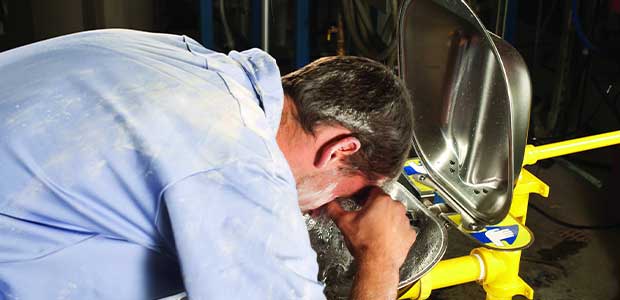
Five Common Pitfalls to Avoid with Emergency Safety Showers and Eyewashes Gas
Don’t let these common mistakes allow your emergency equipment to suffer.
- By Ryan Pfund
- Aug 01, 2022
Worksite hazards involving harmful chemicals, dusty conditions and flammable materials present fluctuating risks and challenges to employees. While emergency safety showers and eyewashes can help abate these hazards, there are unfortunately several common areas involved with the installation, operation and maintenance of emergency shower equipment that can fall by the wayside and hinder their performance in an emergency.
Specifically, it’s crucial to regularly evaluate—and recheck—the performance, placement and sterility of equipment to ensure ANSI/ISEA compliance and efficacy when needed.
The following are some of the most common mistakes made with emergency equipment, along with strategies for avoiding them in the first place:
Failing to Perform Weekly Testing and Activations
According to ANSI/ISEA Z358.1–2014 American National Standard for Emergency Eyewash and Shower Equipment, emergency drench showers, eyewashes and eye/face washes must be activated one time per week. Weekly testing and activations may seem like time-consuming and laborious tasks but they are just as important as they are necessary.
Safety equipment must work properly in supplying tepid water when needed. Unless the product is activated on a weekly basis, water stagnating in the supply piping may not be clean. Weekly activation ensures the product is properly functioning and safe for the person to use when needed. This activation makes sure that nothing is blocking the flow of the flushing fluid and eliminates any chance of contamination from stagnant water. The fixture needs to be activated long enough to ensure proper flushing fluid is available and to clear the line of any sediment build-up. (A longer and more thorough evaluation should be conducted once per year.)
Inspection tags are often included with fixtures to document testing and to satisfy a safety audit. To further help assist in testing, manufacturers offer a variety of specially designed devices.
Neglecting to Check Proper Locations of Emergency Eyewashes and Showers
At least yearly, it’s important to conduct site evaluations to pinpoint at-risk areas, potential hazards and emergency needs. In particular, pay attention to product location relative to hazards to ensure they are easily seen and accessed.
Consider these guidelines, which reflect the ANSI/ISEA Z358.1-2014 standard:
- Fixtures must be within 55 feet of a potential hazard and take no more than 10 seconds to reach. Access to the fixture must not be obstructed.
- Equipment must be on the same level as the hazard. A door can be considered an obstruction; however, if the hazard is not caustic, one door can be present provided it swings in the direction of travel and it cannot be locked.
- The height of the eyewash flow pattern should be between 33 and 53 inches, and measured from the floor to the water flow.
- If a potential chemical spill in an area can affect multiple workers, enough fixtures should be in place for all to access.
- If corrosive chemicals are used, the drench shower or eyewash should be placed immediately adjacent to the hazard.
- All equipment must be identified in a well-lit area with highly visible signage, e.g., bright yellow; fixtures should be able to be activated in less than one second.
Conducting a walk-through of facilities with a health or safety expert can help determine proper placement and types of fixtures for each location. Manufacturers often conduct free site surveys to ensure proper placement and other best practices for ANSI/ISEA compliance.
Inability to Provide Tepid Water for ANSI-Required 15-minute Drenches
According to the current revision of ANSI/ISEA Z358.1, water supplied to eyewash and drench showers needs to be potable and tepid. Tepid water is defined as 60-100 degrees Fahrenheit or 16-38 degrees Celsius. This temperature will need to be present throughout the entire 15-minute drench. The cold supply may seem warm enough at first activation because the water in the supply line is at room temperature but eventually over the 15-minute drench it will likely turn to a colder ground water temperature. Using a dependable delivery system of tepid flushing fluid encourages a full 15-minute flush of the injured area.
Using technology such as thermostatic mixing valves or electric tankless water heaters helps ensure that tepid water is supplied in a dependable and efficient manner for the entire 15-minute duration.
Dirty or Unclean Eyewash and Drench Showers
It’s important to keep eye/face wash systems clean and bacteria-free. Compounding the problem is that when the product isn’t activated on a weekly basis, stagnant water can harbor bacteria or sediment that you would not want to enter the eyes during use.
While facility managers can avoid false activation issues by installing an eyewash alarm system, newer eyewash designs come equipped with either plastic or stainless-steel bowl covers that shield the entire bowl from misuse and contamination. The see-through plastic allows for quick and easy visual inspection and the hinging mechanism provides a more secure hold. The fixture is activated as the cover is opened and may be installed on barrier-free fixtures.
As discussed above, weekly testing and activations provide the opportunity to clear settled water in the line, among other harmful bacteria.
One of the newer eye/face wash models comes equipped with a self-draining design that eliminates any settled water in the system. This model also incorporates separate supply and waste pipes to prevent cross-contamination from the clean inlet and wastewater.
Overlooking Proper Employee Training
Unfortunately, training employees can fall by the wayside during busy times and get lost in the shuffle of employee turnover. Even the best emergency safety plan cannot be successful without educating and training employees on the correct use of equipment and where they are located. Ultimately, training can make the difference between a bad and good outcome when an employee is contaminated with an injurious material.
Safety experts emphasize that when spontaneously forced to deal with physical pain from an injury, the human instinct is to panic and run away from it or even run to the bathroom and try to wash it off. The best antidote to the “fight or flight” response is regularly educating employees and giving them hands-on training and experience in using safety showers and eye washes. Ultimately, the more management explains the safety framework and procedures, and develops the habit of using the fixtures, the better equipped—and more successful—workers will be in the event of an emergency.
For example, key safety concepts to cover in training may include:
- Training employees to protect themselves first before helping others
- Removing any barriers between the injured and the safety fixture
- If clothing is in the way, using safety shears to remove it—don’t pull a shirt over the face, which may spread the contaminant
- How to alert co-workers and medical personnel to locate when and where an accident occurred and respond immediately—whether by yelling or using an emergency signaling system with a visual, audible and auxiliary connection
For assistance with training or developing a company’s safety plan, manufacturers offer complimentary safety shower and eyewash system site surveys. These sessions provide hands-on employee training, reference materials, training guides and other strategies for ensuring ANSI/ISEA compliance and providing the safest workplace possible.
Safety is a Work in Progress
As worksites, operations, employees—and hazards—change, emergency shower equipment should be closely evaluated. Keeping a close watch on ongoing maintenance, placement, testing and employee training will help ensure the highest levels of worksite and employee safety.
This article originally appeared in the July/August 2022 issue of Occupational Health & Safety.