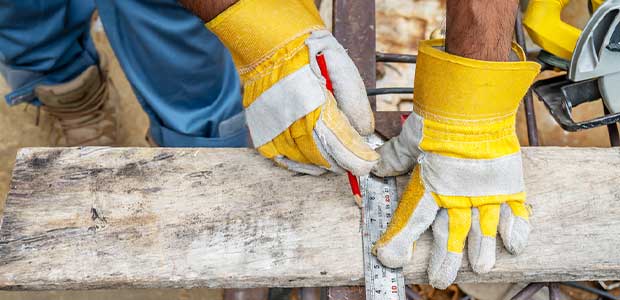
Cutting Edge Technology Can Protect Your Workers from Cutting Edges
New advancements can keep workers safe.
- By John Heniff
- May 01, 2022
According to the Ohio Bureau of Workers’ Compensation, cuts and lacerations make up approximately 30 percent of workplace injuries. Since these injuries are so common, protecting your workers is critical whether their job involves manufacturing, metal stamping, construction or any other industrial work. The good news is new technologies in cut resistance are making it easier than ever to protect workers while keeping them comfortable and compliant.
Problems with Some Cut-Resistant Gloves
Workplace studies have found that over 70 percent of hand injuries occurred when the worker wasn’t wearing gloves. The reasons workers might take off their gloves can vary. They may do it because the gloves trap heat against their skin, cause irritation, or just feel uncomfortable to the point where they can’t do their job efficiently. Sometimes they forget to put them back on when they’ve been off for a break or they just decide to work without them. They may also experience painful and annoying contact dermatitis. This can be caused when the fiberglass, steel or basalt inner cores used to achieve high levels of cut-resistance begin to wear down to the point of breaking and irritating a worker’s skin.
New Technology—Coreless ANSI Cut Level A5 and A6 Protection
Coreless material has become popular with workers in recent years due to its cool comfort and cut protection without irritation. Infused with strength-enhancing micro particles to provide cut resistance without the core, new advancements in this technology have gone beyond the original cut levels of ANSI Cut Level A4 and have gone higher without sacrificing comfort. Coreless technology offers a lightweight and soft feel that keeps hands cool even while working in heavy-duty environments like an appliance or automotive manufacturing facility. These new materials are 30 percent lighter than comparable fabrics with the same cut level, but they don’t cause irritation or discomfort.
The Lightest and Most Versatile Cut Resistance You’ve Ever Worn
One of the biggest technological advancements in recent years is specially blended yarns that create a combination of high level of protection in incredibly light and comfortable materials. Certain yarns are over 50 percent lighter than comparable HPPE of the same cut level. They are specially engineered to feel cooler with flexibility like a second layer of skin. And with cut levels as high as ANSI Cut Level A9, workers can count on it for protection from some of the sharpest hazards found in their work area.
Improved Protection for Hot and Dangerous Industries Like Glass Manufacturing
New yarn wrapping technology can be especially beneficial for industries that are hot and dangerous, such as glass manufacturers. In the past, jobs in a glass plant often required protective gear that was heavy, thick and itchy. On top of that, workers would commonly roll their sleeves up or take gloves off to provide relief from hot conditions inside the plants.
Beyond sleeves and gloves, older cut-resistant “sweaters” suffered from similar issues. Workers toiled in hot, heavy and itchy garments that also had sizing inconsistencies that left some unprotected in crucial areas. To protect the upper body, new materials have been used to create garments up to 30 percent lighter than comparable equivalents. These new cut-resistant tops are designed with higher cut resistance to protect critical areas, such as at the abdomen which can come into contact with glass when handling or inspecting.
Trusting New Technology
These new materials are so light and cool it can be surprising to learn they still effectively protect workers from cuts. It’s natural to wonder how such light and comfortable fabrics are as good as their thicker counterparts. The way to prove this is through a rigorous cut testing process. Here’s an example of a three-step testing process to ensure our gloves and sleeves will get the job done.
Machine Testing. First, a state-of-the-art testing machine is carefully calibrated to drag a sharpened blade across a piece of material (in accordance with ASTM F2992). Once a cut is observed, the amount of pressure is recorded to determine the fabric’s cut level.
Lab Testing. Once the first test is completed, the fabric is sent to an independent and accredited third-party laboratory to validate the results. The test is performed again with the same type of machine to ensure the results are accurate.
Edge Testing. After both tests on the fabric, gloves and sleeves endure an additional test to encounter hazards that can be found on a jobsite. The glove or sleeve fabric is often filled with closed-cell foam or another similar material to mimic the weight and density of a worker’s hand or arm. An edge-test involves running the fabric across a hazard (such as the sharp edge of a stamped metal part) with even greater force than a worker typically would apply. This way, manufacturers confidently know the shell can hold up to hazards even under the strongest amounts of pressure.
If you find a glove or sleeve that has passed these tests, you can confidently know that it will live up to its safety rating and protect your workers, even if it is more lightweight and breathable than anything you’ve seen before.
Whether it’s innovative shells or versatile yarn-wrapping techniques, it’s important to know the latest and greatest technologies so your teams aren’t using yesterday’s gear. Give your workers the best in both comfort and safety to keep them compliant.
This article originally appeared in the May 2022 issue of Occupational Health & Safety.