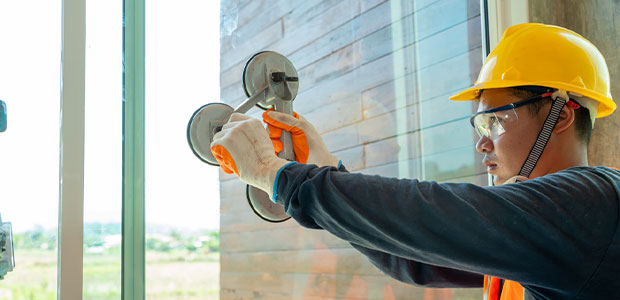
Incident investigations are a Challenge but Increase Contractors' Safety
Taking advantage of teachable moments and harboring a safe environment to discuss dangers are key to avoiding preventable loss.
- By Shereen Hashem
- Feb 08, 2022
The term "incident investigation" can sometimes make employees nervous or hesitant to participate in important safety assessments. Nevertheless, getting to the bottom of a construction site incident is the best way to prevent similar situations in the future. Companies can overcome employee concerns and gather more complete information that results in valuable action items by planning and solidly executing incident investigations, according to an article.
"If we don't understand why an incident happened, we have no chance of preventing recurrence, and that's really what we're trying to do," said Rob Dahl, risk and safety specialist at CSDZ.
Jobsite incidents are not just a matter of chance, he said. Proper investigations could uncover opportunities to improve underlying issues all the way up the employee chain. Areas that might need tweaking include management systems, work procedures, communication, incorrect work equipment and inadequate protective equipment." Conducting thorough incident investigations demonstrate a commitment to employee safety. Plus, investigations can help an employer's bottom line. For example, gaining full knowledge of an incident can prevent fraudulent workers compensation filings or insurance claims.
When to Investigate
All incidents should be analyzed, Dahl said. Even those with minor consequences shouldn't be dismissed. The more incidents that builders investigate, the more data that they have at their fingertips to reach conclusions that prevent a future incident. Labeling an incident as a "fluke" or "freak accident" isn't helpful because the team then believes they couldn't have done anything to prevent it and gives up on learning anything from it, Dahl said. About 80 percent of workplace incidents are caused by human error and 20 percent involve equipment failures, according to a Department of Energy Study. An accident doesn't have to be serious to constitute a learning opportunity.
Empowering Workers to Report
Incident prevention begins with recognizing hazards and risks. Then, employees must report risky behaviors or incidents so managers can launch an investigation. Only a small percentage of workers are willing to speak up to another employee about an unsafe act or report one to a supervisor, Dahl said. Many incidents go unreported due to systemic inadequacies in workplace “customs or culture.” Of the human error incidents cited in the Department of Energy study, about 70 percent are because of systemic weaknesses. Only 30 percent are caused by the individual worker. Employees involved in incidents are often blamed or assumed to have poor judgment. Rather, many make the "least worst" decision based on work pressures, culture or a supervisor's tendency to overlook issues, Dahl said.
Planning for Success
Traditional approaches to incident investigations often fail, Dahl said. Generally, companies don't provide sufficient training on how to conduct investigations. This results in poorly crafted and executed analyses that lack positive impact. Companies should have clear forms and processes for reporting incidents and conducting investigations. “Building trust with investigation participants is key, as is separating them from other interviewees and treating the situation like an information gathering session instead of an interrogation.”
Supervisors miss a chance to improve workplace safety, culture and operations if they don't communicate incident investigation findings to other employees.