. There are many key indicators that you have a potential problem, such as dim lighting due to dust floating in the air, piles of dust around the processes from leaking duct work or containers, and dust thicknesses of 1/32 of an inch (the thickness of a dime) on surfaces around the facility.
Keep in mind there may be hidden areas on top of machines, duct work, ceiling joists or suspended ceilings, just to name a few, that may be hiding those dangers if not inspected properly. If you are performing cleaning tasks in areas such as these with air wands, compressed air or even brooms, you may be adding to the danger by dispersing dust into unseen areas. These cleaning methods can even create dust clouds outside of a dust collection system, which creates an even more hazardous situation.
Steps to Make Your Facility Safer
While some dust-related accidents may be unavoidable, their consequences can be mitigated, and many incidents can be prevented through proper education, planning and equipment. This underscores the importance of implementing a combustible dust management program in every facility that generates airborne particles.
The primary aim of this program is to safeguard individuals from the hazards of fire, deflagration and explosion, allowing time for evacuation, relocation or seeking refuge. While preventing ignition remains paramount, in the event of a fire or combustible dust incident, the primary objective shifts to safeguarding individuals outside the immediate vicinity of the ignition and preventing structural damage to the building that could endanger evacuating occupants.
Combustible Dust Management Program
A combustible dust management program constitutes a structured strategy for addressing hazards within the facility. While the particulars of such a safety program may vary depending on the processes involved at the plant, it should encompass the following fundamental components:
• Management of change program —
A structured procedure guided by the findings of the dust hazard analysis that delineates how to address all necessary changes to achieve the life safety goals. It outlines the methodology for implementing, overseeing and adapting the components of the combustible dust program as necessary.
• Facility analysis —A strategy aimed at identifying both visible and concealed areas prone to the accumulation of combustible dust, assessing mechanisms for dispersal into the air, and pinpointing potential sources of ignition
• Process hazard analysis —This is required on each process point generating dust in a facility. OSHA will ask for this when investigating combustible dust processes. The plan must detail how to remove the dust hazard from each process point.
• Hazard mitigation —A detailed strategy outlining measures to mitigate combustible dust hazards at each operational point. This entails addressing heat sources near areas susceptible to dust accumulation. These could include friction heat from adjacent equipment, static electricity, open flames, sparks, smoking, faulty wiring or electrical equipment malfunctions. Note that colder weather elevates the risk of static electricity.
• Housekeeping plan —A strategy outlining cleaning processes to control the buildup of combustible dust.
• Maintenance and inspection —A continuous regimen aimed at ensuring equipment functions properly and adheres to pertinent regulations.
• Employee training —Continuous education encompassing facility protocols for managing ignition sources and dust hazards. This training should cover identifying potential hazards, reporting procedures to management, determining when preventive measures are necessary and mitigating potential disasters. Managers and supervisors should receive training on effectively processing information from employees to promptly address unsafe practices
In Summary
Combustible dust hazards demand serious attention — and a dedicated management program. Equipping your team with the ability to identify warning signs of potential dust explosions, effectively addressing these issues and implementing appropriate controls and procedures are crucial for maintaining a safer facility. Consistent housekeeping practices and utilizing a properly designed dust collection system tailored to your specific operation can greatly diminish airborne dust levels in the workplace and mitigate the risk of fire and explosion.
This article originally appeared in the April/May 2024 issue of Occupational Health & Safety.