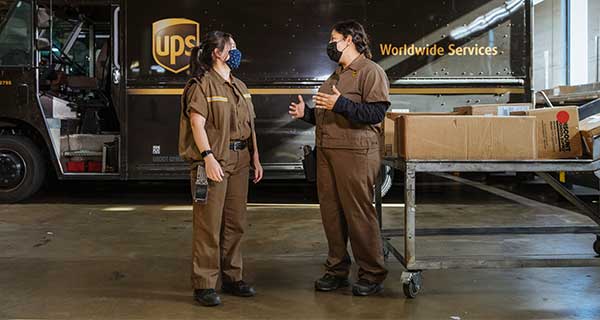
Three Things to Learn about Safety from Front-Line Employees
David Keeling, Vice President of Global Health and Safety at UPS, shares his experience working with over half a million front-line employees.
- By Dave Keeling
- Jun 02, 2021
I was a University of Louisville student when I started working for UPS in 1985 as a part-time package handler on the night shift. I soon learned from experience the importance of safety and wellness. I quickly understood how adequate sleep and hydration can positively affect your day. I learned the importance of attitude and focus. And I quickly began to value the little things that allow you to leave your shift as safe and healthy as when you arrived.
I’ve maintained that focus on safety in the 36 years since. But as I made my way into mid-level and eventually senior management jobs, I got further away from the first-hand experience front-line employees have with the operation. Jobs, facilities and equipment continuously change and evolve, and I’ve found it increasingly important to seek out the input and perspective of frontline employees who “touch cardboard” (in UPS parlance) on actions, small and large, that we can take to help keep employees safe.
That’s one reason UPS’s over 3,200 Comprehensive Health and Safety Process (CHSP) committees are so important. These committees involve UPS front-line employees, along with managers, to help keep their co-workers safe at their facilities. Among other things, they create and recommend process and equipment changes that are frequently implemented across our operations. With nearly half a million employees delivering 5.5 billion packages a year, what seems like a small change recommended by a local CHSP Committee – a modification to a package car handrail, a lowered step-bumper – can and does have a major effect.
With that in mind, here are a few things about safety that I’ve learned, or been reminded of, by continuing to listen to our front-line employees and CHSP Committees:
Listen to your front-line people. No one knows the job better than they do. Even when a manager has experience in the job in question, certain fundamentals can change over time. When you get an entire CHSP Committee involved, the safety solutions will almost always be better than if a decision were made in a silo.
Trust is hard won and easily lost. Inconsistency is one of the greatest enemies of a safe culture. Rules must be applied evenly and across all work groups, and management above all must be held to the highest of safety standards. Our employees are fanatical about serving our customers – it’s critical to let them know their efforts to do that, safely, are noticed, encouraged and appreciated.
What you incentivize matters. People may not always not do what you ask, but they will almost always do what you incent. Proactively look for ways to acknowledge good decisions and safe behaviors. Be specific as to what you are recognizing employees for, and be timely in your recognition. Genuine, positive reinforcement of good decisions and behaviors is more effective than punishment of bad decisions or behaviors -- and is much more likely to lead to long-term positive behavior and increased trust.
About the Author
David Keeling is Vice President – Global Health & Safety at UPS. He has spent over 20 years in health and safety at UPS at the local, regional and corporate level, and currently has responsibility for all UPS global health and safety operations.